Sinter and pellet are both agglomerated forms of iron ore used in the iron and steel industry, but they differ significantly in their production processes, physical properties, and applications. Sinter is produced by sintering, a process that involves heating fine iron ore particles with fluxes and other materials to form a porous mass. Pellets, on the other hand, are made by rolling fine iron ore with binders and then hardening them through firing. Sinter is typically used in blast furnaces, while pellets are used in both blast furnaces and direct reduction processes. The choice between sinter and pellet depends on factors like cost, availability, and specific industrial requirements.
Key Points Explained:
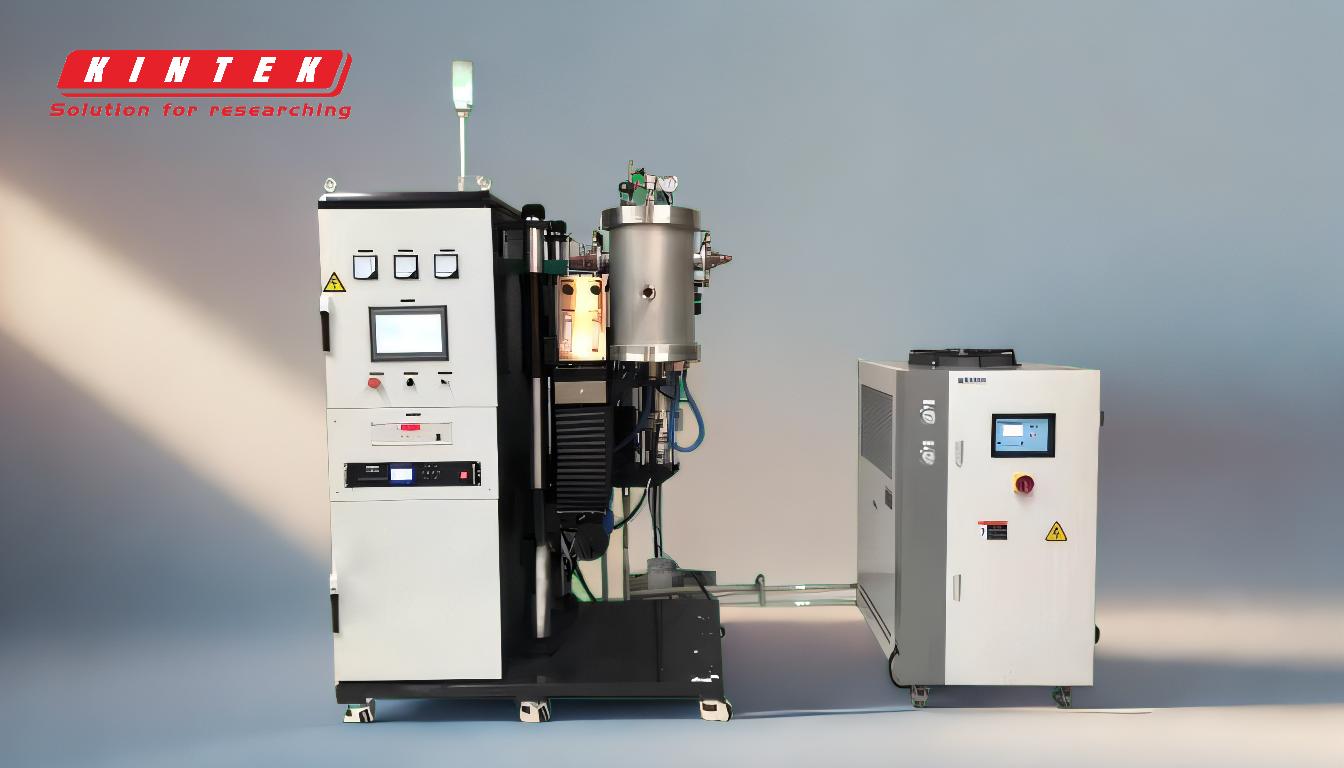
-
Production Process:
- Sinter: Sinter is produced through a sintering process, where fine iron ore particles are mixed with fluxes (like limestone and dolomite) and other materials, then heated to a temperature below the melting point of iron. This causes the particles to fuse together, forming a porous mass.
- Pellet: Pellets are produced by rolling fine iron ore with binders (like bentonite) and then hardening them through a firing process in a pelletizing plant. The firing process typically occurs in a rotary kiln or a grate-kiln system.
-
Physical Properties:
- Sinter: Sinter is characterized by its porous structure, which allows for better gas flow in the blast furnace. It has a lower strength compared to pellets but is more cost-effective to produce.
- Pellet: Pellets are more uniform in size and shape, with higher mechanical strength and density. This makes them more suitable for long-distance transportation and for use in direct reduction processes.
-
Applications:
- Sinter: Sinter is primarily used in blast furnaces, where its porous structure aids in the efficient reduction of iron ore. It is often preferred in integrated steel plants due to its lower production cost.
- Pellet: Pellets are used in both blast furnaces and direct reduction processes. Their high strength and uniformity make them ideal for use in modern steelmaking processes, especially in regions where high-quality iron ore is not readily available.
-
Cost and Availability:
- Sinter: The production of sinter is generally less expensive than that of pellets, as it requires less energy and fewer raw materials. However, the availability of suitable iron ore fines for sintering can be a limiting factor.
- Pellet: Pellets are more expensive to produce due to the additional energy required for firing and the need for binders. However, they offer greater flexibility in terms of raw material sourcing, as they can be made from a wider range of iron ores.
-
Environmental Impact:
- Sinter: The sintering process can produce significant emissions, including dust, sulfur dioxide, and nitrogen oxides. Efforts are being made to reduce these emissions through improved sintering technologies and the use of cleaner fuels.
- Pellet: The pelletizing process is generally considered to be more environmentally friendly than sintering, as it produces fewer emissions and can utilize waste materials as binders. However, the energy-intensive nature of the firing process remains a concern.
In summary, while both sinter and pellet serve as essential raw materials in the iron and steel industry, they differ in their production processes, physical properties, and applications. The choice between sinter and pellet depends on various factors, including cost, availability, and specific industrial requirements. Understanding these differences is crucial for making informed decisions in the procurement and use of these materials.
Summary Table:
Aspect | Sinter | Pellet |
---|---|---|
Production Process | Heating fine iron ore with fluxes to form a porous mass. | Rolling fine iron ore with binders, then hardening through firing. |
Physical Properties | Porous structure, lower strength, cost-effective. | Uniform size, higher strength, suitable for transportation. |
Applications | Primarily used in blast furnaces. | Used in blast furnaces and direct reduction processes. |
Cost and Availability | Less expensive, limited by iron ore fines availability. | More expensive, flexible raw material sourcing. |
Environmental Impact | Higher emissions, but improving with cleaner technologies. | Fewer emissions, but energy-intensive firing process. |
Need help choosing between sinter and pellet for your operations? Contact our experts today for tailored advice!