Controlled atmosphere brazing (CAB) is a specialized brazing process that takes place in a controlled atmosphere furnace, where the environment is carefully regulated to prevent oxidation and ensure high-quality joints. This process is widely used in industries requiring strong, reliable, and oxidation-free bonds, such as automotive, aerospace, and electronics. CAB eliminates the need for fluxes in many cases, reduces energy consumption, and offers precise control over temperature and atmosphere, making it suitable for high-volume production and complex parts. However, it requires specialized knowledge and equipment to manage the process effectively.
Key Points Explained:
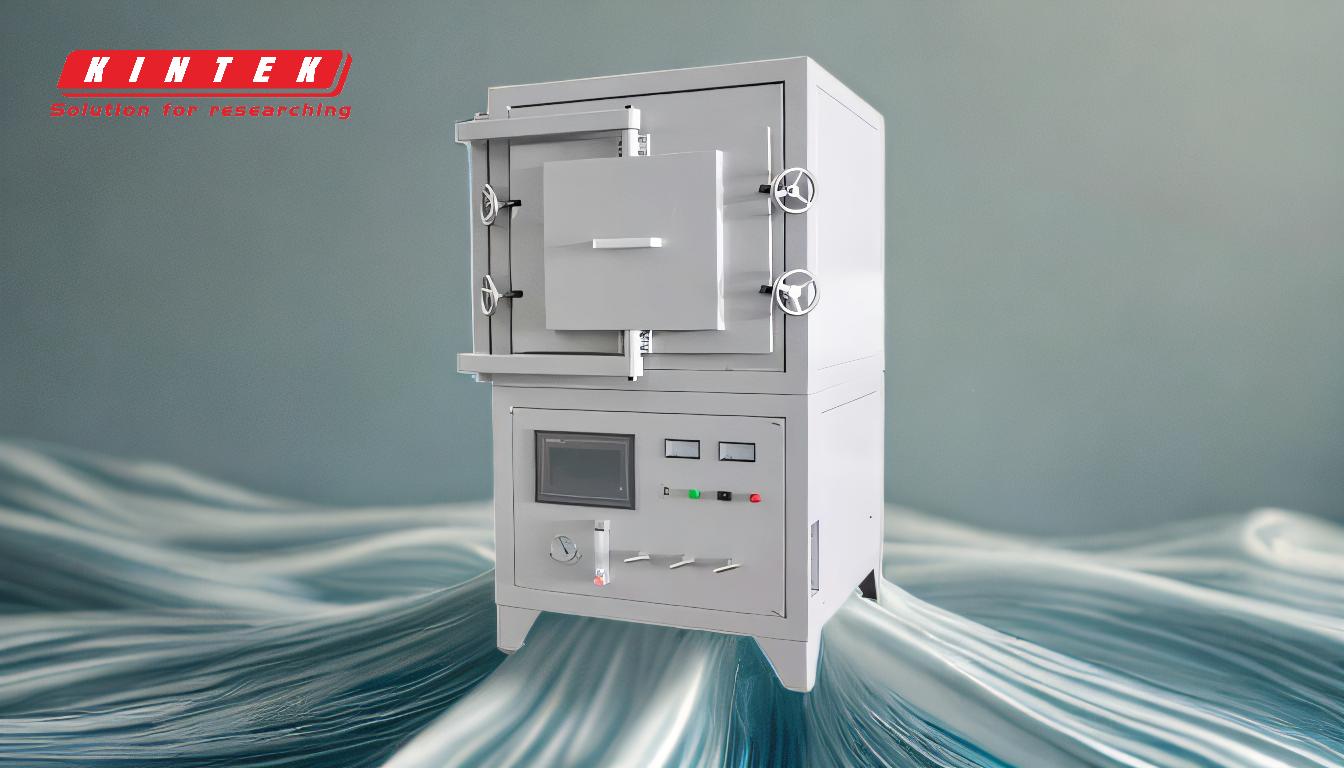
-
Definition and Purpose of Controlled Atmosphere Brazing:
- Controlled atmosphere brazing is a process where brazing is performed in a controlled atmosphere furnace to prevent oxidation and ensure proper wetting and flow of the filler metal. This results in strong, reliable joints with minimal defects.
- The controlled environment is critical for removing or reducing surface oxides on base metals, which allows the filler metal to bond effectively. This process is particularly useful for materials like aluminum, which are prone to oxidation.
-
Role of Controlled Atmosphere Furnace:
- A controlled atmosphere furnace provides a tightly sealed environment where temperature, pressure, and gas composition can be precisely controlled. This ensures optimal conditions for brazing, such as thermal homogeneity and accurate temperature regulation.
- The furnace can create protective or reactive atmospheres, which are essential for achieving desired material properties during heating and cooling.
-
Advantages of Controlled Atmosphere Brazing:
- Energy Efficiency: The process is energy-saving and environmentally friendly, with low energy consumption and reduced operating costs.
- High Performance: It offers high efficiency, thermal homogeneity, and precise controls, ensuring consistent and reliable results.
- Versatility: Suitable for parts of all shapes and sizes, making it applicable across various industries.
- Reduced Flux Usage: The controlled atmosphere minimizes or eliminates the need for flux, reducing post-brazing cleaning and improving joint quality.
-
Types of Furnaces Used:
- Continuous Belt Furnace: Ideal for high-volume production, this furnace uses a continuously moving belt to transport parts through heating and cooling zones. The belt speed can be adjusted to optimize throughput and meet specific part requirements.
- Batch Furnace: This involves loading parts into a furnace, creating a vacuum, heating to brazing temperature, and then cooling before unloading. While effective, it is slower and less suitable for high-volume production compared to continuous furnaces.
-
Challenges and Considerations:
- Filler Material Selection: Choosing the correct filler material based on bonding strength, conductivity, and compatibility with base metals is critical.
- Process Parameters: Calculating the appropriate time-at-temperature and preventing oxidation during the process require specialized knowledge.
- Technical Expertise: Operating a controlled atmosphere furnace safely and effectively demands expertise in industrial gas mixing and furnace controls.
-
Applications and Industries:
- Controlled atmosphere brazing is widely used in industries requiring high-strength, oxidation-free joints, such as automotive (radiators, heat exchangers), aerospace (heat shields, fuel systems), and electronics (heat sinks, circuit boards).
- The process is particularly beneficial for aluminum brazing, where oxidation is a significant concern.
-
Environmental and Safety Benefits:
- The process is environmentally friendly due to reduced flux usage and energy-efficient operations.
- Safety devices and precise controls in the furnace ensure safe handling of industrial gases and prevent accidents.
In summary, controlled atmosphere brazing is a highly efficient and versatile process that leverages the capabilities of a controlled atmosphere furnace to produce high-quality, oxidation-free joints. While it requires specialized knowledge and equipment, its advantages in terms of energy savings, performance, and versatility make it a preferred choice for many industries.
Summary Table:
Key Aspect | Details |
---|---|
Definition | Brazing in a controlled atmosphere to prevent oxidation and ensure strong joints. |
Advantages | Energy-efficient, high performance, versatile, and reduces flux usage. |
Furnace Types | Continuous belt furnace (high-volume) and batch furnace (smaller batches). |
Applications | Automotive, aerospace, electronics, and aluminum brazing. |
Challenges | Requires specialized knowledge, filler material selection, and precise controls. |
Environmental Benefits | Reduced flux usage, energy-efficient, and safe handling of industrial gases. |
Discover how controlled atmosphere brazing can elevate your manufacturing process—contact our experts today!