Electron coating, also known as electron beam (EB) coating or e-beam coating, is a specialized process that involves the use of an electron beam to deposit or cure materials onto a substrate. This technology is widely used in various industries due to its ability to produce fine, durable, and high-performance coatings. Electron coating can be categorized into two main types: electron beam evaporation for physical vapor deposition (PVD) and electron beam curing for liquid coatings. The process is highly directional, allowing for precise application, and is capable of producing coatings with superior properties such as abrasion resistance, chemical resistance, and optical clarity. Applications range from decorative and functional coatings on materials like glass, metal, and plastics to specialized uses in aerospace, automotive, and medical industries.
Key Points Explained:
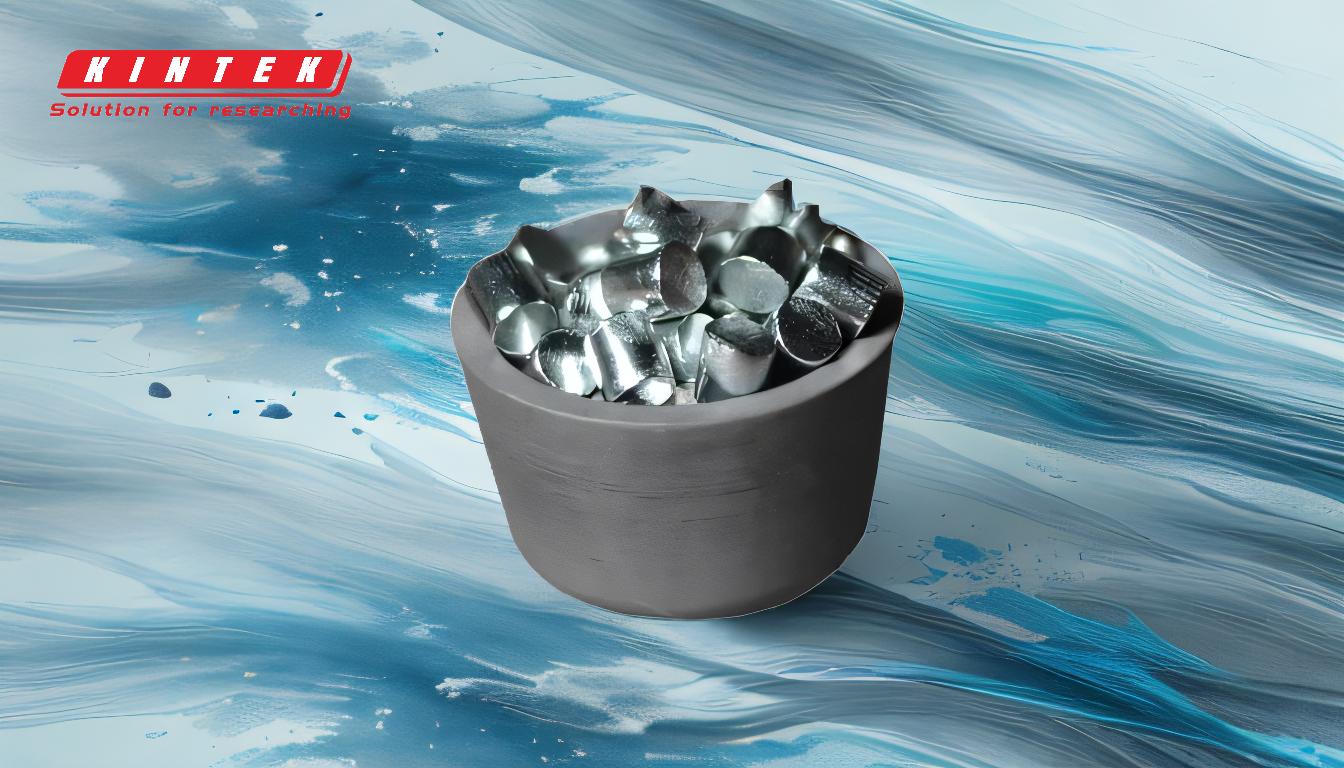
-
Definition and Types of Electron Coating:
- Electron coating refers to processes that utilize an electron beam to either evaporate materials for deposition (e.g., electron beam evaporation) or cure liquid coatings into solid films (e.g., EB curable coatings).
- Electron beam evaporation is a physical vapor deposition (PVD) technique used to create thin, fine layers of materials like metals and dielectrics.
- EB curable coatings are liquid formulations that are transformed into solid, durable films through exposure to an electron beam.
-
How Electron Beam Coating Works:
- In electron beam evaporation, a high-energy electron beam is directed at a target material, causing it to evaporate and deposit onto a substrate. This process is highly directional and allows for precise control over coating thickness and uniformity.
- For EB curable coatings, the electron beam interacts with photoinitiators in the liquid coating, initiating a polymerization reaction that solidifies the coating. This method is energy-efficient and environmentally friendly, as it does not rely on solvents.
-
Advantages of Electron Coating:
- Precision and Control: The directional nature of the electron beam ensures accurate application, making it ideal for applications requiring fine layers or specific patterns.
- Durability: Electron coatings are known for their superior abrasion, scratch, and chemical resistance, making them suitable for demanding environments.
- Versatility: A wide range of materials, including metals, dielectrics, and custom-formulated coatings, can be used with electron coating processes.
- Eco-Friendly: EB curable coatings are solvent-free, reducing volatile organic compound (VOC) emissions and aligning with sustainability goals.
-
Applications of Electron Coating:
- Industrial and Manufacturing: Used for metallization, dielectric coatings, and optical coatings in aerospace, automotive, and industrial components.
- Decorative and Functional Coatings: Applied to glass, metal, and plastics for durability, energy efficiency (e.g., low-emissivity glass), and aesthetic purposes.
- Specialized Uses: Includes antimicrobial coatings, low-friction coatings for treadmill decking, and coatings for signage, flooring, and store fixtures.
- Medical and Optical: Used for ophthalmic coatings and equipment in sensitive environments like dairy sheds.
-
Material Choices and Customization:
- Electron beam evaporation supports a variety of materials, including metals (e.g., aluminum, gold) and dielectrics (e.g., oxides, nitrides), enabling applications like conductive layers, insulation, and optical coatings.
- EB curable coatings are highly engineered and can be custom-formulated to meet specific performance requirements, such as anti-skid properties, electrostatic discharge (ESD) protection, or special visual effects.
-
Comparison with Other Coating Technologies:
- Electron coating offers advantages over traditional methods like spray coating or thermal evaporation, including better adhesion, finer layer control, and reduced environmental impact.
- However, it may have limitations in terms of coated area size and equipment cost, making it more suitable for specialized or high-value applications.
-
Future Trends and Innovations:
- Advances in electron beam technology are expanding its use in emerging fields such as flexible electronics, nanotechnology, and renewable energy.
- Research is ongoing to develop new formulations for EB curable coatings, focusing on enhanced performance, reduced curing times, and broader material compatibility.
In summary, electron coating is a versatile and advanced technology that plays a critical role in modern manufacturing and industrial applications. Its ability to produce high-performance, durable, and precisely applied coatings makes it a preferred choice for industries requiring superior material properties and innovative solutions.
Summary Table:
Aspect | Details |
---|---|
Types | Electron beam evaporation (PVD), EB curable coatings |
Key Advantages | Precision, durability, versatility, eco-friendliness |
Applications | Aerospace, automotive, medical, decorative, and functional coatings |
Materials | Metals (e.g., aluminum, gold), dielectrics (e.g., oxides, nitrides) |
Future Trends | Flexible electronics, nanotechnology, renewable energy |
Explore how electron coating can elevate your projects—contact us today for expert guidance!