A calciner is a specialized piece of equipment used in chemistry and industrial processes to carry out calcination, which involves heating materials to high temperatures to induce chemical dissociation or remove volatile components. This process is critical in the production of inorganic materials, such as converting calcium carbonate into calcium oxide and carbon dioxide, or removing moisture from substances like borax. Calcination is widely used in industries like cement production, metal refining, and chemical manufacturing.
Key Points Explained:
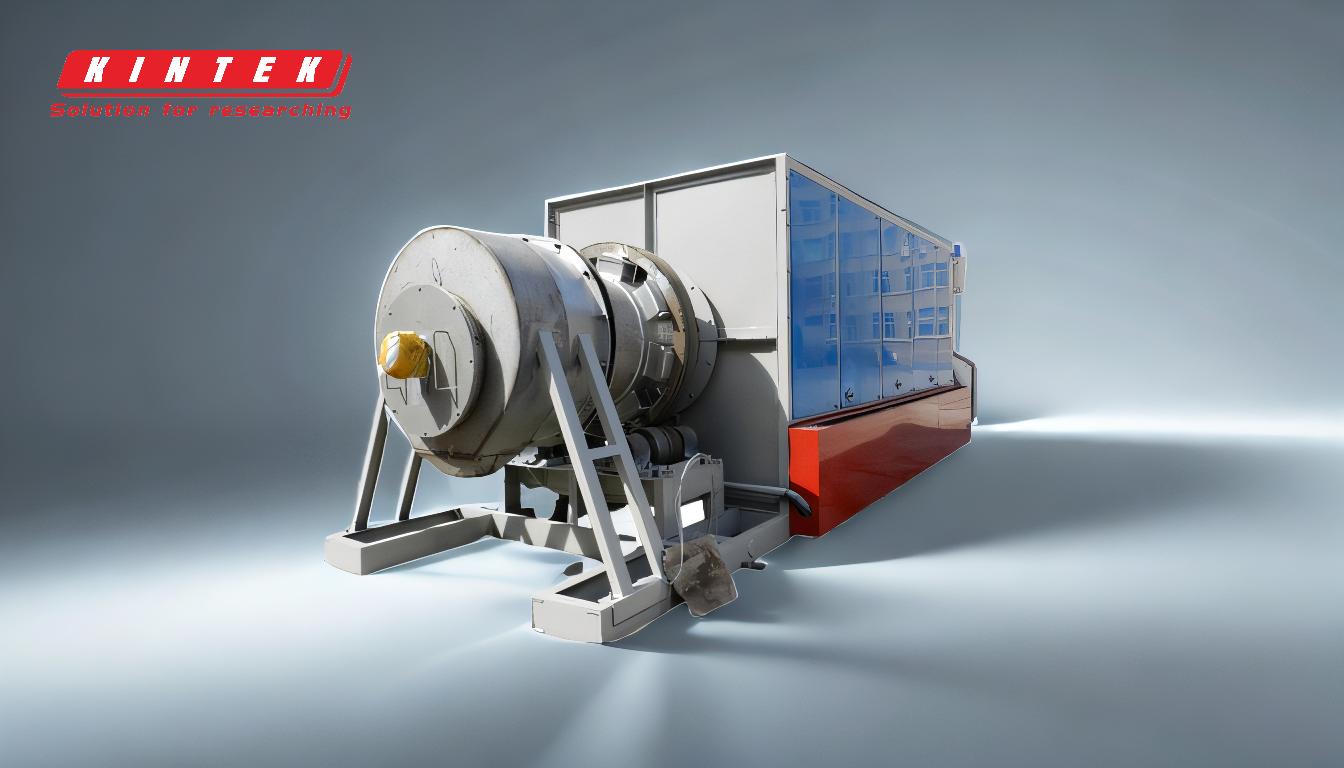
-
Definition of Calcination:
- Calcination is a thermal treatment process where materials are heated to high temperatures (typically below their melting points) to achieve chemical dissociation or remove volatile components.
- Example: Heating calcium carbonate (CaCO₃) to produce calcium oxide (CaO) and carbon dioxide (CO₂).
-
Purpose of Calcination:
- Chemical Dissociation: Breaking down compounds into simpler substances, such as decomposing carbonates, hydroxides, or sulfates.
- Moisture Removal: Eliminating bound water or other volatile impurities from materials like borax or gypsum.
- Phase Transformation: Changing the physical or chemical properties of materials, such as converting ores into oxides for metal extraction.
-
Types of Materials Processed in a Calciner:
- Inorganic Compounds: Calcium carbonate, magnesium carbonate, and other carbonates.
- Hydrated Minerals: Gypsum (CaSO₄·2H₂O) to produce anhydrous calcium sulfate.
- Metallic Ores: Used in metal refining to convert ores into oxides for further processing.
-
Applications of Calcination:
- Cement Production: Calcining limestone to produce lime (CaO), a key ingredient in cement.
- Metal Refining: Extracting metals like aluminum and zinc from their ores.
- Chemical Manufacturing: Producing industrial chemicals like sodium carbonate or titanium dioxide.
- Environmental Applications: Treating waste materials to remove harmful components.
-
Calciner Design and Operation:
- Types of Calciners: Rotary kilns, fluidized bed calciners, and vertical shaft calciners.
- Heat Source: Typically fueled by natural gas, oil, or electricity, depending on the material and process requirements.
- Temperature Control: Precise temperature regulation is critical to ensure the desired chemical reactions occur without damaging the material.
-
Advantages of Calcination:
- Efficient removal of volatile components.
- Production of high-purity materials.
- Enables the extraction of metals and production of industrial chemicals.
-
Challenges in Calcination:
- High energy consumption due to the need for sustained high temperatures.
- Potential release of harmful gases, such as CO₂, requiring proper gas handling systems.
- Risk of material degradation if temperature control is not precise.
In summary, a calciner is an essential tool in chemistry and industry for processing materials through high-temperature treatment. Its applications range from cement production to metal refining, making it a cornerstone of modern industrial processes. Understanding its operation, design, and applications is crucial for anyone involved in the procurement or use of such equipment.
Summary Table:
Aspect | Details |
---|---|
Definition | Thermal treatment process for chemical dissociation or volatile removal. |
Purpose | Chemical dissociation, moisture removal, phase transformation. |
Materials Processed | Inorganic compounds, hydrated minerals, metallic ores. |
Applications | Cement production, metal refining, chemical manufacturing, environmental. |
Types of Calciners | Rotary kilns, fluidized bed calciners, vertical shaft calciners. |
Advantages | Efficient volatile removal, high-purity materials, metal extraction. |
Challenges | High energy consumption, gas emissions, precise temperature control. |
Learn how a calciner can optimize your industrial processes—contact our experts today!