Field Assisted Sintering Technique (FAST), also known as Spark Plasma Sintering (SPS), is an advanced sintering method that uses a direct current (DC) electric current to generate heat through Joule heating in the mold and/or sample. This technique enables extremely high heating rates, short processing cycle times, and lower sintering temperatures and pressures compared to conventional methods. FAST is particularly effective for fine metal powder aggregates, as it enhances sintering activity and improves densification while inhibiting grain growth. The process is efficient, cost-effective, and allows for precise control over microstructure and material properties, making it suitable for a wide range of applications in materials science and engineering.
Key Points Explained:
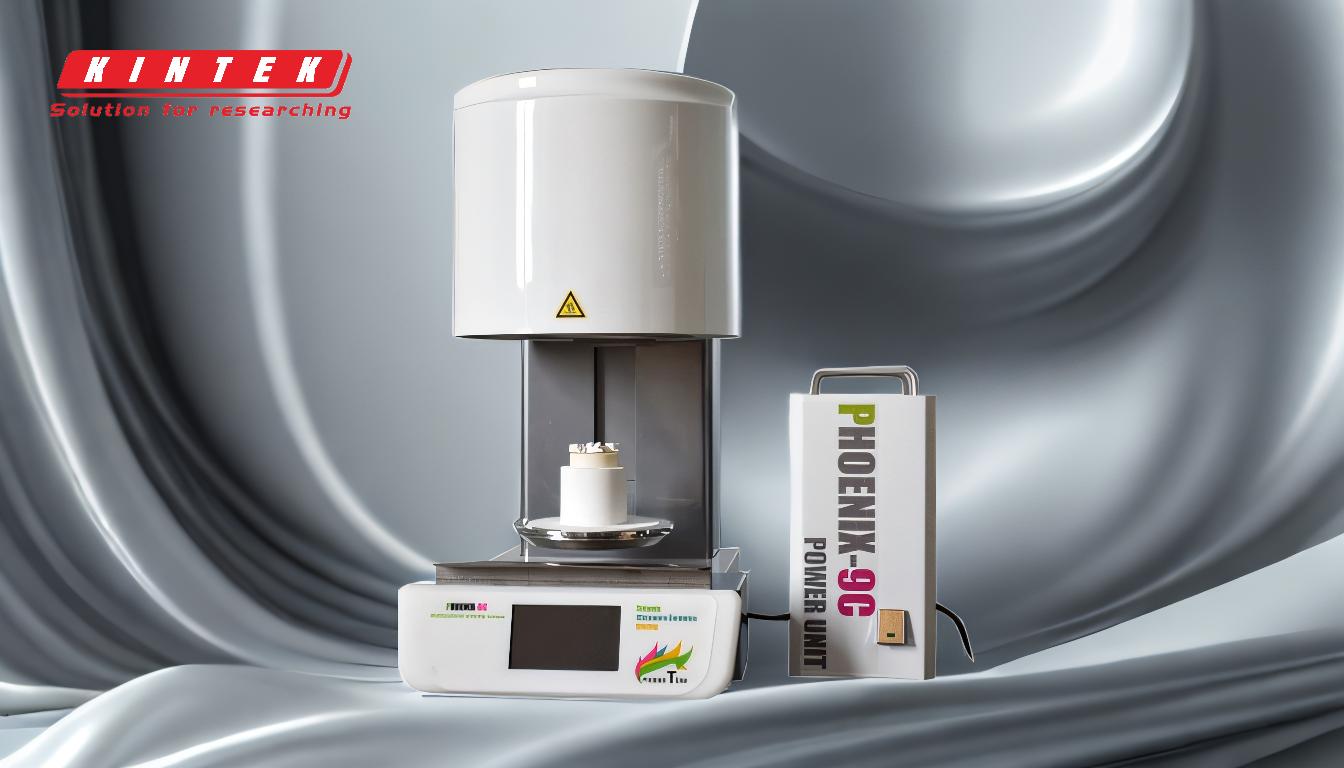
-
Principle of FAST:
- FAST involves directly connecting the mold and/or sample to electrical power.
- Heat is generated through Joule heating due to the resistivity of the mold and the powder.
- This direct heating mechanism results in very high heating rates and increased sintering activity.
-
Advantages of FAST:
- High Heating Rates: FAST achieves rapid heating, significantly reducing processing time.
- Lower Sintering Temperature and Pressure: The technique lowers the threshold for sintering temperature and pressure compared to conventional methods.
- Improved Densification: Enhanced sintering activity leads to better densification of materials.
- Inhibited Grain Growth: The process minimizes grain growth, preserving fine microstructures.
- Short Cycle Times: FAST enables quick processing, making it highly efficient.
- Cost-Effective and Simple Equipment: The method uses relatively simple equipment and is low-cost compared to traditional sintering techniques.
-
Comparison with Conventional Sintering:
- Traditional sintering methods often require longer cycle times, higher temperatures, and more complex equipment.
- FAST reduces these requirements, making it more energy-efficient and suitable for a broader range of materials.
-
Applications and Benefits:
- FAST is particularly effective for fine metal powder aggregates, enabling the production of high-density materials with controlled microstructures.
- The technique is widely used in materials science for developing advanced ceramics, composites, and metallic materials.
- It allows for non-equilibrium sintering, which can produce materials with unique properties not achievable through conventional methods.
-
Technical Details:
- Joule Heating: The primary mechanism of heat generation in FAST, where electrical resistance in the mold and powder converts electrical energy into heat.
- Direct Current (DC): The use of DC ensures consistent and controllable heating, contributing to the precision of the process.
- Uniform Heating: FAST provides uniform heating with minimal temperature gradients, ensuring consistent material properties.
-
Energy Efficiency and Environmental Impact:
- FAST is more energy-efficient than traditional sintering methods due to its rapid heating and lower temperature requirements.
- The reduced energy consumption and shorter processing times contribute to a lower environmental impact.
-
Future Prospects:
- Ongoing research and development in FAST aim to further optimize the process for new materials and applications.
- The technique's ability to produce high-performance materials with tailored properties makes it a promising area for future advancements in materials engineering.
In summary, Field Assisted Sintering Technique (FAST) is a highly efficient and versatile sintering method that offers numerous advantages over traditional techniques. Its ability to achieve rapid heating, lower sintering temperatures, and improved material properties makes it a valuable tool in the field of materials science and engineering.
Summary Table:
Key Aspect | Details |
---|---|
Principle | Uses DC electric current for Joule heating, enabling rapid sintering. |
Advantages | High heating rates, lower temperatures, improved densification, and more. |
Applications | Advanced ceramics, composites, and metallic materials. |
Energy Efficiency | Reduces energy consumption and environmental impact. |
Future Prospects | Promising for producing high-performance materials with tailored properties. |
Unlock the potential of FAST for your material processing needs—contact our experts today!