An exothermic atmosphere is a type of controlled atmosphere created by the combustion of a fuel (such as natural gas or propane) with a limited supply of air. This process generates heat (exothermic reaction) and produces a mixture of gases, primarily nitrogen (N₂), carbon dioxide (CO₂), and small amounts of carbon monoxide (CO) and hydrogen (H₂). This atmosphere is commonly used in heat treatment processes, such as annealing, hardening, and brazing, to prevent oxidation and decarburization of metals. The composition of the exothermic atmosphere can be adjusted by varying the air-to-fuel ratio, making it versatile for different industrial applications.
Key Points Explained:
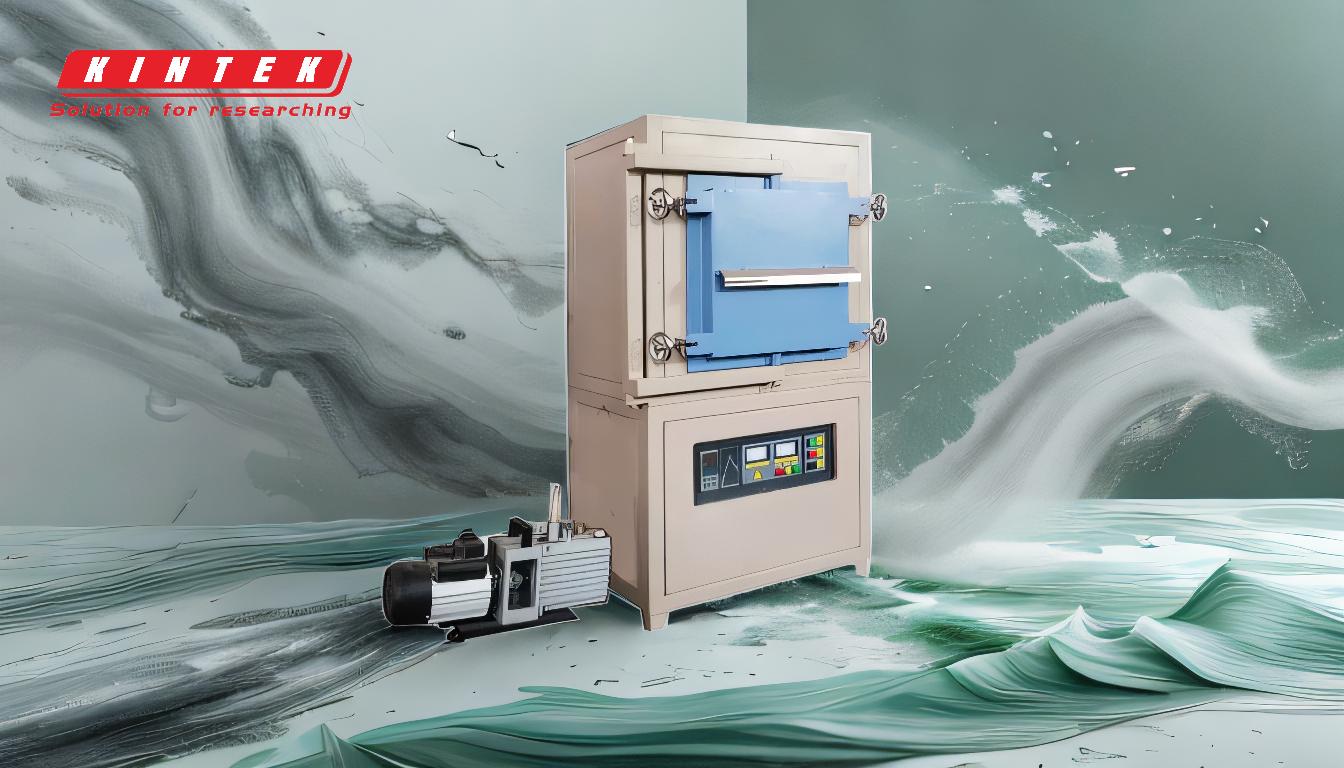
-
Definition and Formation of Exothermic Atmosphere:
- An exothermic atmosphere is formed through the partial combustion of a hydrocarbon fuel (e.g., natural gas or propane) with a restricted amount of air.
- The chemical reaction is exothermic, meaning it releases heat, and the resulting gas mixture is rich in nitrogen (N₂) and carbon dioxide (CO₂), with trace amounts of carbon monoxide (CO) and hydrogen (H₂).
-
Composition of Exothermic Atmosphere:
- The primary components of an exothermic atmosphere are:
- Nitrogen (N₂): 70–90%
- Carbon dioxide (CO₂): 5–15%
- Carbon monoxide (CO): 1–5%
- Hydrogen (H₂): 1–5%
- The exact composition depends on the air-to-fuel ratio used during combustion. A leaner mixture (more air) produces more CO₂ and less CO, while a richer mixture (less air) increases the concentration of CO and H₂.
- The primary components of an exothermic atmosphere are:
-
Applications in Heat Treatment:
- Exothermic atmospheres are widely used in heat treatment processes to protect metals from oxidation and decarburization.
- Common applications include:
- Annealing: Softening metals to improve machinability.
- Hardening: Increasing the hardness and strength of metals.
- Brazing: Joining metals using a filler material.
- The controlled atmosphere ensures a clean, oxide-free surface, which is critical for achieving desired material properties.
-
Advantages of Exothermic Atmospheres:
- Cost-effective: The process uses readily available fuels and air, making it economical.
- Versatile: The composition can be adjusted to suit different metals and processes.
- Protective: Prevents oxidation and decarburization, ensuring high-quality results.
- Safe: The low concentration of flammable gases (CO and H₂) reduces the risk of explosions.
-
Limitations and Considerations:
- Carbon control: The presence of CO and CO₂ can affect the carbon content of the metal, which may not be suitable for all applications.
- Equipment requirements: Generators and control systems are needed to produce and maintain the atmosphere.
- Environmental impact: Combustion produces CO₂, contributing to greenhouse gas emissions.
-
Comparison with Other Controlled Atmospheres:
- Exothermic atmospheres are often compared to endothermic and nitrogen-based atmospheres.
- Endothermic atmospheres are richer in CO and H₂, making them more suitable for processes requiring carbon enrichment.
- Nitrogen-based atmospheres are inert and used when oxidation prevention is critical without carbon interaction.
- The choice of atmosphere depends on the specific requirements of the heat treatment process.
- Exothermic atmospheres are often compared to endothermic and nitrogen-based atmospheres.
By understanding the principles and applications of exothermic atmospheres, manufacturers can optimize their heat treatment processes to achieve desired material properties while minimizing costs and environmental impact.
Summary Table:
Aspect | Details |
---|---|
Definition | Formed by partial combustion of hydrocarbon fuels with limited air supply. |
Primary Components | - Nitrogen (N₂): 70–90% - Carbon dioxide (CO₂): 5–15% - Carbon monoxide (CO): 1–5% - Hydrogen (H₂): 1–5% |
Applications | Annealing, hardening, brazing to prevent oxidation and decarburization. |
Advantages | Cost-effective, versatile, protective, and safe. |
Limitations | Carbon control challenges, equipment requirements, environmental impact. |
Comparison | Richer in N₂ and CO₂ compared to endothermic and nitrogen-based atmospheres. |
Discover how exothermic atmospheres can enhance your heat treatment processes—contact our experts today!