Catalyst-assisted chemical vapor deposition (CVD) is a specialized form of CVD where a catalyst is used to enhance or enable the chemical reactions that deposit a thin film onto a substrate. This method leverages the catalytic properties of certain materials to lower the activation energy required for the deposition process, making it more efficient and controllable. The catalyst can be integrated into the substrate or introduced as a separate component, depending on the application. The process involves the transport of gaseous reactants to the substrate surface, adsorption of these reactants onto the catalyst, chemical reactions facilitated by the catalyst, and the subsequent deposition of the desired material. This technique is widely used in applications such as semiconductor manufacturing, nanotechnology, and the production of advanced materials like carbon nanotubes and graphene.
Key Points Explained:
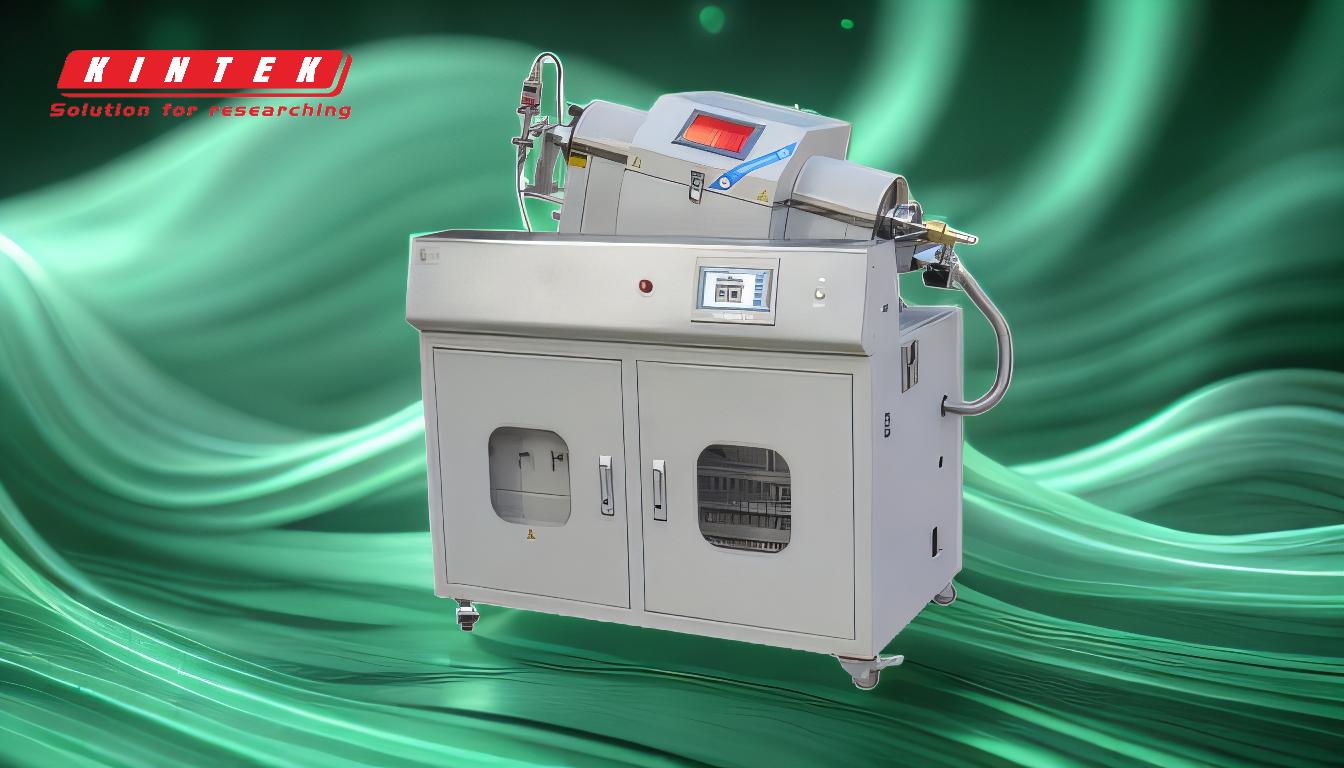
-
Definition of Catalyst-Assisted CVD:
- Catalyst-assisted CVD is a variant of the traditional CVD process where a catalyst is used to promote or control the chemical reactions that result in the deposition of a thin film. The catalyst can be a metal, metal oxide, or other materials that lower the activation energy required for the reaction, making the process more efficient and controllable.
-
Role of the Catalyst:
- The catalyst plays a crucial role in the deposition process by providing active sites for the chemical reactions to occur. It can either be embedded within the substrate or introduced as a separate component. The catalyst facilitates the decomposition of the precursor gases and the formation of the desired material on the substrate.
-
Steps Involved in Catalyst-Assisted CVD:
- Transport of Gaseous Reactants: The precursor gases are transported to the substrate surface in a controlled environment, often under vacuum or at specific pressures.
- Adsorption on the Catalyst: The gaseous reactants adsorb onto the catalyst surface, where they undergo chemical reactions.
- Surface-Catalyzed Reactions: The catalyst lowers the activation energy, enabling the reactants to form the desired material at the substrate surface.
- Nucleation and Growth: The material nucleates and grows on the substrate, forming a thin film.
- Desorption and Transport of Byproducts: Gaseous byproducts of the reaction are desorbed from the surface and transported away from the substrate.
-
Advantages of Catalyst-Assisted CVD:
- Lower Reaction Temperatures: The use of a catalyst allows the deposition process to occur at lower temperatures compared to traditional CVD, which is beneficial for temperature-sensitive substrates.
- Enhanced Control: The catalyst provides greater control over the deposition process, allowing for the precise formation of complex nanostructures.
- Versatility: This method can be used to deposit a wide range of materials, including metals, semiconductors, and carbon-based materials like graphene and carbon nanotubes.
-
Applications of Catalyst-Assisted CVD:
- Semiconductor Manufacturing: Catalyst-assisted CVD is used to deposit thin films of semiconductors, which are essential for the fabrication of electronic devices.
- Nanotechnology: This technique is widely used in the production of nanomaterials, such as carbon nanotubes and nanowires, which have applications in electronics, energy storage, and sensors.
- Advanced Materials: Catalyst-assisted CVD is employed in the synthesis of advanced materials like graphene, which has unique electrical, thermal, and mechanical properties.
-
Comparison with Other CVD Techniques:
- Thermal CVD: In thermal CVD, high temperatures are required to drive the chemical reactions, whereas catalyst-assisted CVD can achieve similar results at lower temperatures.
- Aerosol-Assisted CVD: Aerosol-assisted CVD uses an aerosol to deliver the precursor, which can be less precise compared to catalyst-assisted CVD, where the catalyst provides more controlled deposition.
- Plasma-Enhanced CVD: Plasma-enhanced CVD uses plasma to activate the precursor gases, which can be more complex and expensive compared to catalyst-assisted CVD.
In summary, catalyst-assisted chemical vapor deposition is a powerful and versatile technique that leverages the properties of catalysts to enhance the deposition of thin films and nanomaterials. Its ability to operate at lower temperatures and provide greater control over the deposition process makes it a valuable tool in various industries, from semiconductor manufacturing to nanotechnology.
Summary Table:
Aspect | Details |
---|---|
Definition | A CVD variant using a catalyst to enhance or enable chemical reactions. |
Role of Catalyst | Lowers activation energy, enabling efficient and controlled deposition. |
Key Steps | 1. Transport of reactants 2. Adsorption on catalyst 3. Surface reactions 4. Nucleation and growth 5. Desorption of byproducts |
Advantages | Lower reaction temperatures, enhanced control, and material versatility. |
Applications | Semiconductor manufacturing, nanotechnology, advanced materials like graphene. |
Comparison | More efficient than thermal CVD, more precise than aerosol-assisted CVD, and simpler than plasma-enhanced CVD. |
Discover how catalyst-assisted CVD can revolutionize your material deposition process—contact our experts today for more information!