A split tube furnace is a specialized heating device designed with a cylindrical tube that is split lengthwise, allowing easy access to the furnace chamber. This unique design simplifies the installation and removal of work tubes and reaction vessels, making it ideal for applications requiring frequent sample changes or complex setups. Commonly used in thermal analysis, catalyst testing, crystal growth, and material testing, split tube furnaces are versatile and efficient tools in laboratory and industrial settings. Their ability to accommodate larger or more intricate setups compared to non-split furnaces makes them invaluable for processes like pyrolysis, chemical vapor deposition, and graphitization.
Key Points Explained:
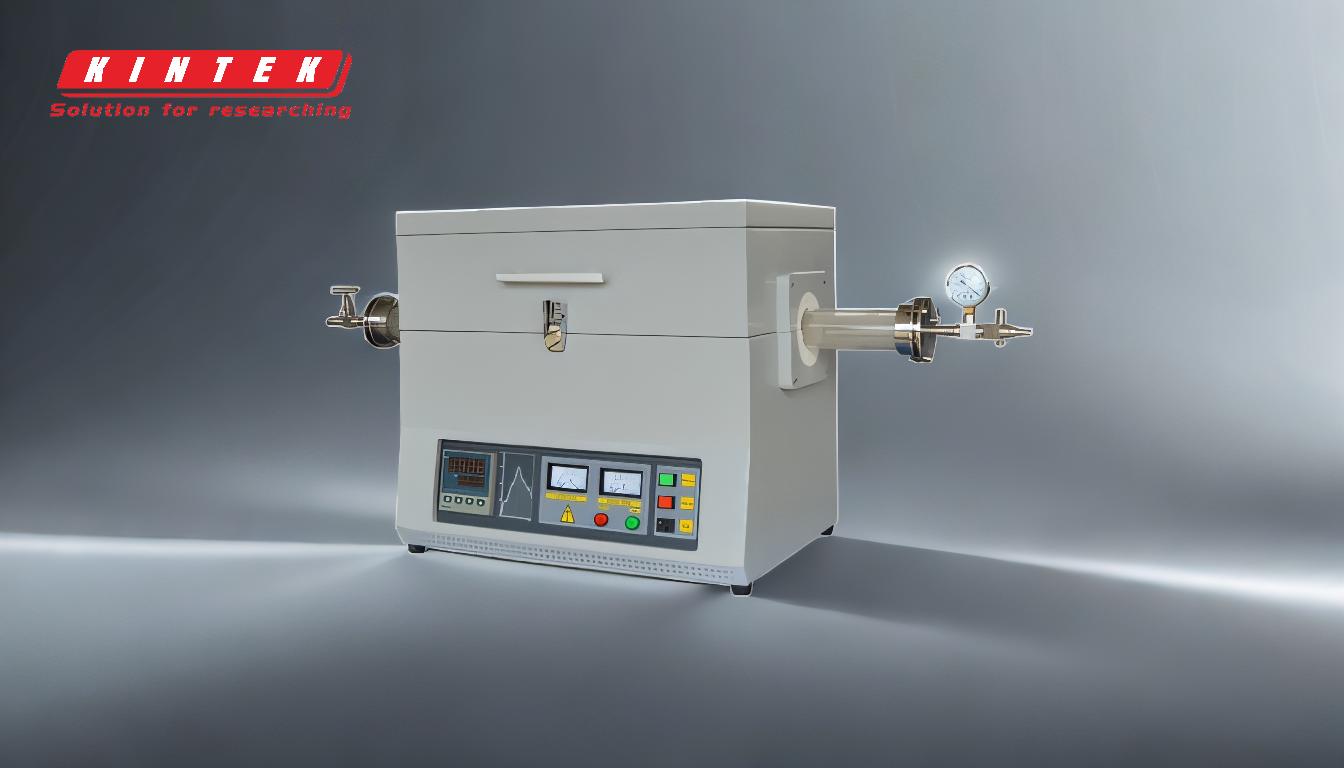
-
Design and Structure of a Split Tube Furnace:
- A split tube furnace consists of a cylindrical tube that is split lengthwise, enabling the furnace to open and close easily. This design is typically constructed in two halves, joined with hinges and equipped with pneumatic dampening struts for smooth operation.
- The split design allows for quick access to the furnace chamber, making it easier to install or remove work tubes, reaction vessels, and other components with complex ends or fittings that would be difficult to handle in a non-split furnace.
-
Primary Benefits:
- The main advantage of a split tube furnace is its ability to open, which significantly simplifies the process of loading and unloading samples or equipment. This feature is particularly useful in applications requiring frequent changes or complex setups.
- The design reduces downtime and enhances efficiency, making it a preferred choice for laboratories and industries where time and precision are critical.
-
Applications:
- Split tube furnaces are widely used in various applications, including:
- Thermal Analysis: For studying material properties under controlled heating conditions.
- Catalyst Testing: To evaluate the performance of catalysts in chemical reactions.
- Crystal Growth: For growing high-quality crystals under precise temperature conditions.
- Material Testing: Such as tensile testing, where materials are subjected to mechanical stress.
- Specialized Processes: Including pyrolysis, chemical vapor deposition, and graphitization, which require controlled heating environments.
- They are also integrated into rotating, oscillating, and gradient tube furnaces, further expanding their utility in advanced research and industrial processes.
- Split tube furnaces are widely used in various applications, including:
-
Versatility and Efficiency:
- The split tube furnace's design makes it highly versatile, capable of accommodating a wide range of sample sizes and configurations. This flexibility is particularly beneficial in research and development settings where experimental setups vary significantly.
- Its efficiency in handling complex setups and reducing operational downtime makes it a valuable tool for laboratories and industries focused on innovation and precision.
-
Comparison with Non-Split Tube Furnaces:
- Unlike non-split tube furnaces, which require samples or equipment to be inserted through the ends of the tube, split tube furnaces allow for side access. This feature is especially advantageous when dealing with large or irregularly shaped samples, as well as setups involving multiple connections or fittings.
- The ease of access provided by the split design minimizes the risk of damaging sensitive equipment or samples during installation or removal.
In summary, a split tube furnace is an essential tool for applications requiring frequent sample changes, complex setups, or precise temperature control. Its unique design and versatility make it a preferred choice for researchers and industries working on advanced materials, chemical processes, and thermal analysis.
Summary Table:
Aspect | Description |
---|---|
Design | Cylindrical tube split lengthwise for easy access to the furnace chamber. |
Primary Benefits | Simplifies loading/unloading, reduces downtime, and enhances efficiency. |
Applications | Thermal analysis, catalyst testing, crystal growth, material testing, and more. |
Versatility | Accommodates large or intricate setups, ideal for R&D and industrial processes. |
Comparison to Non-Split | Allows side access, minimizing risk of damage to samples or equipment. |
Ready to enhance your lab's efficiency with a split tube furnace? Contact us today to learn more!