Chemical Vapor Deposition (CVD) is a critical process in semiconductor manufacturing, enabling the production of high-quality, high-performance thin films and coatings. It involves the use of volatile precursor gases that react or decompose on a substrate surface under controlled conditions of temperature, pressure, and flow rate. This process results in the formation of a chemically bonded thin film, while volatile by-products are removed from the reaction chamber. CVD is widely used to deposit materials such as silicon compounds, carbon-based materials, and high-k dielectrics, making it essential for applications in electronics, coatings, and advanced materials.
Key Points Explained:
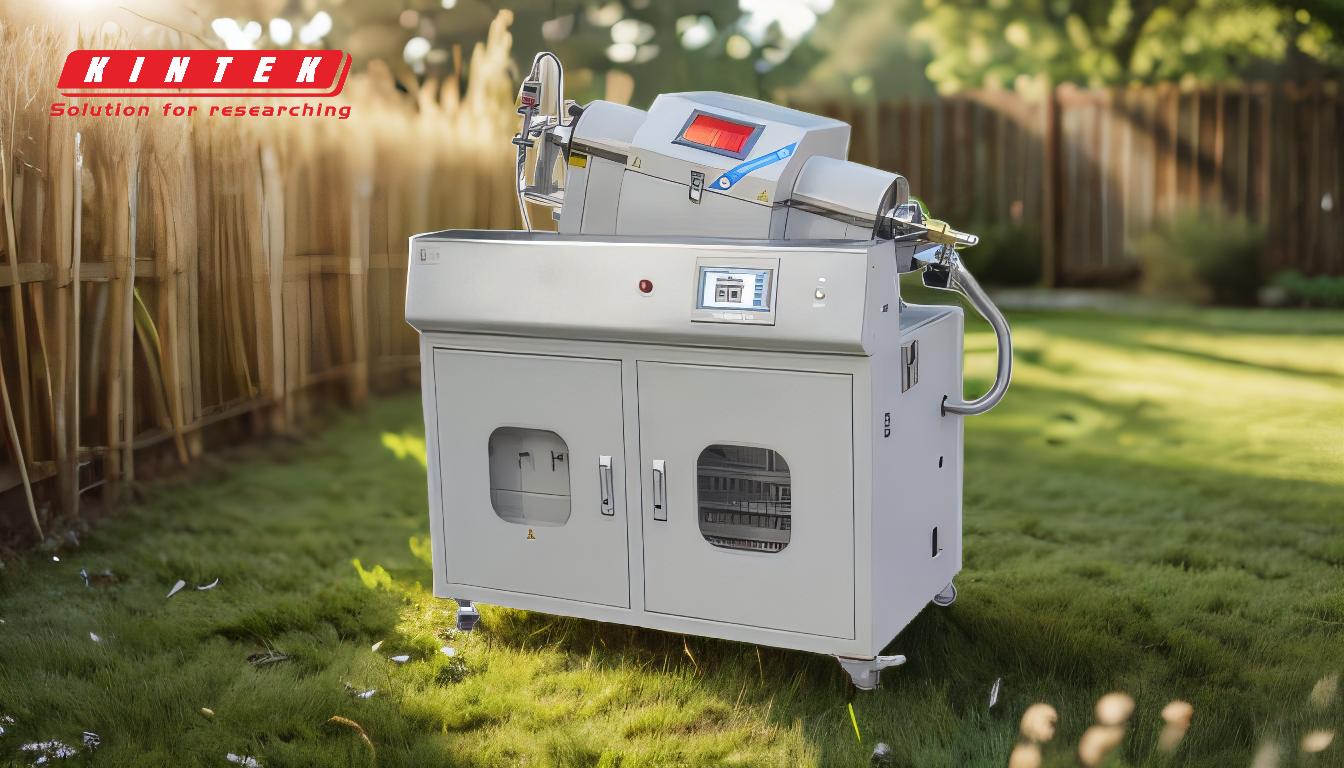
-
Definition and Purpose of CVD:
- CVD is a vacuum deposition method used to create high-quality thin films and coatings on substrates, primarily in semiconductor manufacturing.
- It is essential for producing materials like silicon dioxide, silicon carbide, graphene, and high-k dielectrics, which are critical for electronic devices, corrosion-resistant coatings, and transparent conductors.
-
Process Mechanism:
- CVD involves exposing a substrate (e.g., a wafer) to volatile precursor gases within a reaction chamber.
- These gases undergo chemical reactions (decomposition or composition) on the substrate surface, forming a solid, chemically bonded thin film.
- The process occurs under controlled conditions, including temperature, pressure, and gas flow rate, to ensure uniformity and quality.
-
Types of CVD Processes:
- Thermal CVD: Relies on high temperatures to activate the chemical reactions.
- Plasma-Enhanced CVD (PECVD): Uses plasma to lower the reaction temperature, making it suitable for temperature-sensitive substrates.
- Low-Pressure CVD (LPCVD): Operates at reduced pressures to improve film uniformity and reduce defects.
- Laser-Assisted CVD: Utilizes laser irradiation to locally heat the substrate and enable precise deposition.
- Photochemical CVD: Uses light to initiate chemical reactions, often for specialized applications.
-
Materials Deposited by CVD:
- Silicon-based materials: Silicon dioxide (SiO₂), silicon carbide (SiC), silicon nitride (Si₃N₄), and silicon oxynitride (SiON).
- Carbon-based materials: Graphene, carbon nanotubes, diamond, and carbon fibers.
- Metals and metal compounds: Tungsten (W), titanium nitride (TiN), and other high-k dielectrics.
- Fluorocarbons and other specialized coatings.
-
Advantages of CVD:
- High-quality films: Produces uniform, dense, and defect-free coatings.
- Versatility: Can deposit a wide range of materials with precise control over composition and thickness.
- Scalability: Suitable for large-area deposition, making it ideal for industrial applications.
- Conformality: Ensures even coating on complex geometries and high-aspect-ratio structures.
-
Challenges and Considerations:
- High temperatures: Some CVD processes require elevated temperatures, which may limit compatibility with certain substrates.
- Precursor selection: The choice of precursor gases affects the quality and properties of the deposited film.
- By-product management: Volatile by-products must be efficiently removed to prevent contamination and ensure film purity.
- Cost and complexity: CVD equipment and processes can be expensive and require precise control over environmental conditions.
-
Applications of CVD in Semiconductors:
- Transistors and integrated circuits: CVD is used to deposit gate oxides, interlayer dielectrics, and conductive layers.
- Protective coatings: Provides corrosion resistance and wear protection for semiconductor components.
- Advanced materials: Enables the fabrication of graphene, carbon nanotubes, and other nanomaterials for next-generation electronics.
- Optoelectronics: Used in the production of transparent conductors and light-emitting devices.
-
Future Trends in CVD:
- Low-temperature processes: Development of CVD techniques that operate at lower temperatures to expand compatibility with flexible and organic substrates.
- Atomic layer deposition (ALD) integration: Combining CVD with ALD for ultra-thin, highly controlled films.
- Sustainable precursors: Research into eco-friendly and cost-effective precursor materials.
- Nanoscale precision: Advancements in CVD to enable atomic-level control over film growth for emerging technologies like quantum computing and nanodevices.
In summary, Chemical Vapor Deposition is a cornerstone technology in semiconductor manufacturing, offering unparalleled precision and versatility in thin film deposition. Its applications span from traditional electronics to cutting-edge nanomaterials, making it indispensable for the continued advancement of technology.
Summary Table:
Aspect | Details |
---|---|
Definition | Vacuum deposition method for creating thin films and coatings. |
Key Materials | Silicon dioxide, graphene, carbon nanotubes, tungsten, high-k dielectrics. |
Process Types | Thermal CVD, PECVD, LPCVD, Laser-Assisted CVD, Photochemical CVD. |
Advantages | High-quality, uniform films; versatile; scalable; conformal coatings. |
Challenges | High temperatures, precursor selection, by-product management, cost. |
Applications | Transistors, protective coatings, nanomaterials, optoelectronics. |
Future Trends | Low-temperature processes, ALD integration, sustainable precursors. |
Discover how CVD can revolutionize your manufacturing process—contact our experts today!