Physical Vapor Deposition (PVD) coatings are widely used across various industries due to their ability to enhance the durability, functionality, and aesthetic appeal of components. PVD coatings involve the deposition of thin films of materials onto surfaces through a vacuum-based process. These coatings are known for their excellent hardness, wear resistance, and corrosion resistance. Examples of PVD coatings include Titanium Nitride (TiN), Chromium Nitride (CrN), Titanium Aluminum Nitride (TiAlN), and Titanium Boron Nitride (TiBN). These materials are chosen based on their unique properties and the specific requirements of the application, such as in aerospace, automotive, and consumer electronics.
Key Points Explained:
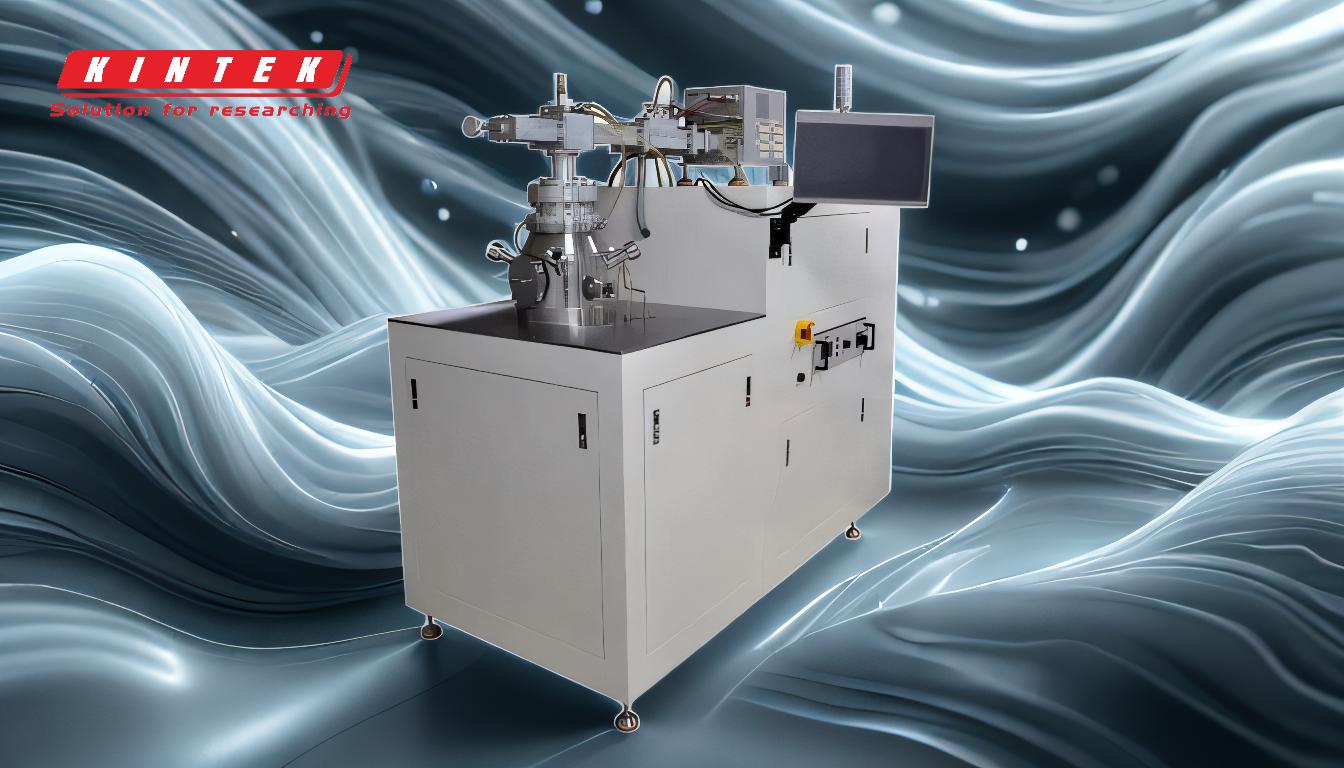
-
Common PVD Coating Materials:
- PVD coatings are made from a variety of materials, including metals, alloys, ceramics, and specialized compounds. Examples include:
- Titanium Nitride (TiN): Known for its high resistance to abrasion and corrosion, TiN is commonly used in building valves, door handles, and other surfaces requiring durability and aesthetic appeal.
- Chromium Nitride (CrN): Offers excellent wear resistance and is often used in high-performance automotive and aerospace components.
- Titanium Aluminum Nitride (TiAlN): Provides enhanced thermal stability and is suitable for high-temperature applications.
- Titanium Boron Nitride (TiBN): Combines the properties of titanium and boron nitride, offering superior hardness and wear resistance.
- PVD coatings are made from a variety of materials, including metals, alloys, ceramics, and specialized compounds. Examples include:
-
Applications of PVD Coatings:
- Automotive Industry: PVD coatings are used to improve the durability and appearance of high-performance engine components, as well as for decorative purposes in auto and motorcycle interiors. They are also applied to car headlamps to create a reflective aluminum layer.
- Aerospace: Materials like gold are used in PVD coatings for aerospace electronics due to their excellent conductivity and corrosion resistance.
- Consumer Electronics: PVD coatings are applied to enhance the durability and aesthetic appeal of components such as smartphone cases and watch bands.
-
Advantages of PVD Coatings:
- Enhanced Durability: PVD coatings significantly improve the hardness and wear resistance of surfaces, making them ideal for high-stress applications.
- Corrosion Resistance: These coatings provide excellent protection against corrosion, extending the lifespan of components.
- Aesthetic Appeal: PVD coatings can be used to create a variety of finishes, including metallic and dark DLC (Diamond-like Carbon) finishes, enhancing the visual appeal of products.
- Environmental Benefits: PVD is a cleaner alternative to traditional plating methods, such as hexavalent chrome, reducing environmental impact.
-
Substrates for PVD Coatings:
- PVD coatings can be applied to a wide range of substrates, including:
- Metals: Stainless steel, aluminum, and copper.
- Plastics: Nylon and other polymers.
- Ceramics and Glass: Used in specialized applications requiring high durability and thermal stability.
- PVD coatings can be applied to a wide range of substrates, including:
-
Specialized PVD Coatings:
- In addition to common materials, specialized coatings such as carbides, nitrides, silicides, and borides are used for unique applications. For example:
- Graphite and Titanium: Often used in high-performance aerospace and automotive components.
- Diamond-like Carbon (DLC): Provides a hard, wear-resistant coating with a low friction coefficient, ideal for moving parts.
- In addition to common materials, specialized coatings such as carbides, nitrides, silicides, and borides are used for unique applications. For example:
In summary, PVD coatings offer a versatile and effective solution for enhancing the performance and appearance of various components across multiple industries. The choice of coating material depends on the specific requirements of the application, with each material offering unique benefits such as increased hardness, wear resistance, and corrosion protection.
Summary Table:
Coating Material | Key Properties | Common Applications |
---|---|---|
Titanium Nitride (TiN) | High abrasion & corrosion resistance | Building valves, door handles |
Chromium Nitride (CrN) | Excellent wear resistance | Automotive, aerospace components |
Titanium Aluminum Nitride (TiAlN) | Enhanced thermal stability | High-temperature applications |
Titanium Boron Nitride (TiBN) | Superior hardness & wear resistance | Specialized industrial uses |
Ready to enhance your components with PVD coatings? Contact us today for expert guidance!