Batch pyrolysis is a thermal decomposition process that occurs in the absence of oxygen, where organic materials are heated in a sealed, fixed-batch reactor to break down into smaller molecules, producing gases, liquids (bio-oil), and solid residues (char). This process is widely used in waste management, energy production, and chemical synthesis due to its ability to convert various feedstocks into valuable products. The reactor design, heat transfer mechanisms, and operational parameters play a critical role in determining the efficiency and output of the pyrolysis process.
Key Points Explained:
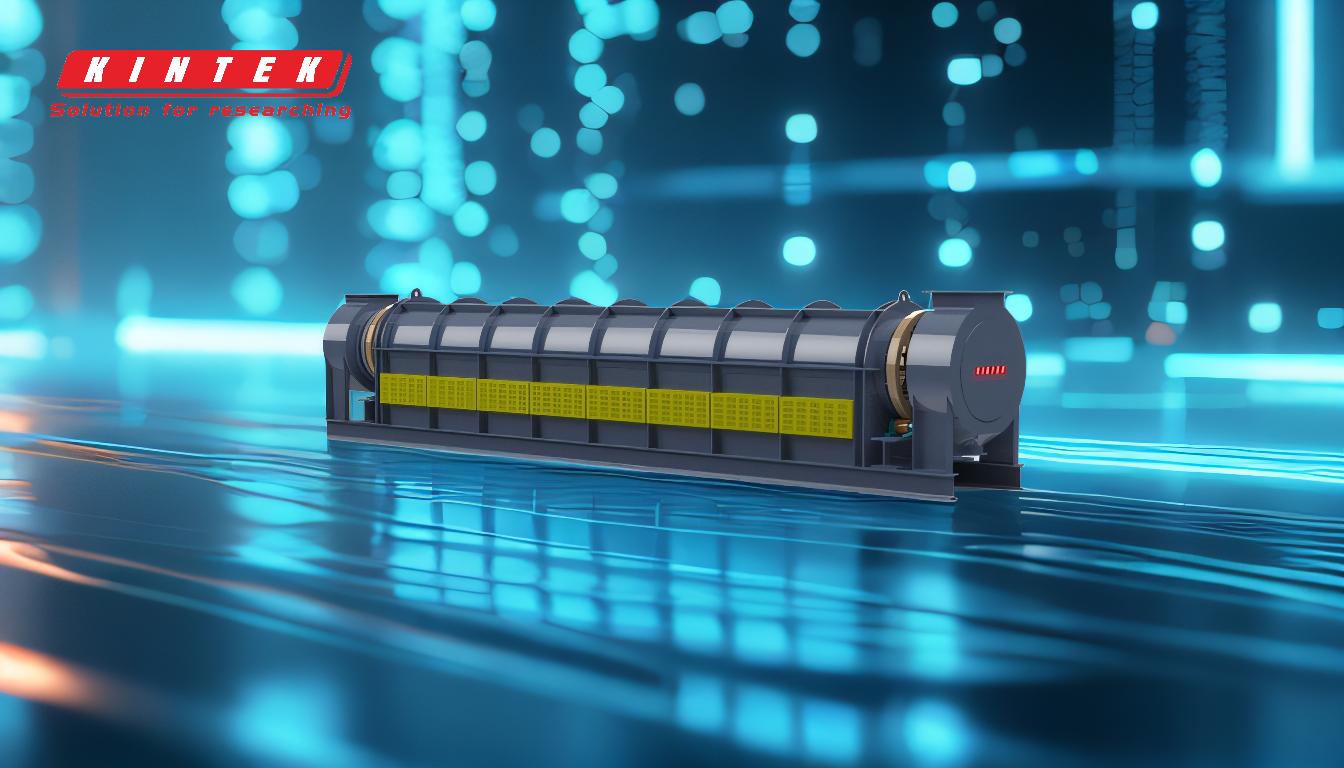
-
Definition and Process of Batch Pyrolysis:
- Batch pyrolysis involves loading a fixed amount of feedstock into a sealed reactor, heating it in the absence of oxygen, and allowing thermal decomposition to occur. The process produces three main outputs: bio-oil, syngas, and char.
- The absence of oxygen prevents combustion, ensuring that the feedstock undergoes decomposition rather than burning. This makes batch pyrolysis ideal for processing materials like biomass, plastics, and rubber.
-
Role of the Pyrolysis Reactor:
- The pyrolysis reactor is the core component of the system, where the thermal decomposition of the feedstock takes place. It is designed to withstand high temperatures and maintain a sealed environment to prevent oxygen ingress.
- Reactors come in various designs, such as fixed-bed, fluidized-bed, and wire-mesh reactors, each suited for specific applications and feedstock types.
-
Types of Batch Pyrolysis Reactors:
- Fixed-Bed Reactors: These are simple, sealed vessels where the feedstock is placed on a bed and heated uniformly. Heat transfer occurs through the walls of the reactor, ensuring consistent thermal decomposition. They are ideal for small-scale operations and research purposes.
- Wire-Mesh Reactors: These reactors use metal grids to hold the sample, allowing for rapid heating and minimal secondary reactions. They are commonly used for fast pyrolysis and experimental studies, particularly to investigate the initial stages of pyrolysis like devolatilization and gasification.
-
Components of a Pyrolysis Reactor System:
- The system typically consists of four main parts:
- Driving Device: Powers the rotation or movement of the reactor.
- Base: Provides structural support for the reactor.
- Main Furnace: Houses the reactor and supplies the necessary heat.
- Casing: Encloses the system, ensuring safety and preventing heat loss.
- The system typically consists of four main parts:
-
Advantages of Batch Pyrolysis:
- Energy Stability: Batch reactors are ideal for processes requiring consistent energy input and output.
- Versatility: They can handle a wide range of feedstocks, including biomass, plastics, and rubber.
- Simplicity: The design is straightforward, making it easy to operate and maintain.
-
Applications of Batch Pyrolysis:
- Waste Management: Converts organic waste into useful products, reducing landfill dependency.
- Energy Production: Produces bio-oil and syngas, which can be used as renewable energy sources.
- Chemical Synthesis: Generates valuable chemicals and materials from waste feedstocks.
-
Challenges and Considerations:
- Heat Transfer Efficiency: Ensuring uniform heat distribution within the reactor is critical for optimal decomposition.
- Feedstock Preparation: The size and moisture content of the feedstock must be controlled to achieve efficient pyrolysis.
- Safety: The sealed nature of the reactor requires robust safety measures to prevent leaks or explosions.
In summary, batch pyrolysis is a versatile and efficient process for converting organic materials into valuable products. The design and operation of the pyrolysis reactor are crucial for ensuring optimal performance, safety, and output quality. By understanding the principles and components of batch pyrolysis, stakeholders can effectively utilize this technology for sustainable waste management and energy production.
Summary Table:
Aspect | Details |
---|---|
Process | Thermal decomposition of organic materials in the absence of oxygen. |
Outputs | Bio-oil, syngas, and char. |
Reactor Types | Fixed-bed, wire-mesh, and fluidized-bed reactors. |
Key Components | Driving device, base, main furnace, and casing. |
Advantages | Energy stability, versatility, and simplicity. |
Applications | Waste management, energy production, and chemical synthesis. |
Challenges | Heat transfer efficiency, feedstock preparation, and safety measures. |
Discover how batch pyrolysis can transform your waste into valuable resources—contact our experts today!