A dental ceramic furnace is a specialized piece of equipment used in dental laboratories for processes such as firing, sintering, pressing, and glazing dental ceramics. These furnaces are designed with advanced features to ensure precision, efficiency, and safety. Key features often include high-temperature precision, digital programmability, compact design, and user-friendly interfaces. Dental ceramic furnaces are essential for creating high-quality dental restorations like crowns, bridges, and frameworks, ensuring they achieve the necessary hardness, density, and aesthetic properties. They are categorized into various types, such as dental press furnaces and dental sintering furnaces, each tailored for specific applications.
Key Points Explained:
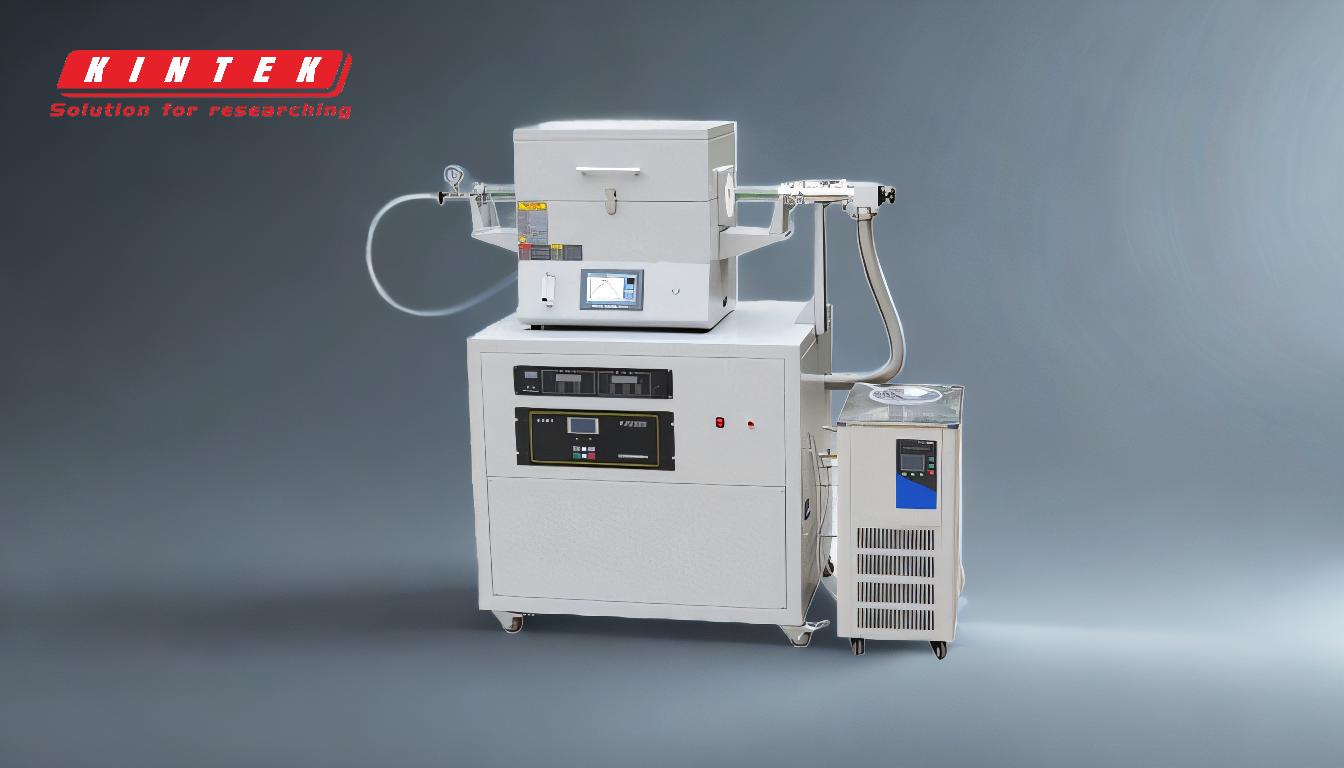
-
Purpose and Applications:
- Dental ceramic furnaces are used in dental laboratories for processes like firing, sintering, pressing, and glazing dental ceramics.
- They are essential for creating dental restorations such as crowns, bridges, and frameworks, ensuring they achieve the necessary hardness, density, and aesthetic properties.
-
Key Features:
- High-Temperature Precision: These furnaces offer precise temperature control, often with an error margin of within +/-1°C, ensuring consistent results.
- Digital Programmability: Many models come with digital programmable functions, allowing for customizable firing schedules and automated processes.
- Compact Design: Dental furnaces are often designed to be compact, making them suitable for small laboratory spaces.
- User-Friendly Interfaces: Features like true color touch screens and USB ports for computer connectivity make these furnaces easy to operate and program.
-
Types of Dental Ceramic Furnaces:
- Dental Press Furnaces: These are used for pressing dental ceramics, often featuring high-quality automatic temperature adjustment and precision stepper motor drives for smooth operation.
- Dental Sintering Furnaces: These furnaces are specifically designed to sinter zirconia restorations, reaching the high temperatures required to achieve final hardness and reduce porosity.
-
Advanced Technologies:
- Vacuum Technology: Some furnaces use vacuum technology to ensure color stability and improve the quality of the final product.
- Insulation and Heating: Advanced insulation materials and heating elements, such as spiral quartz chambers and special alloy heating wires, ensure efficient heating and temperature uniformity.
- Safety Features: Multiple safety measures, including thermocouple failure protection, door opening electrical outage, and over-temperature protection, ensure safe operation.
-
Operational Efficiency:
- Heating and Cooling: Features like double-shell hollow thermal insulation and double ventilation ducts allow for quick internal cooling and efficient ventilation.
- Programmability: Built-in programs and multi-stage programmable control simplify the experiment process, enabling automatic control and operation.
-
Maintenance and Repair:
- Ease of Maintenance: Split designs with detachable circuits make these furnaces easy to repair and maintain.
- Durability: High-quality materials and construction ensure long-lasting performance and reliability.
In summary, a dental ceramic furnace is a critical tool in modern dental laboratories, offering advanced features and technologies to ensure the production of high-quality dental restorations. Its precision, programmability, and safety features make it an indispensable piece of equipment for dental professionals.
Summary Table:
Aspect | Details |
---|---|
Purpose | Firing, sintering, pressing, and glazing dental ceramics. |
Key Features | High-temperature precision, digital programmability, compact design, user-friendly interfaces. |
Types | Dental press furnaces, dental sintering furnaces. |
Advanced Technologies | Vacuum technology, advanced insulation, safety features. |
Operational Efficiency | Quick cooling, programmable controls, automatic operation. |
Maintenance | Easy to repair, durable, long-lasting performance. |
Upgrade your dental lab with a precision dental ceramic furnace—contact us today for expert advice and solutions!