Evaporation in Physical Vapor Deposition (PVD) is a process where a solid material is heated in a vacuum environment until it vaporizes, and the resulting vapor is then deposited onto a substrate to form a thin film. This method is widely used in industries for coating applications due to its simplicity and effectiveness. There are different types of evaporation techniques, such as thermal evaporation and cathode arc evaporation, each with its own mechanisms and applications. Thermal evaporation uses resistive heating to vaporize the material, while cathode arc evaporation employs a high-power electric arc to ionize the material. Both methods rely on creating a vacuum to ensure the vaporized material travels unimpeded to the substrate.
Key Points Explained:
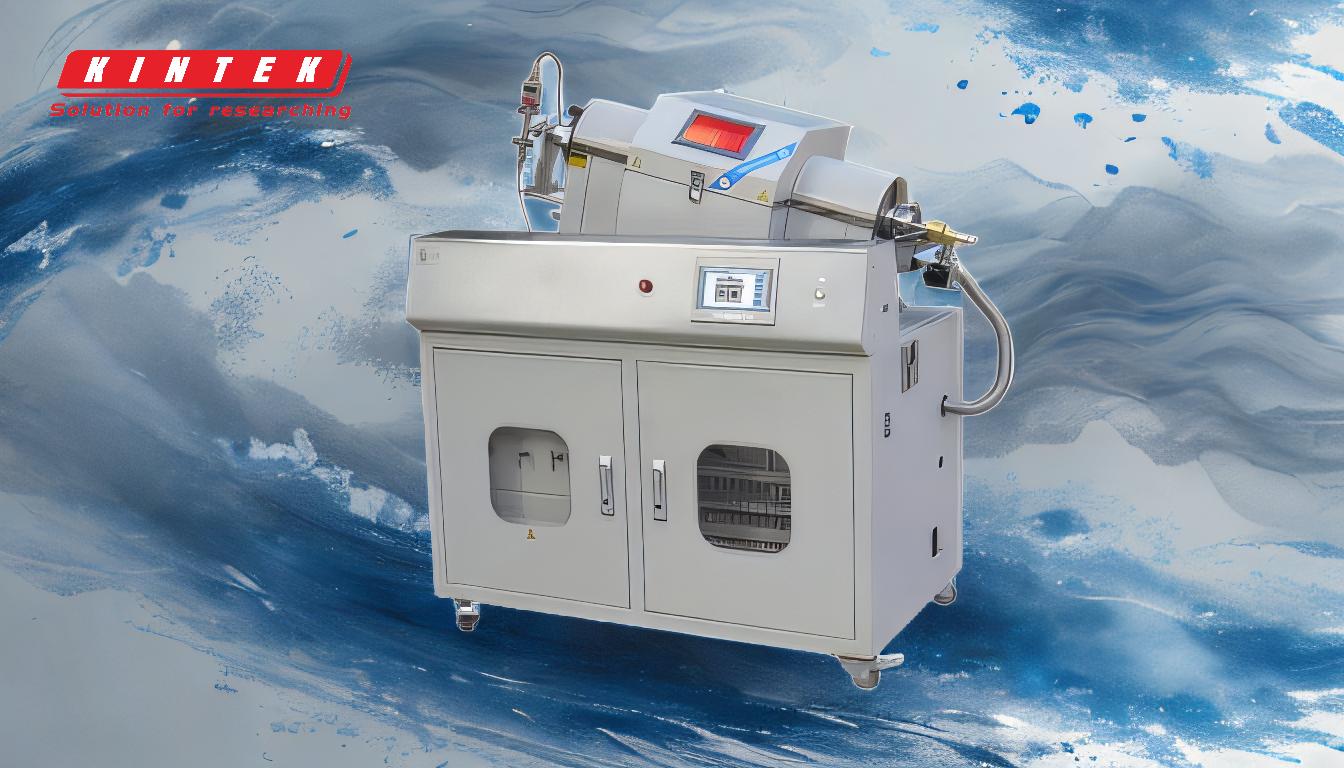
-
Definition of Evaporation in PVD:
- Evaporation in PVD refers to the process of converting a solid material into a vapor phase by heating it in a vacuum. This vapor then condenses onto a substrate to form a thin film. The vacuum environment is crucial as it prevents contamination and ensures the vaporized material travels directly to the substrate without interference from air molecules.
-
Thermal Evaporation:
- Thermal evaporation is one of the simplest and most common PVD techniques. It involves heating the source material using a resistive heat source until it reaches its vapor pressure and evaporates. The vaporized material then travels through the vacuum chamber and deposits onto the substrate. This method is particularly effective for materials with relatively low melting points.
-
Process Steps:
- The material is placed in a high vacuum chamber.
- A resistive heat source (such as a tungsten filament or crucible) heats the material until it vaporizes.
- The vaporized material forms a thin film on the substrate as it condenses.
-
Cathode Arc Evaporation:
- Cathode arc evaporation is another PVD technique where a high-power electric arc is used to vaporize the material. This method ionizes the material almost completely, creating a plasma of metal ions. These ions then interact with reactive gases in the chamber and deposit onto the substrate as a thin film.
-
Process Steps:
- A high-power electric arc is passed over the solid coating material, causing it to evaporate and ionize.
- The ionized material interacts with reactive gases in the vacuum chamber.
- The ions strike the substrate and adhere to it, forming a thin coating.
-
Advantages of Evaporation in PVD:
- High Purity: The vacuum environment ensures that the deposited films are free from contaminants.
- Uniform Coatings: Evaporation techniques can produce very uniform thin films, which are essential for applications in electronics, optics, and other high-precision industries.
- Versatility: Both thermal and cathode arc evaporation can be used with a wide range of materials, including metals, alloys, and compounds.
-
Applications of Evaporation in PVD:
- Electronics: Used for depositing thin films in the manufacture of semiconductors, solar cells, and displays.
- Optics: Applied in the production of anti-reflective coatings, mirrors, and optical filters.
- Decorative Coatings: Utilized for creating decorative finishes on consumer products, such as watches and jewelry.
-
Challenges and Considerations:
- Material Limitations: Some materials may not be suitable for thermal evaporation due to high melting points or other properties.
- Equipment Cost: High vacuum systems and specialized heating sources can be expensive.
- Process Control: Precise control of temperature, pressure, and deposition rate is necessary to achieve high-quality coatings.
In summary, evaporation in PVD is a versatile and effective method for depositing thin films in various industries. Whether using thermal evaporation or cathode arc evaporation, the process relies on creating a vacuum environment to ensure the material vaporizes and deposits uniformly onto the substrate. Understanding the specific requirements and limitations of each technique is crucial for selecting the appropriate method for a given application.
Summary Table:
Aspect | Details |
---|---|
Definition | Conversion of solid material into vapor in a vacuum to form thin films. |
Thermal Evaporation | Uses resistive heating; effective for low-melting-point materials. |
Cathode Arc Evaporation | Uses electric arc to ionize material; creates plasma for deposition. |
Advantages | High purity, uniform coatings, and material versatility. |
Applications | Electronics, optics, and decorative coatings. |
Challenges | Material limitations, equipment cost, and precise process control required. |
Interested in PVD evaporation techniques for your industry? Contact us today to learn more!