Chemical vapor deposition (CVD) is a versatile and widely used technique for fabricating thin films, coatings, and advanced materials, including carbon nanotubes (CNTs). Specifically, the chemical vapor deposition of CNTs involves the use of thermal treatments, gas-phase reactions, and catalytic processes to grow CNTs with controlled structures. This method, known as catalytic chemical vapor deposition (CCVD), is the most common approach due to its cost-effectiveness and ability to produce high-quality CNTs. The process involves the decomposition of carbon-containing gases on a catalyst surface, leading to the formation of CNTs. CVD is not only used for CNTs but also for depositing various materials in industries such as semiconductors, cutting tools, and solar cells. However, the process requires careful control of parameters like temperature, gas flow, and catalyst selection to optimize CNT growth and minimize environmental impacts.
Key Points Explained:
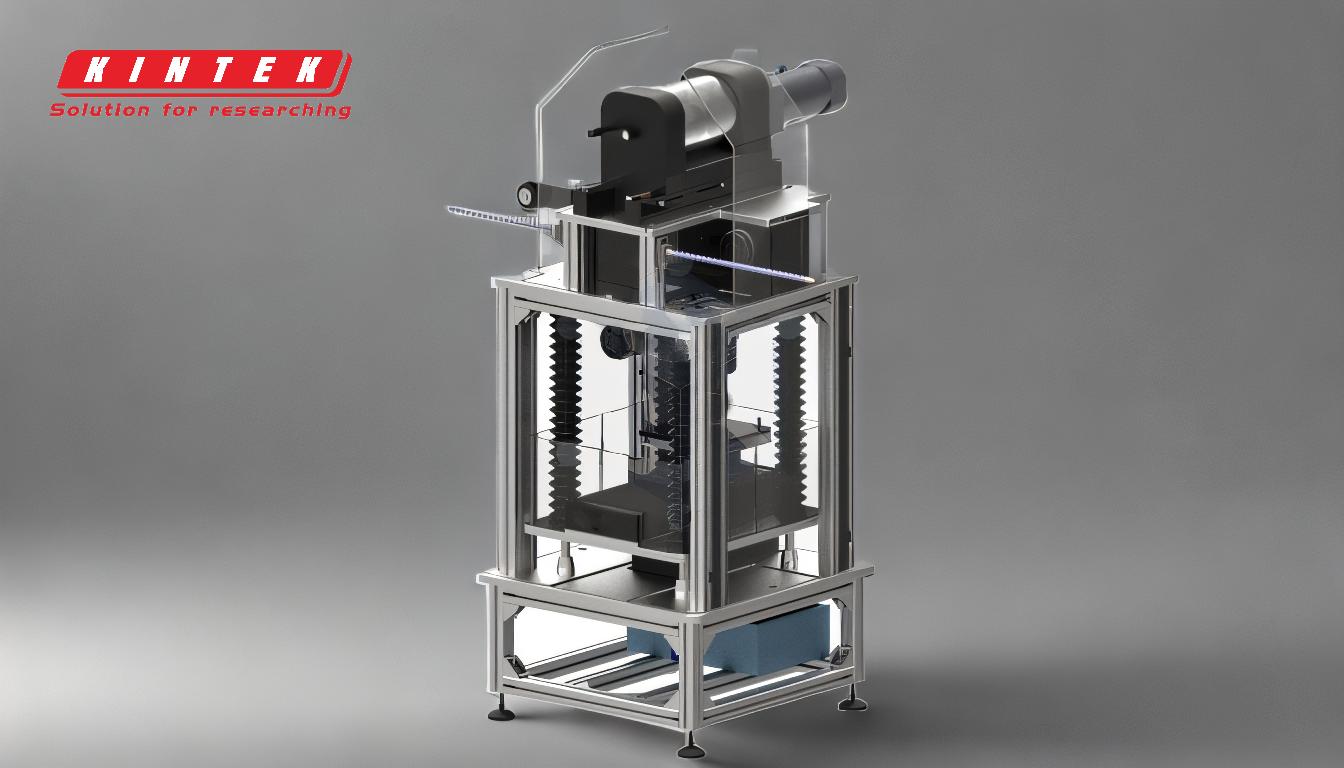
-
What is Chemical Vapor Deposition (CVD)?
- CVD is a vacuum deposition method used to produce high-quality solid materials, including thin films, coatings, and advanced nanostructures like carbon nanotubes (CNTs).
- It involves exposing a substrate to volatile precursors that react or decompose on the surface to form a solid deposit, while volatile by-products are removed by gas flow.
-
How is CVD Applied to CNT Fabrication?
- The fabrication of CNTs via CVD typically involves catalytic chemical vapor deposition (CCVD), where a carbon-containing gas (e.g., methane, ethylene, or acetylene) is decomposed on a catalyst surface (e.g., iron, nickel, or cobalt nanoparticles).
- The process requires thermal treatments and gas-phase rearrangement to achieve controlled growth of CNTs with specific structural properties.
-
Steps in the CVD Process for CNTs:
- Transport of Reacting Gases: Carbon-containing gases are introduced into the reaction chamber and transported to the substrate surface.
- Adsorption and Decomposition: The gases adsorb onto the catalyst surface and decompose into carbon atoms.
- Nucleation and Growth: Carbon atoms diffuse on the catalyst surface, forming nucleation sites and growing into CNTs.
- Desorption of By-products: Volatile by-products are removed from the reaction chamber.
-
Advantages of CVD for CNT Synthesis:
- Structural Controllability: CVD allows precise control over CNT diameter, length, and alignment by adjusting process parameters like temperature, gas flow rate, and catalyst type.
- Cost-Effectiveness: Compared to other methods like arc discharge or laser ablation, CVD is more scalable and economical for large-scale production.
- Versatility: CVD can produce a wide range of CNT types, including single-walled, multi-walled, and aligned CNTs.
-
Environmental Considerations:
- The synthesis process is a major contributor to the life cycle ecotoxicity of CNTs, primarily due to material and energy consumption and greenhouse gas emissions.
- Efforts to reduce environmental impact include optimizing process conditions, using renewable energy sources, and recycling catalysts.
-
Applications of CVD-Grown CNTs:
- Electronics: CNTs are used in transistors, interconnects, and sensors due to their excellent electrical properties.
- Energy Storage: CNTs enhance the performance of batteries and supercapacitors.
- Composites: CNTs are incorporated into polymers, metals, and ceramics to improve mechanical, thermal, and electrical properties.
- Environmental Applications: CNTs are used in filtration, catalysis, and water purification.
-
Challenges in CVD for CNT Synthesis:
- Catalyst Deactivation: Over time, catalysts can become deactivated, reducing the efficiency of CNT growth.
- Uniformity and Purity: Achieving uniform CNT growth and high purity remains a challenge, especially for large-scale production.
- Environmental Impact: The process requires significant energy and generates greenhouse gases, necessitating sustainable practices.
-
Future Directions:
- Research is focused on developing greener CVD processes, improving catalyst efficiency, and exploring new precursor gases.
- Advances in CVD technology are expected to enable the production of CNTs with tailored properties for emerging applications in nanotechnology and materials science.
By understanding the principles and applications of CVD for CNT synthesis, researchers and manufacturers can optimize the process to meet specific requirements while minimizing environmental impact.
Summary Table:
Key Aspect | Details |
---|---|
Process | Catalytic chemical vapor deposition (CCVD) using carbon-containing gases. |
Steps | 1. Transport of gases 2. Adsorption & decomposition 3. Nucleation & growth. |
Advantages | Structural controllability, cost-effectiveness, and versatility. |
Applications | Electronics, energy storage, composites, and environmental uses. |
Challenges | Catalyst deactivation, uniformity, and environmental impact. |
Future Directions | Greener processes, improved catalysts, and tailored CNT properties. |
Discover how CVD can revolutionize your CNT production—contact our experts today for tailored solutions!