Furnace soldering, often referred to as furnace brazing, is a high-temperature joining process used to bond metal components using a filler metal that melts at a temperature above 450°C (842°F) but below the melting point of the base metals. This process is widely utilized in various industries due to its ability to produce strong, reliable, and precise joints. Common applications include hydraulic fittings, heat exchangers, automotive components, aerospace parts, and medical equipment. The process is particularly valued for its ability to join complex assemblies and dissimilar materials, ensuring high integrity and performance in demanding environments.
Key Points Explained:
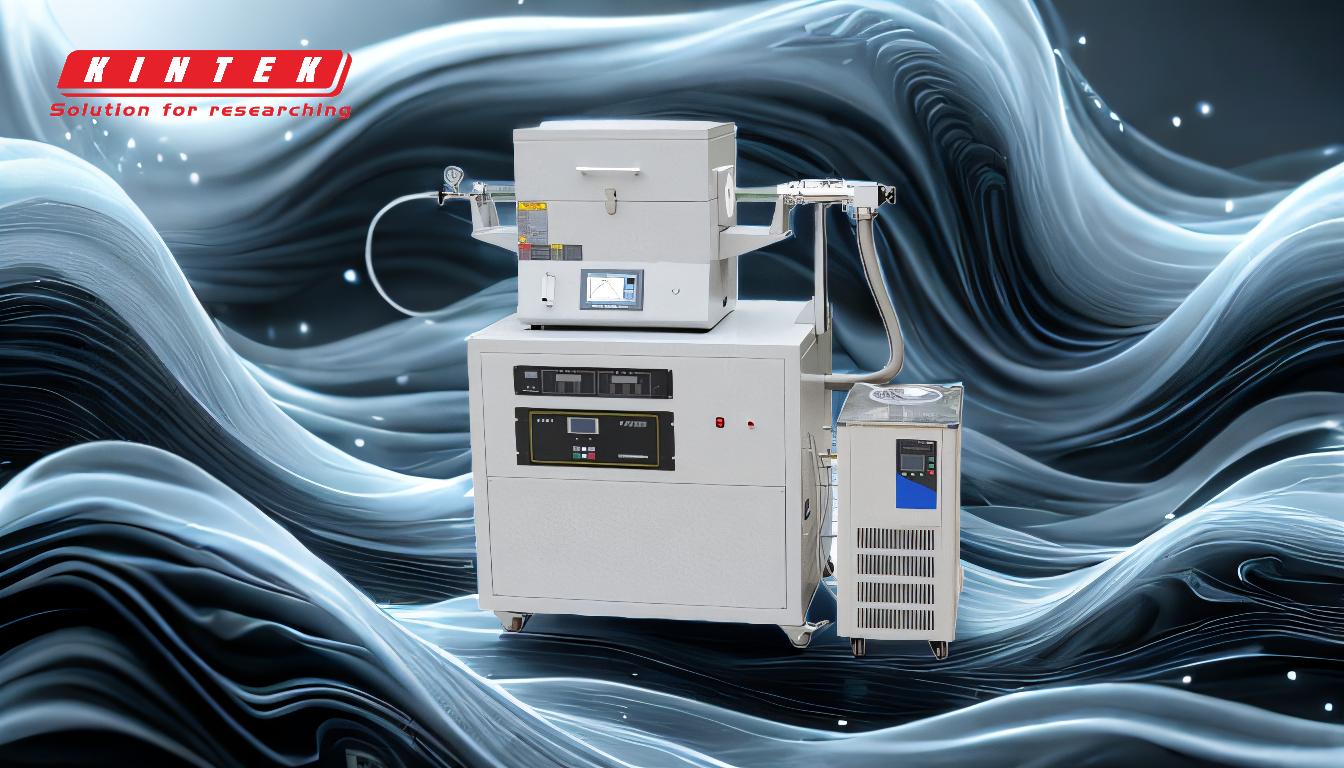
-
Industries and Applications:
- Automotive: Furnace brazing is used to manufacture components such as radiators, heat exchangers, and fuel systems. The process ensures durable and leak-proof joints, which are critical for vehicle performance and safety.
- Aerospace: Components like turbine blades, heat shields, and structural elements are often joined using furnace brazing. The process provides high-strength bonds that can withstand extreme temperatures and stresses encountered in aerospace applications.
- Medical and Scientific Equipment: Precision instruments and devices, such as surgical tools and diagnostic equipment, benefit from the clean and precise joints produced by furnace brazing.
- Industrial Machinery: Hydraulic fittings, tube manipulations, and machined assemblies are commonly brazed using this method, ensuring reliable performance in heavy-duty applications.
-
Advantages of Furnace Brazing:
- High Integrity Joints: The controlled environment of a furnace ensures uniform heating and cooling, leading to strong and consistent joints.
- Ability to Join Dissimilar Materials: Furnace brazing can join metals with different melting points and thermal expansion rates, which is particularly useful in complex assemblies.
- Precision and Cleanliness: The process produces clean joints with minimal distortion, making it ideal for applications requiring high precision and aesthetic quality.
-
Process and Equipment:
- Furnace Types: Various types of furnaces, including muffle furnaces, are used depending on the specific requirements of the application. Muffle furnaces are particularly useful in industries like biomedical, ceramics, and pharmaceuticals due to their ability to provide a controlled atmosphere and high-temperature capabilities.
- Filler Materials: The choice of filler metal is crucial and depends on the base materials and the intended application. Common filler metals include silver, copper, and nickel-based alloys.
-
Material Compatibility:
- Furnace brazing is compatible with a wide range of materials, including stainless steel, aluminum, titanium, and ceramics. This versatility makes it a preferred method in industries dealing with diverse material requirements.
-
Quality and Reliability:
- The process is known for producing high-quality joints with excellent mechanical properties, such as high tensile strength and fatigue resistance. This reliability is essential in critical applications like aerospace and medical devices.
-
Environmental and Economic Benefits:
- Furnace brazing is an environmentally friendly process as it often eliminates the need for fluxes and produces minimal waste. Additionally, the ability to join complex assemblies in a single operation can lead to significant cost savings in manufacturing.
In summary, furnace soldering (brazing) is a versatile and reliable joining process used across various industries to create strong, precise, and high-integrity joints. Its applications range from automotive and aerospace components to medical devices and industrial machinery, making it an indispensable technique in modern manufacturing.
Summary Table:
Aspect | Details |
---|---|
Industries | Automotive, Aerospace, Medical, Industrial Machinery |
Applications | Radiators, Heat Exchangers, Turbine Blades, Surgical Tools |
Advantages | High-integrity joints, Joins dissimilar materials, Precision and cleanliness |
Furnace Types | Muffle furnaces, Controlled atmosphere furnaces |
Filler Materials | Silver, Copper, Nickel-based alloys |
Material Compatibility | Stainless steel, Aluminum, Titanium, Ceramics |
Environmental Benefits | Minimal waste, No need for fluxes, Cost-effective |
Learn how furnace soldering can enhance your manufacturing process—contact us today for expert guidance!