Chemical Vapor Deposition (CVD) is a sophisticated process used to deposit thin films of materials onto a substrate through chemical reactions in the vapor phase. This method involves several steps, including the transport of gaseous reactants to the substrate surface, adsorption, surface reactions, diffusion, nucleation, and desorption of by-products. CVD is highly versatile, offering precise control over film thickness and composition, making it ideal for applications like electrical circuits. It is relatively affordable, provides uniform coatings, and produces high-purity materials. The process can be traced back to ancient times, with modern advancements enabling various specialized techniques such as aerosol-assisted and plasma-based CVD.
Key Points Explained:
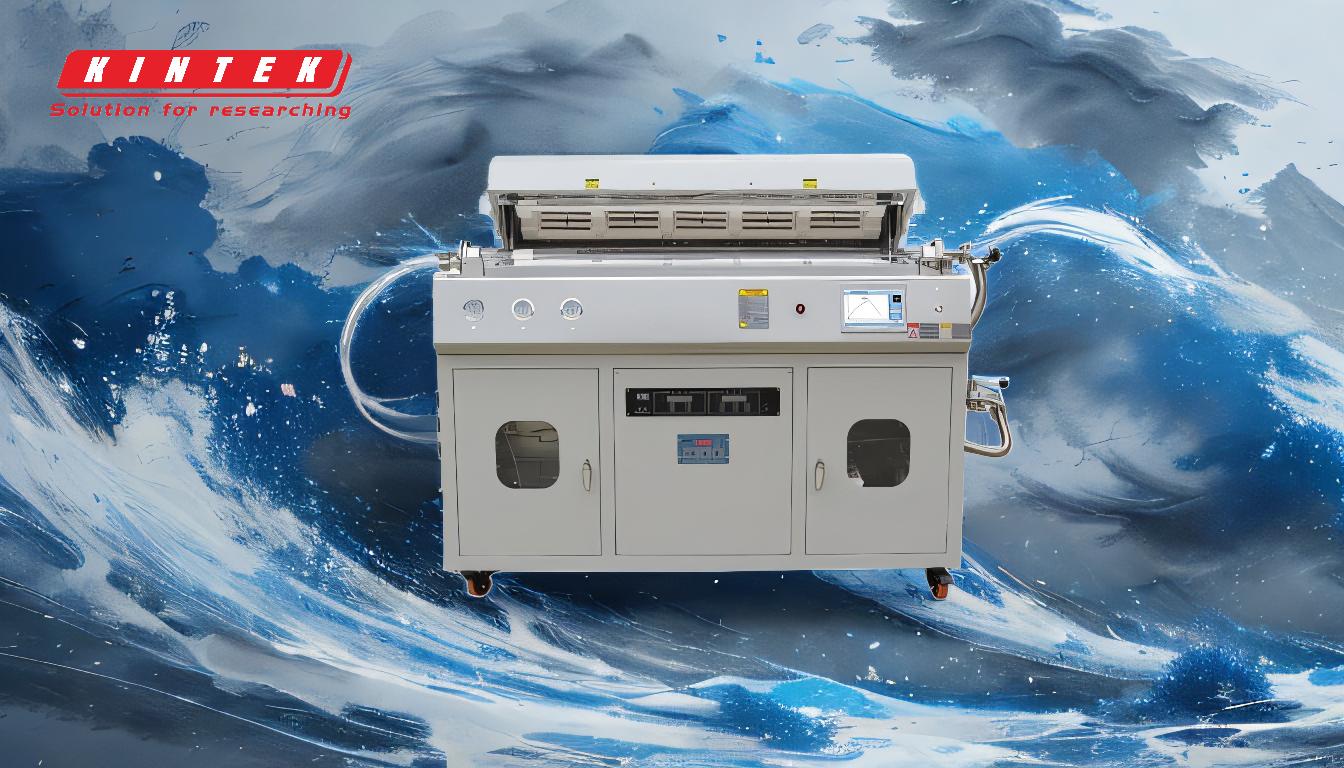
-
Definition and Basic Mechanism:
- Chemical Vapor Deposition (CVD) is a thin-film deposition process where a solid film is formed on a heated substrate due to chemical reactions in the vapor phase.
- The process involves the transport of gaseous reactants to the substrate, adsorption, surface reactions, diffusion to growth sites, nucleation, and desorption of by-products.
-
Types of CVD:
- Aerosol-Assisted CVD: Uses aerosol to deliver the precursor to the substrate.
- Direct Liquid Injection CVD: Involves injecting a liquid precursor into a heated chamber.
- Plasma-Based CVD: Utilizes plasma instead of heat to drive the chemical reactions, allowing for lower temperature processing.
-
Advantages of CVD:
- Versatility: Relies on chemical reactions, allowing for a wide range of materials to be deposited.
- Control: Offers full control over the timing and conditions of the deposition process.
- Precision: Capable of creating ultra-thin layers, essential for applications like electrical circuits.
- Uniformity: Provides uniform coatings over complex geometries.
- Purity: Produces high-purity materials with excellent adhesion properties.
-
Historical Context:
- The concept of CVD can be traced back to ancient times, with the deposition of soot on cave walls from burning lamps being a rudimentary form of the process.
- Modern CVD technology has evolved significantly, enabling precise and controlled deposition of a wide variety of materials.
-
Applications:
- Electrical Circuits: CVD is used to deposit ultra-thin layers of conductive and insulating materials necessary for the fabrication of microelectronic devices.
- Protective Coatings: Provides uniform and durable coatings for tools and components.
- Optical Films: Used in the production of anti-reflective and reflective coatings for lenses and mirrors.
-
Process Steps in Detail:
- Transport of Reactants: Gaseous species are transported to the substrate surface.
- Adsorption: Reactants adhere to the substrate surface.
- Surface Reactions: Chemical reactions occur on the heated surface, leading to film growth.
- Diffusion: Species diffuse across the surface to growth sites.
- Nucleation and Growth: Film formation begins with nucleation, followed by growth.
- Desorption and Removal: By-products are desorbed and transported away from the surface.
-
Economic and Practical Considerations:
- Cost-Effectiveness: CVD is relatively affordable compared to other thin-film deposition techniques.
- Scalability: Suitable for large-scale production due to its high deposition rate and uniformity.
- Non-Line of Sight Process: Can coat complex geometries and hidden surfaces effectively.
By understanding these key points, one can appreciate the complexity and utility of Chemical Vapor Deposition in modern manufacturing and technology.
Summary Table:
Aspect | Details |
---|---|
Definition | A process to deposit thin films via chemical reactions in the vapor phase. |
Key Steps | Transport, adsorption, surface reactions, diffusion, nucleation, desorption. |
Types of CVD | Aerosol-assisted, direct liquid injection, plasma-based. |
Advantages | Versatility, precision, uniformity, high-purity materials. |
Applications | Electrical circuits, protective coatings, optical films. |
Economic Benefits | Affordable, scalable, effective for complex geometries. |
Interested in how electrical chemical vapor deposition can benefit your projects? Contact us today to learn more!