High-density plasma chemical vapor deposition (HDP-CVD) is an advanced variation of the chemical vapor deposition (CVD) process, specifically designed to enhance the quality and efficiency of thin film deposition. It leverages high-density plasma to achieve better control over the deposition process, enabling the creation of highly uniform and dense films. This method is particularly useful in semiconductor manufacturing, where precision and material quality are critical. The process involves the generation of plasma to ionize gas molecules, which then react to form a thin film on the substrate. HDP-CVD is known for its ability to deposit films at lower temperatures compared to traditional CVD, making it suitable for temperature-sensitive materials.
Key Points Explained:
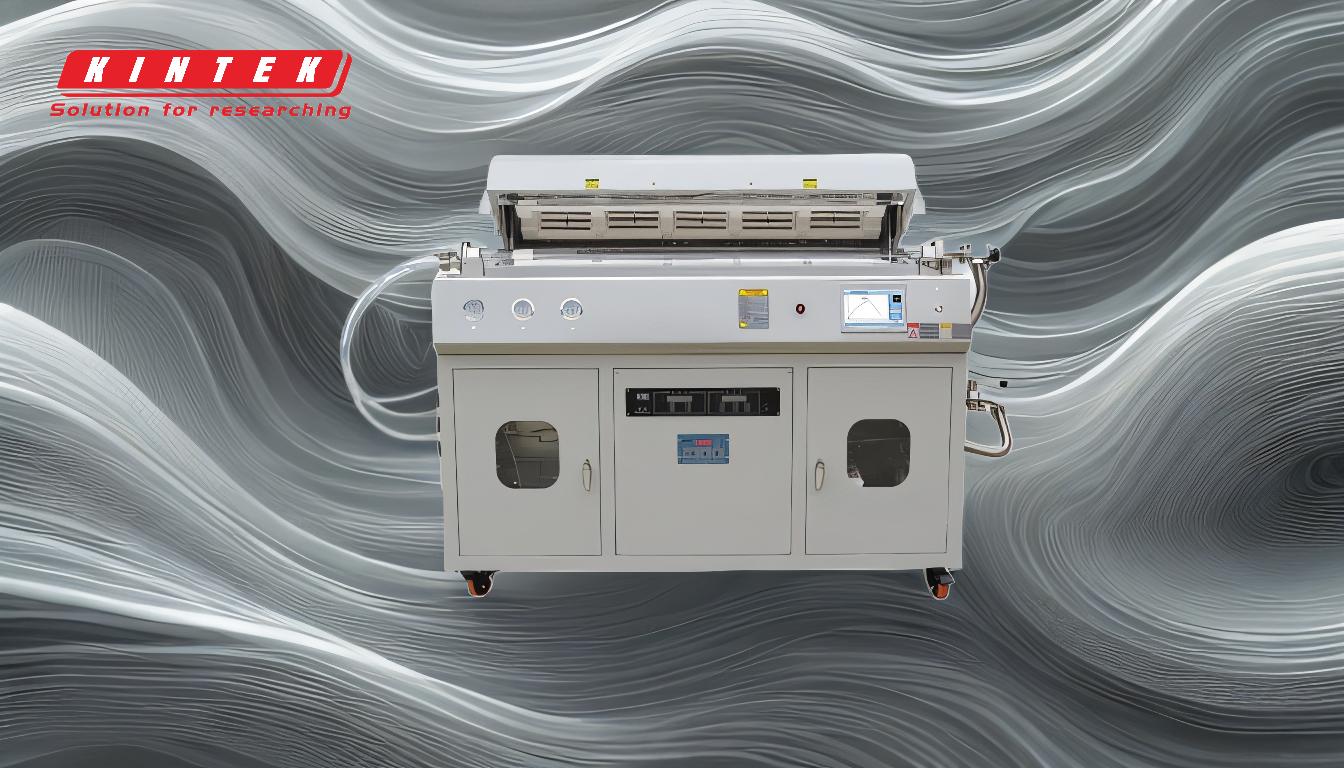
-
Introduction to HDP-CVD:
- High-density plasma chemical vapor deposition (HDP-CVD) is a specialized form of CVD that uses high-density plasma to enhance the deposition process.
- The plasma is generated using electromagnetic fields, which ionize the gas molecules, creating a highly reactive environment for film formation.
-
Steps in the HDP-CVD Process:
- Transport of Gaseous Species: Reacting gases are introduced into the chamber and transported to the substrate surface.
- Plasma Generation: High-density plasma is generated using radio frequency (RF) or microwave energy, ionizing the gas molecules.
- Surface Reactions: The ionized species react on the substrate surface, forming a thin film.
- Film Growth and Desorption: The film grows as the reaction continues, and byproducts are desorbed and removed from the chamber.
-
Advantages of HDP-CVD:
- Lower Deposition Temperatures: HDP-CVD can deposit films at lower temperatures compared to traditional CVD, making it suitable for temperature-sensitive substrates.
- Improved Film Quality: The high-density plasma ensures a more uniform and dense film, with fewer defects.
- Enhanced Step Coverage: HDP-CVD provides excellent step coverage, even on complex geometries, which is crucial for semiconductor devices.
-
Applications of HDP-CVD:
- Semiconductor Manufacturing: HDP-CVD is widely used in the fabrication of integrated circuits, where it is used to deposit dielectric layers, such as silicon dioxide and silicon nitride.
- Optoelectronics: The process is also used in the production of optoelectronic devices, where high-quality thin films are essential for performance.
- MEMS and Nanotechnology: HDP-CVD is employed in the fabrication of microelectromechanical systems (MEMS) and nanostructures, where precise control over film properties is required.
-
Comparison with Other CVD Methods:
- Plasma-Enhanced CVD (PECVD): While PECVD also uses plasma, HDP-CVD operates at higher plasma densities, resulting in better film quality and lower deposition temperatures.
- Atmospheric Pressure CVD (APCVD): Unlike APCVD, which operates at atmospheric pressure, HDP-CVD is performed in a vacuum, allowing for better control over the deposition environment.
- Low-Pressure CVD (LPCVD): HDP-CVD offers advantages over LPCVD in terms of deposition rate and film uniformity, especially for complex structures.
-
Key Process Parameters:
- Plasma Density: The density of the plasma is a critical parameter, as it directly affects the reaction rate and film quality.
- Substrate Temperature: Although HDP-CVD can operate at lower temperatures, the substrate temperature still plays a role in determining the film properties.
- Chamber Pressure: The pressure within the deposition chamber influences the mean free path of the gas molecules, affecting the deposition rate and film uniformity.
-
Challenges and Considerations:
- Plasma Uniformity: Achieving uniform plasma density across the substrate is challenging but essential for consistent film quality.
- Material Compatibility: The choice of materials for the chamber and electrodes must consider their compatibility with the plasma and reactive gases.
- Process Control: Precise control over the plasma generation, gas flow, and substrate temperature is necessary to achieve the desired film properties.
In summary, high-density plasma chemical vapor deposition is a sophisticated and highly controlled process that offers significant advantages in terms of film quality, deposition temperature, and step coverage. Its applications in semiconductor manufacturing, optoelectronics, and nanotechnology highlight its importance in modern technology. The process involves careful management of plasma density, substrate temperature, and chamber pressure to achieve optimal results.
Summary Table:
Aspect | Details |
---|---|
Process Overview | Uses high-density plasma to enhance thin film deposition. |
Key Advantages | Lower deposition temperatures, improved film quality, enhanced step coverage. |
Applications | Semiconductor manufacturing, optoelectronics, MEMS, and nanotechnology. |
Comparison to CVD | Superior to PECVD, APCVD, and LPCVD in quality and uniformity. |
Key Parameters | Plasma density, substrate temperature, and chamber pressure. |
Challenges | Plasma uniformity, material compatibility, and precise process control. |
Discover how HDP-CVD can revolutionize your thin film processes—contact our experts today!