Coated carbide tools are cutting tools made from tungsten carbide, a hard and durable material, which are further enhanced with a thin layer of coating to improve their performance. The coating, typically made of materials like titanium nitride (TiN), titanium carbonitride (TiCN), or aluminum oxide (Al₂O₃), provides additional hardness, wear resistance, and thermal stability. These tools are widely used in machining applications, such as turning, milling, and drilling, where they offer extended tool life, higher cutting speeds, and better surface finishes. The combination of carbide's toughness and the coating's protective properties makes coated carbide tools a preferred choice in industries like automotive, aerospace, and manufacturing.
Key Points Explained:
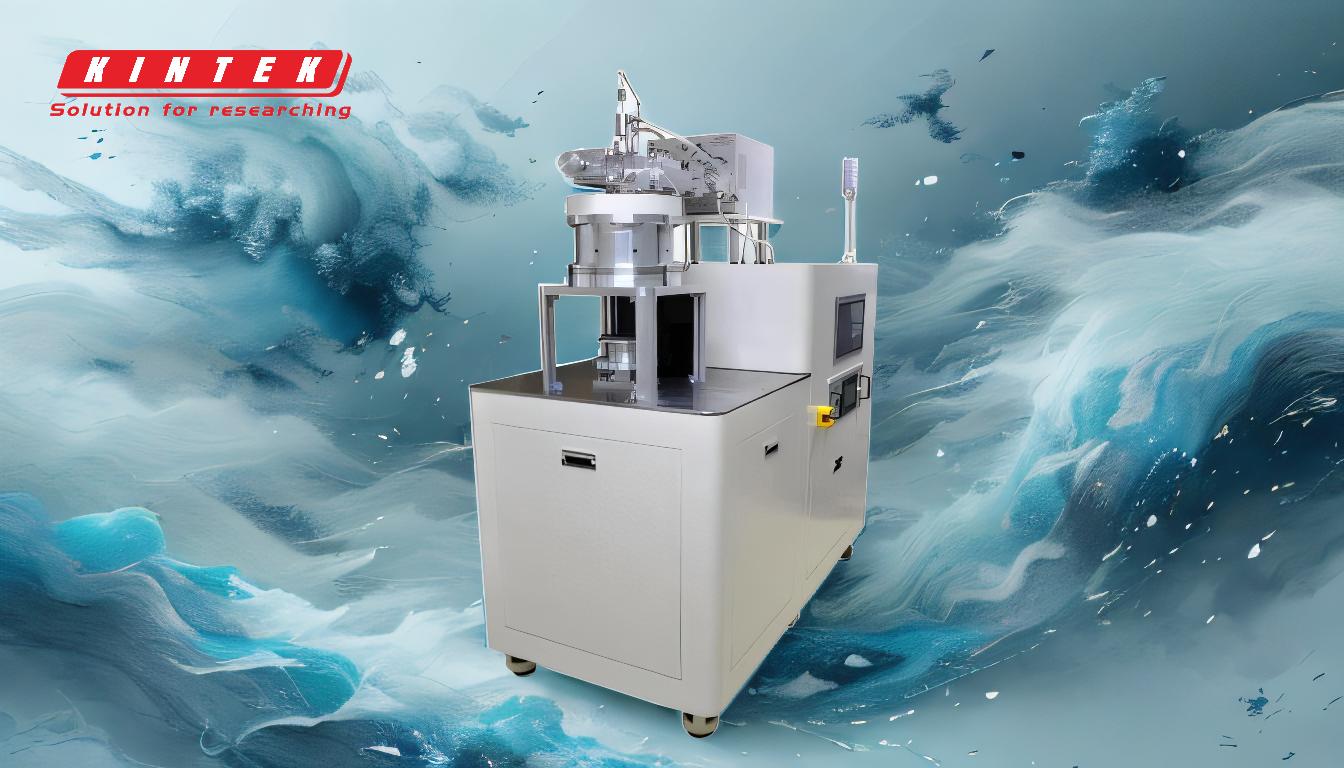
-
Composition of Coated Carbide Tools:
- Coated carbide tools are made from tungsten carbide, a composite material consisting of tungsten carbide particles bonded with a metallic binder, usually cobalt. This base material provides exceptional hardness and toughness, making it suitable for demanding machining operations.
- The coating is applied to the carbide substrate using advanced techniques like Physical Vapor Deposition (PVD) or Chemical Vapor Deposition (CVD). Common coating materials include:
- Titanium Nitride (TiN): Offers excellent wear resistance and a distinctive gold color.
- Titanium Carbonitride (TiCN): Provides higher hardness and better performance in high-speed applications.
- Aluminum Oxide (Al₂O₃): Enhances thermal stability and is ideal for high-temperature machining.
-
Advantages of Coated Carbide Tools:
- Extended Tool Life: The coating significantly reduces wear and tear, allowing the tool to last longer even under harsh conditions.
- Improved Performance: Coated tools can operate at higher cutting speeds and feed rates, increasing productivity.
- Better Surface Finish: The smooth surface of the coating reduces friction, resulting in superior surface quality on the machined part.
- Thermal Stability: Coatings like Al₂O₃ help dissipate heat, preventing thermal damage to the tool and workpiece.
-
Applications of Coated Carbide Tools:
- These tools are widely used in industries that require precision and durability, such as:
- Automotive: For machining engine components, gears, and transmission parts.
- Aerospace: For cutting high-strength materials like titanium and nickel alloys.
- General Manufacturing: For milling, turning, and drilling operations on a variety of materials, including steel, cast iron, and composites.
- These tools are widely used in industries that require precision and durability, such as:
-
Selection Criteria for Coated Carbide Tools:
- When choosing coated carbide tools, consider the following factors:
- Material to be Machined: Different coatings are optimized for specific materials. For example, TiCN is ideal for stainless steel, while Al₂O₃ is better for high-temperature alloys.
- Machining Conditions: High-speed operations may require coatings with better thermal stability.
- Tool Geometry: The shape and design of the tool should match the machining operation, such as roughing or finishing.
- When choosing coated carbide tools, consider the following factors:
-
Maintenance and Care:
- Proper handling and storage of coated carbide tools are essential to maintain their performance. Avoid exposing them to moisture or corrosive environments.
- Regular inspection for wear and damage ensures optimal performance and prevents premature failure.
By combining the inherent strength of tungsten carbide with the advanced properties of modern coatings, coated carbide tools provide a reliable and efficient solution for a wide range of machining challenges.
Summary Table:
Aspect | Details |
---|---|
Composition | Tungsten carbide base with coatings like TiN, TiCN, or Al₂O₃. |
Advantages | Extended tool life, higher cutting speeds, better surface finish, thermal stability. |
Applications | Automotive, aerospace, and general manufacturing. |
Selection Criteria | Material, machining conditions, and tool geometry. |
Maintenance | Proper storage, regular inspection, and avoiding corrosive environments. |
Discover how coated carbide tools can optimize your machining process—contact us today for expert advice!