The primary difference between RF (Radio Frequency) sputtering and DC (Direct Current) sputtering lies in the type of power source used and their respective applications. DC sputtering uses a Direct Current power source and is ideal for conductive materials, offering high deposition rates and cost-efficiency for large substrates. RF sputtering, on the other hand, employs an Alternating Current power source, typically at 13.56 MHz, and is suitable for both conductive and non-conductive materials, especially dielectric targets. RF sputtering has a lower deposition rate and is more expensive, making it better suited for smaller substrates. Additionally, RF sputtering prevents charge buildup on insulating materials, a limitation of DC sputtering.
Key Points Explained:
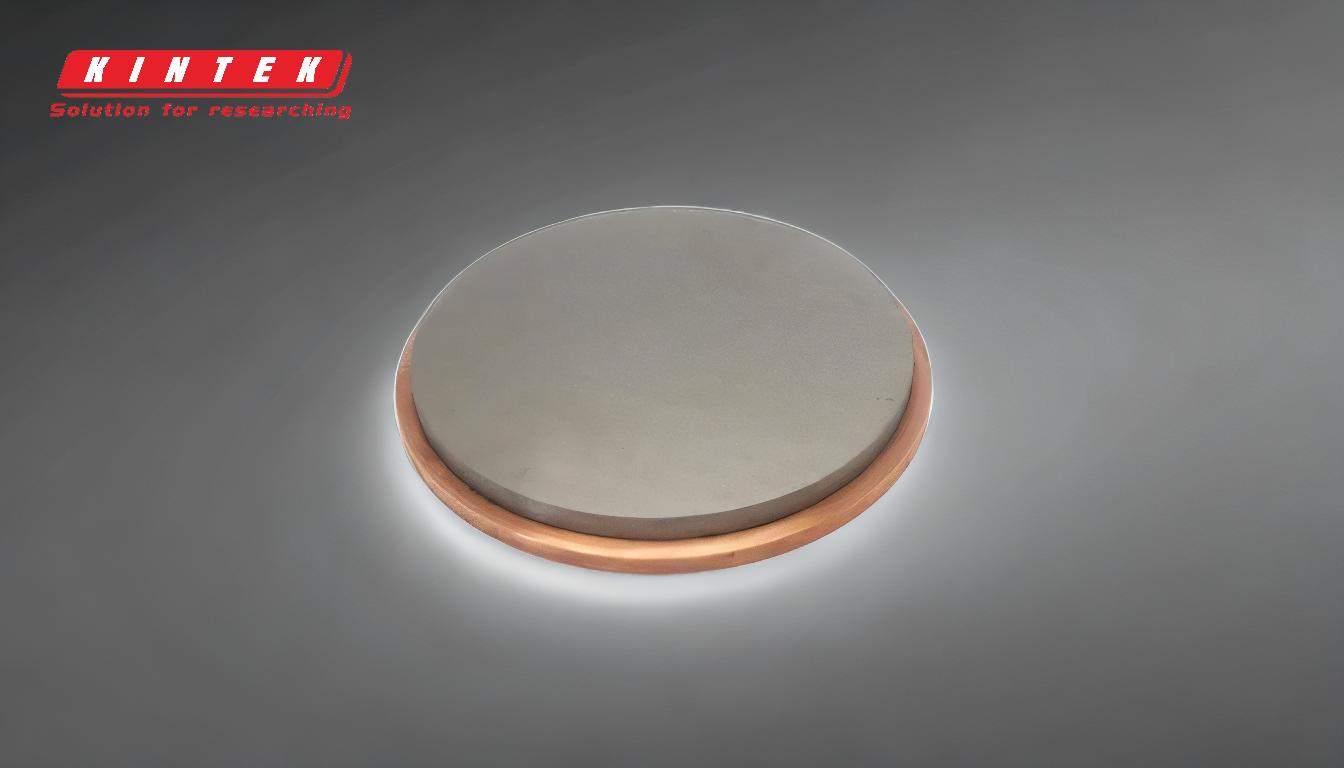
-
Power Source and Mechanism:
- DC Sputtering: Uses a Direct Current (DC) power source. Positively charged gas ions are accelerated toward the target material, causing atoms to be ejected and deposited onto the substrate.
- RF Sputtering: Uses an Alternating Current (AC) power source, typically at 13.56 MHz. The alternating current prevents charge buildup on the target, making it effective for both conductive and non-conductive materials.
-
Material Compatibility:
- DC Sputtering: Best suited for conductive materials like pure metals. It struggles with insulating materials due to charge accumulation.
- RF Sputtering: Can handle both conductive and non-conductive (dielectric) materials. The alternating current prevents charge buildup, allowing continuous sputtering of insulating materials.
-
Deposition Rate and Cost:
- DC Sputtering: Offers high deposition rates and is more cost-efficient, making it suitable for large substrates and high-volume production.
- RF Sputtering: Has a lower deposition rate and is more expensive, making it more suitable for smaller substrates and specialized applications.
-
Voltage Requirements:
- DC Sputtering: Operates at voltages between 2,000-5,000 volts.
- RF Sputtering: Requires higher voltage (1,012 volts or higher) and can maintain gas plasma at lower chamber pressure, reducing collisions and preventing charge buildup.
-
Applications:
- DC Sputtering: Widely used for applying metal coatings on large substrates. It is effective and economical for processing large quantities.
- RF Sputtering: Used for both conductive and non-conductive materials, especially in applications requiring precise control and smaller substrate sizes.
-
Process Dynamics:
- DC Sputtering: Involves a straightforward process where positively charged ions are accelerated to the target, causing sputtering.
- RF Sputtering: Involves a two-cycle process of polarization and reverse polarization, which helps in preventing charge buildup and allows for continuous sputtering of insulating materials.
In summary, the choice between RF and DC sputtering depends on the material properties and the specific requirements of the application. DC sputtering is preferred for its high deposition rates and cost-efficiency with conductive materials, while RF sputtering is essential for handling dielectric materials and applications requiring precise control.
Summary Table:
Aspect | DC Sputtering | RF Sputtering |
---|---|---|
Power Source | Direct Current (DC) | Alternating Current (AC) at 13.56 MHz |
Material Compatibility | Best for conductive materials (e.g., metals) | Suitable for both conductive and non-conductive (dielectric) materials |
Deposition Rate | High deposition rate | Lower deposition rate |
Cost | Cost-efficient for large substrates | More expensive, suited for smaller substrates |
Voltage Requirements | 2,000-5,000 volts | 1,012 volts or higher |
Applications | Metal coatings on large substrates | Precise control for smaller substrates and dielectric materials |
Process Dynamics | Positively charged ions accelerate to the target | Two-cycle process prevents charge buildup on insulating materials |
Need help choosing the right sputtering method for your project? Contact our experts today!