Heat treatment is a critical process in the manufacturing and finishing of metal castings, as it enhances their mechanical properties, relieves internal stresses, and improves their overall performance. For castings, heat treatment can adjust properties such as hardness, strength, ductility, and toughness, making them suitable for specific applications. It also addresses issues like residual stresses from casting or machining, ensuring dimensional stability and preventing warping or cracking. Additionally, heat treatment can reduce magnetic permeability in materials like 1008 or 316, which is essential for parts used in electronic environments. By controlling heating and cooling rates, heat treatment refines the microstructure of metals, optimizing their performance for demanding applications.
Key Points Explained:
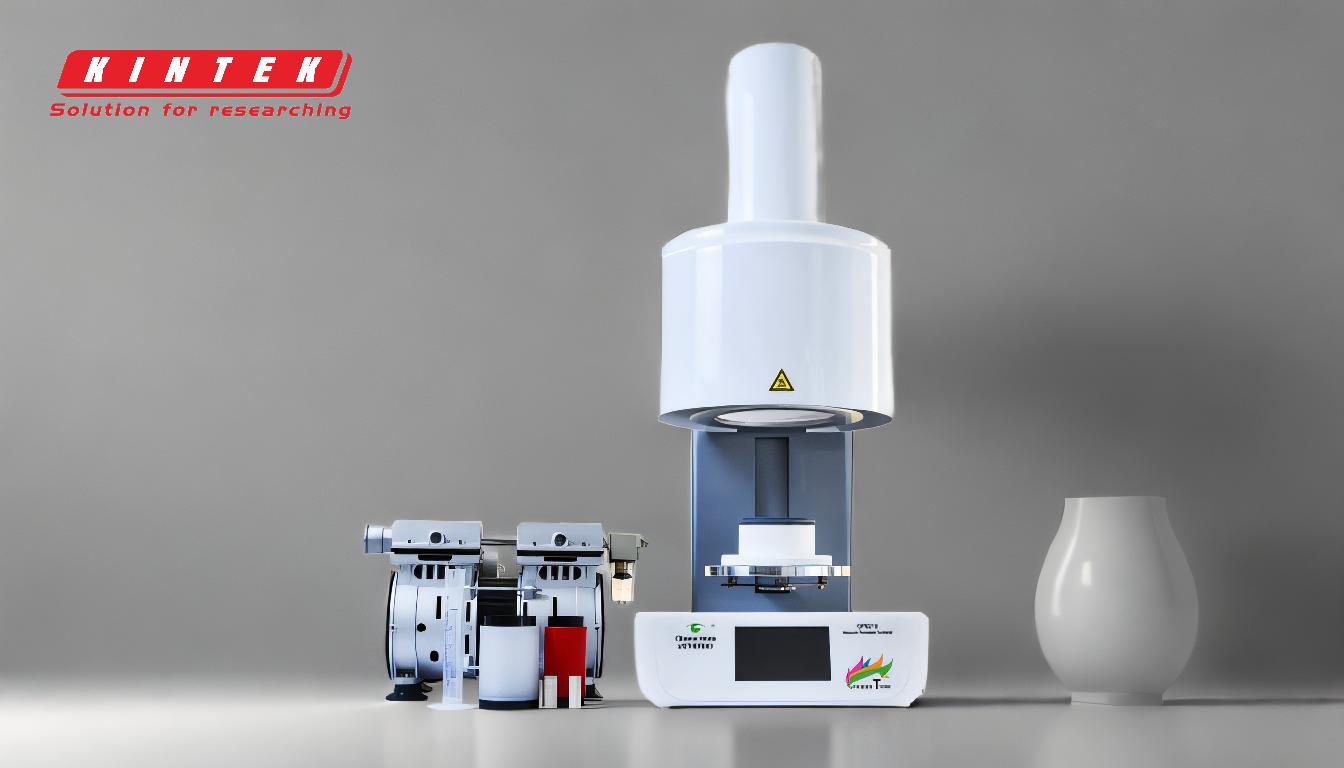
-
Enhancing Mechanical Properties:
- Heat treatment is used to manipulate the mechanical properties of castings, such as hardness, strength, toughness, ductility, and elasticity. This is achieved by controlling the rate of diffusion and cooling within the metal's microstructure.
- For example, annealing can soften a metal, making it more ductile, while quenching and tempering can increase hardness and strength.
- This is particularly important for castings that need to withstand high stress or wear in their final applications.
-
Relieving Residual Stresses:
- During casting or machining, residual stresses can build up in the metal due to uneven cooling or mechanical deformation. These stresses can lead to warping, cracking, or dimensional instability.
- Heat treatment, such as stress relieving, helps to reduce these internal stresses, ensuring the casting maintains its shape and integrity.
- This is especially critical for complex or precision components where dimensional accuracy is essential.
-
Improving Microstructure:
- Heat treatment refines the microstructure of cast metals, which directly impacts their performance. For instance, processes like normalizing or solution annealing can homogenize the grain structure, improving uniformity and mechanical properties.
- A refined microstructure also enhances resistance to fatigue, corrosion, and other forms of degradation, making the casting more durable.
-
Reducing Magnetic Permeability:
- Certain materials, such as 1008 or 316 stainless steel, can become magnetized when work-hardened during machining or forming. This can be problematic for parts used in electronic environments.
- A specific annealing process can reduce magnetic permeability, ensuring the casting performs reliably in sensitive applications.
-
Applications in Additive Manufacturing:
- Heat treatment is also crucial for metal parts produced via additive manufacturing (e.g., SLM, DMLS, or L-PBF). During printing, thermal stresses accumulate due to uneven heating and cooling, leading to stress gradients between layers.
- Heat treatment after printing helps to relieve these stresses, preventing warping or build failure. This ensures the final part meets the required mechanical and dimensional specifications.
-
Expanding Application Potential:
- By improving properties like hardness, corrosion resistance, and shear strength, heat treatment expands the range of applications for castings. For example, vacuum heat treatment can enhance corrosion resistance, making the casting suitable for harsh environments.
- This allows castings to be used in more demanding industries, such as aerospace, automotive, and electronics.
In summary, heat treatment is a versatile and essential process for castings, addressing issues like mechanical performance, stress relief, and microstructure refinement. It ensures that castings meet the stringent requirements of their intended applications, making them more reliable and durable.
Summary Table:
Purpose of Heat Treatment | Key Benefits |
---|---|
Enhancing Mechanical Properties | Improves hardness, strength, ductility, and toughness for high-stress applications. |
Relieving Residual Stresses | Reduces internal stresses, preventing warping, cracking, and dimensional instability. |
Improving Microstructure | Refines grain structure for better uniformity, fatigue resistance, and durability. |
Reducing Magnetic Permeability | Lowers magnetic permeability in materials like 1008 or 316 for electronic applications. |
Applications in Additive Manufacturing | Relieves thermal stresses in 3D-printed parts, ensuring mechanical and dimensional accuracy. |
Expanding Application Potential | Enhances properties like corrosion resistance, enabling use in aerospace and automotive industries. |
Unlock the full potential of your metal castings with expert heat treatment solutions—contact us today!