Fluidized bed pyrolysis is a thermal decomposition process used to convert biomass into bio-oil, syngas, and biochar in the absence of oxygen. It involves a fluidized bed reactor, typically containing a sand bed, where hot gas (often nitrogen) is introduced from the bottom to fluidize the bed and maintain high heating rates. Biomass is fed from the top, and the intense mixing ensures efficient heat transfer and rapid pyrolysis. This method is advantageous due to its simplicity, excellent temperature control, and ability to prevent unwanted reactions. However, it can produce micro carbon particles that are challenging to remove from the vapor phase.
Key Points Explained:
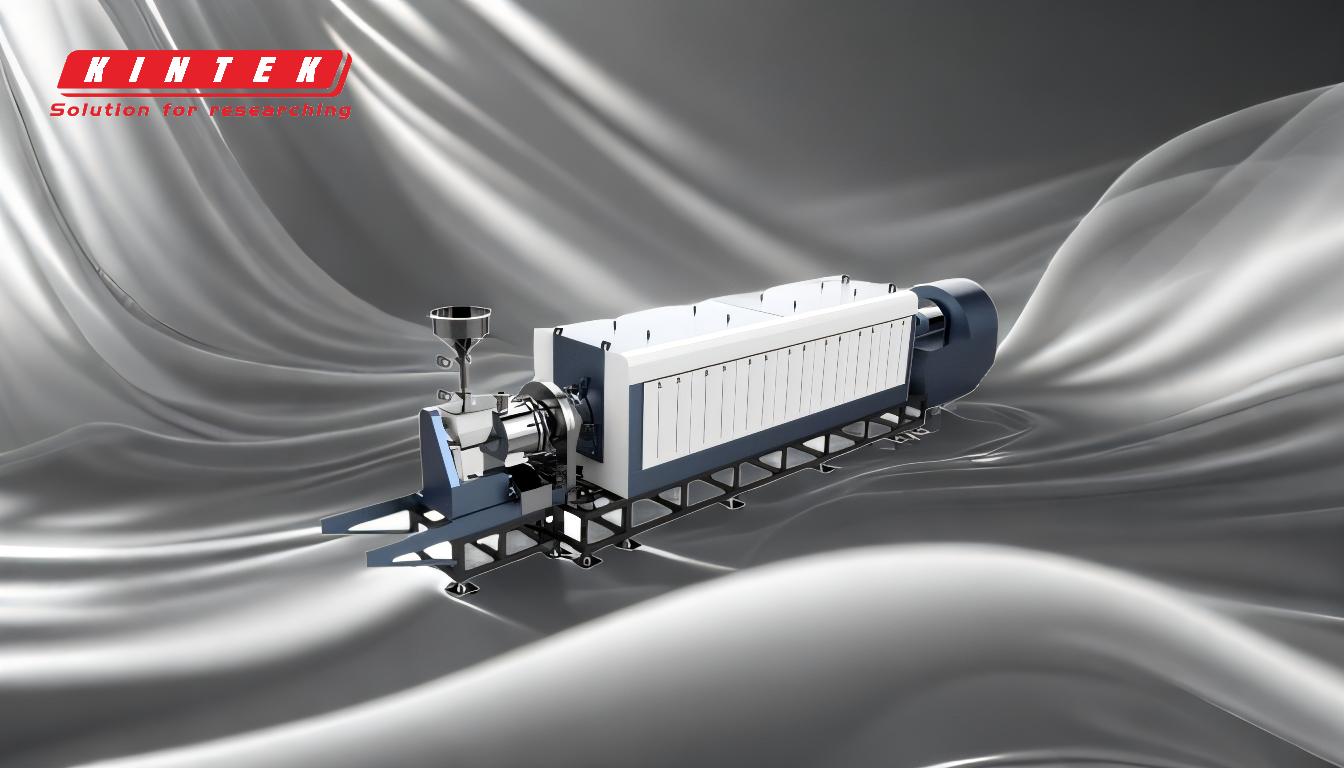
-
Definition and Purpose of Fluidized Bed Pyrolysis:
- Fluidized bed pyrolysis is a thermal decomposition process that breaks down biomass in the absence of oxygen.
- The primary goal is to produce bio-oil, syngas, and biochar, which are valuable energy products.
-
Components of a Fluidized Bed Reactor:
- Sand Bed: Acts as the primary medium for heat transfer. The sand bed is fluidized by hot gas, ensuring uniform temperature distribution.
- Hot Gas Flow: Typically pure nitrogen or another inert gas is introduced from the bottom to maintain an inert atmosphere and prevent unwanted chemical reactions.
- Biomass Feed: Biomass is fed from the top of the reactor, where it interacts with the fluidized sand bed.
-
Heat Transfer Mechanisms:
- Conduction: Approximately 90% of the heat transfer occurs through conduction, where heat is directly transferred from the sand particles to the biomass.
- Convection: The remaining 10% of heat transfer occurs through convection, facilitated by the movement of the fluidizing gas.
- Intense Mixing: The fluidized state ensures intense mixing, which enhances heat transfer efficiency and maintains uniform temperature distribution.
-
Advantages of Fluidized Bed Pyrolysis:
- High Heating Rates: The fluidized bed allows for rapid heating, which is crucial for fast pyrolysis and high yields of bio-oil.
- Temperature Control: The system provides excellent temperature control, which is essential for optimizing the pyrolysis process.
- Efficient Heat Transfer: The intense mixing and direct contact between the biomass and the hot sand particles ensure efficient heat transfer.
- Simplicity: Fluidized bed reactors are well-understood, simple in construction, and easy to operate.
-
Challenges and Considerations:
- Micro Carbon Formation: The process can produce small amounts of micro carbon, which can be difficult to remove from the vapor phase.
- Attrition: The fluidization process causes attrition, which erodes the surface of the biomass and the carbon layer around the catalyst. While this exposes fresh biomass for reaction, it can also lead to the formation of fine particles that need to be managed.
-
Operational Considerations:
- Inert Atmosphere: Maintaining an inert atmosphere (usually with nitrogen) is crucial to prevent oxidation and other unwanted chemical reactions.
- Fluidization Gas: The choice of fluidization gas and its flow rate are critical for maintaining the fluidized state and ensuring efficient heat transfer.
- Biomass Feed Rate: The rate at which biomass is fed into the reactor must be carefully controlled to ensure optimal pyrolysis conditions and product yields.
-
Applications and Relevance:
- Bioenergy Production: Fluidized bed pyrolysis is widely used in the production of bioenergy, including bio-oil and syngas, which can be used as renewable fuels.
- Waste Management: The process can also be applied to the pyrolysis of waste materials, contributing to waste reduction and resource recovery.
- Catalyst Activity: In some cases, catalysts are used to enhance the pyrolysis process, and the fluidized bed helps maintain catalyst activity by continuously exposing fresh surfaces.
In summary, fluidized bed pyrolysis is a highly efficient and well-understood method for converting biomass into valuable energy products. Its advantages include high heating rates, excellent temperature control, and efficient heat transfer, making it a preferred choice for fast pyrolysis applications. However, challenges such as micro carbon formation and attrition need to be managed to optimize the process.
Summary Table:
Aspect | Details |
---|---|
Definition | Thermal decomposition of biomass in the absence of oxygen. |
Purpose | Produces bio-oil, syngas, and biochar for renewable energy. |
Components | Sand bed, hot gas flow (e.g., nitrogen), biomass feed. |
Heat Transfer | 90% conduction, 10% convection; intense mixing ensures efficiency. |
Advantages | High heating rates, excellent temperature control, simplicity. |
Challenges | Micro carbon formation, attrition of biomass and catalyst. |
Applications | Bioenergy production, waste management, catalyst-enhanced pyrolysis. |
Discover how fluidized bed pyrolysis can optimize your biomass conversion process—contact our experts today!