A sintering oven, also known as a sintering furnace, is a specialized piece of equipment used in the sintering process, which involves compacting and fusing powdered materials into a solid mass without melting them. This process is widely used in industries such as manufacturing, metallurgy, and ceramics to produce components like gears, bearings, and electrical contacts. The sintering oven plays a critical role in achieving the desired material properties, such as high density, dimensional precision, and functional performance. The process involves heating the material to a temperature below its melting point, allowing atomic diffusion to bond particles together, often under vacuum or controlled atmospheric conditions. Sintering ovens are versatile and can handle various materials, including metals, ceramics, and polymers, making them essential for producing complex, high-strength parts.
Key Points Explained:
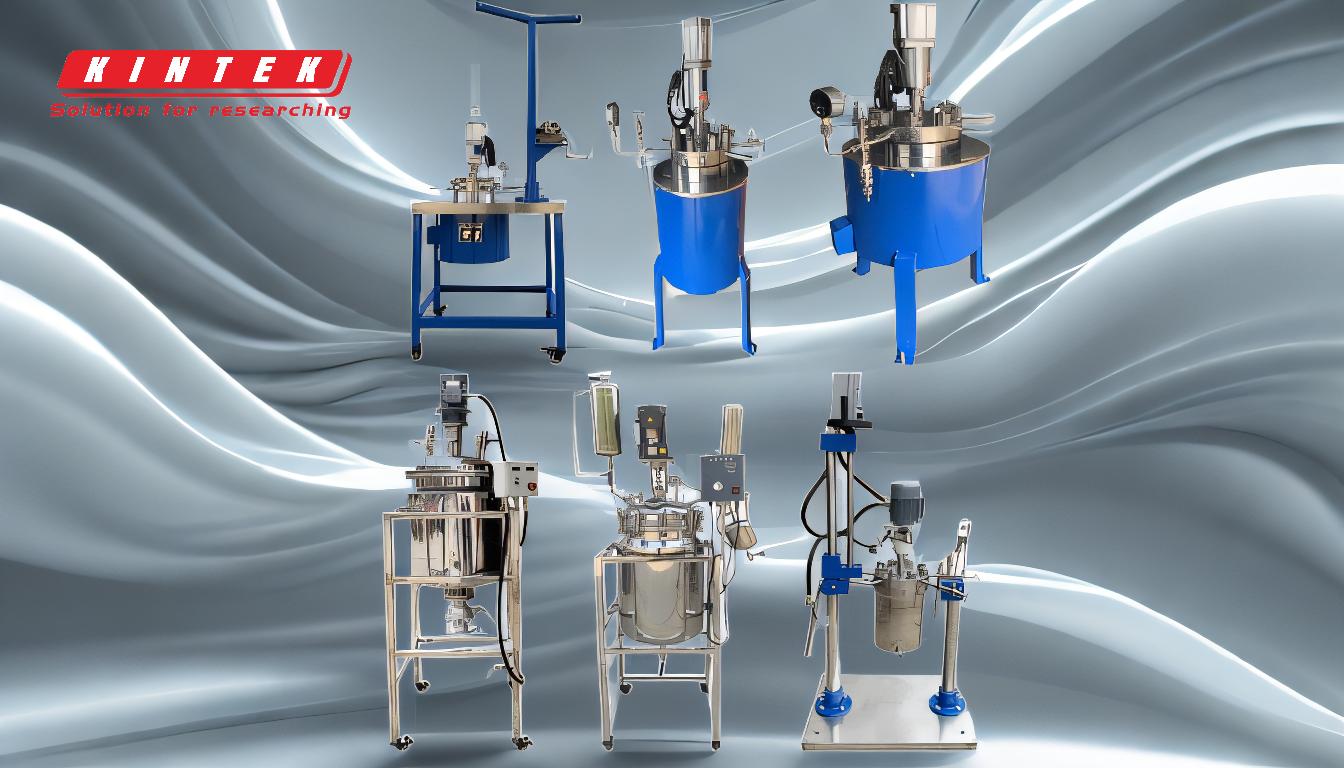
-
Definition and Purpose of a Sintering Oven:
- A sintering oven is a furnace designed to heat powdered materials to a temperature below their melting point, enabling the particles to bond through atomic diffusion.
- The primary purpose is to create solid, high-density components with precise dimensions and functional properties, such as strength and durability.
-
How Sintering Works:
- The process begins with compacting loose powder into a desired shape, forming a weak, oversized component.
- The component is then placed in the sintering oven, where it is heated to a specific temperature, causing the particles to fuse without melting.
- This thermal fusion removes pores and binds the particles, resulting in a solid, full-strength part.
-
Types of Sintering Processes:
- Liquid-Phase Sintering: Involves adding a small amount of material that melts at the sintering temperature, forming a liquid that helps rearrange particles and remove pores.
- Vacuum Sintering: Conducted in a vacuum to eliminate atmospheric gases, ensuring a clean environment for the material to sinter without contamination.
-
Applications of Sintering Ovens:
- Sintering ovens are used in various industries to produce components such as gears, bearings, pulleys, rotors, and electrical contacts.
- The process is cost-effective and efficient, making it ideal for mass production of complex parts.
-
Advantages of Sintering:
- Cost-Effective: Requires less energy compared to melting processes.
- Versatility: Can be used with a wide range of materials, including metals, ceramics, and polymers.
- Precision: Produces parts with high dimensional accuracy and minimal porosity.
-
Key Features of Sintering Ovens:
- Temperature Control: Precise temperature regulation is crucial for achieving the desired material properties.
- Atmosphere Control: Some ovens operate under vacuum or controlled atmospheres to prevent oxidation or contamination.
- Uniform Heating: Ensures consistent sintering across the entire component.
-
Material Considerations:
- The choice of material and sintering parameters (temperature, pressure, and time) depends on the desired properties of the final product.
- Common materials include stainless steel, tungsten, and ceramics, each requiring specific sintering conditions.
-
Post-Sintering Characteristics:
- After sintering, the part exhibits micro-porosity, high dimensional precision, and functional performance if the specifications are met.
- The process can achieve near-full density, depending on the material and sintering method used.
By understanding the role and functionality of a sintering oven, manufacturers can optimize the sintering process to produce high-quality, durable components tailored to specific applications.
Summary Table:
Key Aspect | Details |
---|---|
Definition | A furnace for heating powdered materials below melting point to bond particles. |
Purpose | Creates solid, high-density components with precise dimensions and strength. |
Process | Compacts powder, heats to fuse particles without melting, and removes pores. |
Types | Liquid-phase sintering, vacuum sintering. |
Applications | Gears, bearings, electrical contacts, and more. |
Advantages | Cost-effective, versatile, and produces high-precision parts. |
Key Features | Precise temperature control, atmosphere control, uniform heating. |
Materials | Metals, ceramics, polymers (e.g., stainless steel, tungsten). |
Post-Sintering | High dimensional precision, micro-porosity, and functional performance. |
Optimize your component production with a sintering oven—contact us today to learn more!