Diamond coating film is a thin layer of synthetic diamond material applied to various substrates to enhance their performance. It combines the exceptional properties of diamond, such as high hardness, excellent thermal conductivity, chemical inertness, and wear resistance, with the ability to customize its characteristics (e.g., grain size, surface roughness, and crystallinity) through controlled deposition processes. These films are widely used in industrial applications, including tool coatings, electronics, optics, and mechanical components, as well as in academic research. Their unique properties and tunability make them ideal for improving efficiency, precision, and durability in modern machinery and advanced technologies.
Key Points Explained:
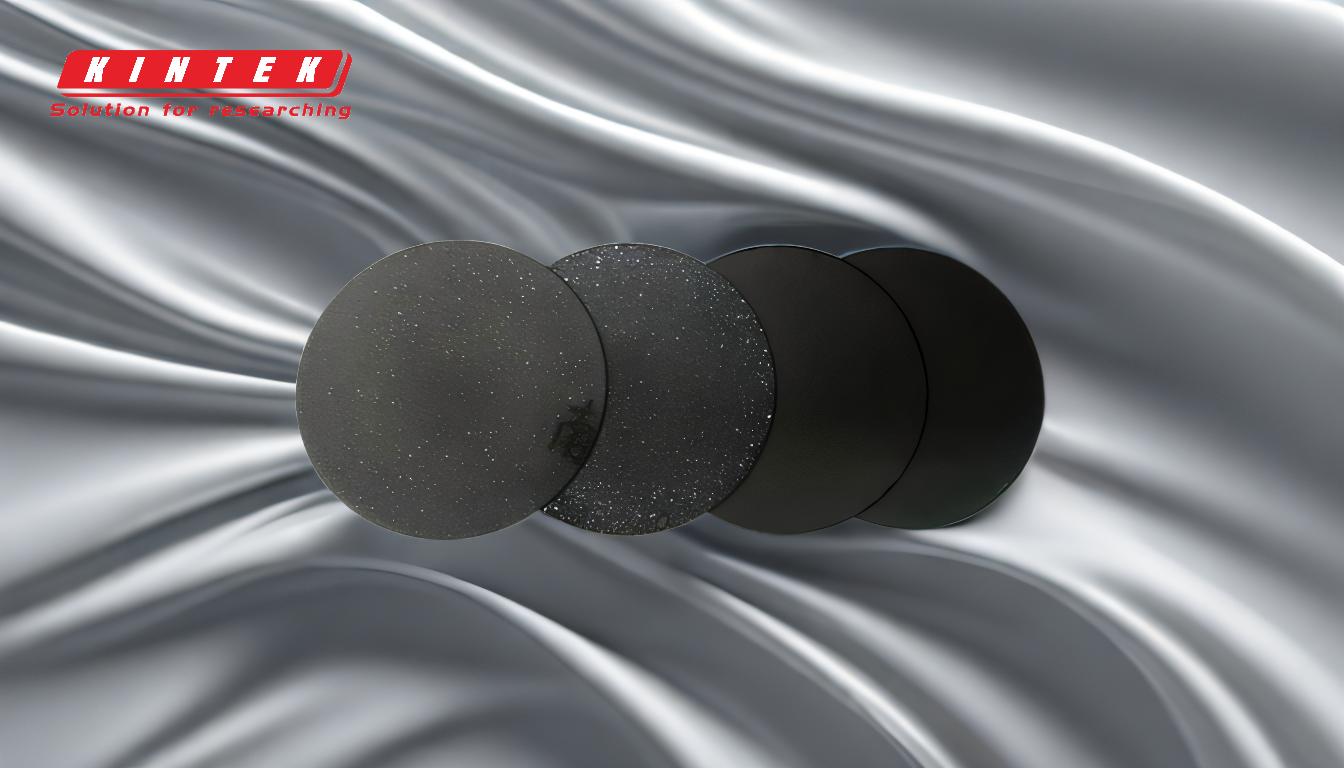
-
Definition and Composition:
- Diamond coating film is a synthetic diamond layer deposited onto substrates to enhance their properties.
- It mimics the structure and characteristics of natural diamond, including its crystalline form and exceptional material properties.
-
Key Properties:
- High Hardness: Diamond is the hardest known material, making the coating highly resistant to wear and abrasion.
- Excellent Thermal Conductivity: It efficiently dissipates heat, which is crucial for applications in electronics and high-temperature environments.
- Chemical Inertness: Diamond coatings are resistant to chemical reactions, making them suitable for corrosive environments.
- Wear Resistance: The coating significantly extends the lifespan of tools and mechanical components.
- Electrical Insulation: Diamond films provide excellent electrical insulation, which is valuable in electronic applications.
- Optical and Acoustic Properties: These films exhibit transparency and acoustic properties, making them useful in optics and acoustic devices.
-
Customizability:
- The properties of diamond coating films can be tailored by controlling deposition parameters (e.g., temperature, pressure) and gas phase composition during synthesis.
- Characteristics such as grain size, surface roughness, and crystallinity can be adjusted to meet specific application requirements.
-
Applications:
- Industrial Tools: Diamond coatings are used to enhance the performance and lifespan of cutting tools, drills, and wear-resistant components.
- Electronics: The thermal and electrical properties of diamond films make them ideal for heat sinks, semiconductor devices, and sensors.
- Optics: Their transparency and durability are utilized in optical windows, lenses, and protective coatings.
- Acoustic Devices: Diamond films are used in high-frequency acoustic devices due to their excellent acoustic properties.
- Research: In academia, diamond films are studied for their fundamental properties and potential applications in advanced technologies.
-
Advantages of Nanometer Diamond Films:
- Nanometer diamond films combine the properties of nanomaterials (e.g., high surface area, unique mechanical properties) with those of diamond.
- They are particularly effective as tool coatings, improving machining efficiency, precision, and tool longevity in modern machinery industries.
-
Synthesis Methods:
- Diamond coating films are typically synthesized using chemical vapor deposition (CVD) techniques, which allow precise control over film properties.
- Other methods include physical vapor deposition (PVD) and plasma-enhanced CVD, depending on the desired characteristics and application.
-
Future Potential:
- The ability to tune the microstructure, morphology, and impurity levels of diamond films opens up possibilities for new applications in emerging fields such as quantum computing, biomedical devices, and advanced sensors.
- Ongoing research aims to further optimize the synthesis process and expand the range of substrates compatible with diamond coatings.
In summary, diamond coating film is a versatile and high-performance material that leverages the exceptional properties of diamond. Its applications span industries and research fields, driven by its hardness, thermal conductivity, chemical resistance, and customizability. As technology advances, the potential for diamond coatings continues to grow, offering solutions to challenges in precision engineering, electronics, and beyond.
Summary Table:
Key Aspect | Details |
---|---|
Definition | Synthetic diamond layer applied to substrates to enhance performance. |
Key Properties | High hardness, thermal conductivity, chemical inertness, wear resistance. |
Applications | Industrial tools, electronics, optics, acoustic devices, research. |
Customizability | Adjust grain size, surface roughness, and crystallinity for specific needs. |
Synthesis Methods | CVD, PVD, plasma-enhanced CVD. |
Future Potential | Quantum computing, biomedical devices, advanced sensors. |
Unlock the potential of diamond coating films for your applications—contact us today!