Vapor deposition is a process used to create thin films or coatings on a substrate by depositing vaporized material onto its surface. This technique is widely used in industries such as semiconductors, optics, and coatings. The process involves converting a material into a vapor phase, which then condenses onto the substrate to form a thin, uniform layer. Two common methods of vapor deposition are Chemical Vapor Deposition (CVD) and sputtering deposition. In CVD, a substrate is exposed to a gas that reacts or decomposes to form a solid film, while sputtering uses high-energy ions to dislodge atoms from a target material, which then deposit onto the substrate.
Key Points Explained:
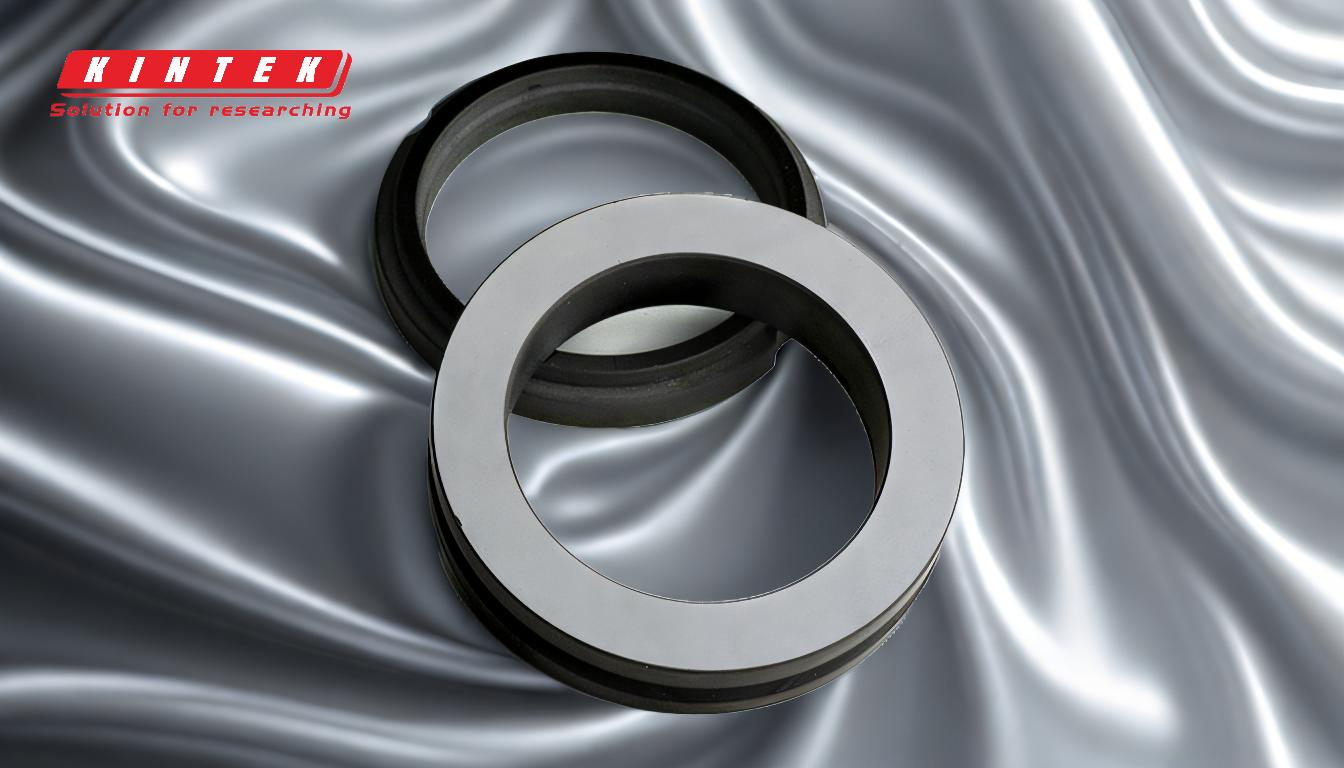
-
Definition of Vapor Deposition:
- Vapor deposition is a process where a material is vaporized and then deposited onto a substrate to form a thin film or coating. This method is essential for creating high-quality, uniform layers used in various applications, including electronics, optics, and protective coatings.
-
Chemical Vapor Deposition (CVD):
- In CVD, the substrate is placed in a chamber filled with organometallic or reactive gases. These gases either react with the substrate surface or decompose, leading to the formation of a solid film. This process is widely used for depositing materials like metals, semiconductors, and plastics. CVD is favored for its ability to produce high-purity, uniform films with excellent adhesion to the substrate.
-
Sputtering Deposition:
- Sputtering involves bombarding a target material with high-energy ions, typically of argon gas. The impact dislodges atoms from the target, which then travel and deposit onto the substrate. This method is versatile and can be used to deposit a wide range of materials, including metals, alloys, and ceramics. Sputtering is known for its ability to produce dense, high-quality films with good step coverage.
-
Applications of Vapor Deposition:
- Vapor deposition techniques are critical in the fabrication of semiconductor devices, where they are used to create thin films of conductive, insulating, and semiconducting materials.
- In the optics industry, vapor deposition is used to produce anti-reflective coatings, mirrors, and optical filters.
- The process is also employed in the production of wear-resistant and corrosion-resistant coatings for industrial tools and components.
-
Advantages of Vapor Deposition:
- Uniformity: Vapor deposition techniques can produce highly uniform films, even on complex geometries.
- Versatility: A wide range of materials, including metals, ceramics, and polymers, can be deposited using these methods.
- Precision: The process allows for precise control over film thickness and composition, making it ideal for high-tech applications.
-
Challenges and Considerations:
- Cost: Vapor deposition equipment and processes can be expensive, particularly for high-purity or large-scale applications.
- Complexity: The process often requires precise control of parameters such as temperature, pressure, and gas flow rates.
- Material Limitations: Some materials may not be suitable for vapor deposition due to their thermal or chemical properties.
By understanding the principles and techniques of vapor deposition, manufacturers and researchers can select the appropriate method for their specific application, ensuring high-quality and reliable thin film coatings.
Summary Table:
Aspect | Details |
---|---|
Definition | Process of depositing vaporized material onto a substrate to form thin films. |
Methods | Chemical Vapor Deposition (CVD), Sputtering Deposition. |
Applications | Semiconductors, optics, wear-resistant coatings, and more. |
Advantages | Uniformity, versatility, and precision in film creation. |
Challenges | High cost, process complexity, and material limitations. |
Discover how vapor deposition can elevate your projects—contact our experts today!