A high-frequency induction furnace is a specialized type of induction furnace that uses high-frequency alternating currents to generate heat within conductive materials through electromagnetic induction. This furnace is widely used in industries for melting, heating, and heat treatment of metals due to its efficiency, precision, and ability to operate under various atmospheres. The furnace works by passing a high-frequency electrical current through a copper coil, creating a fluctuating magnetic field that induces eddy currents in the conductive material placed within the coil. These eddy currents generate heat through resistance, melting or heating the material uniformly. The furnace's design includes key components such as a power supply, induction coil, crucible, and control system, ensuring optimal performance and safety.
Key Points Explained:
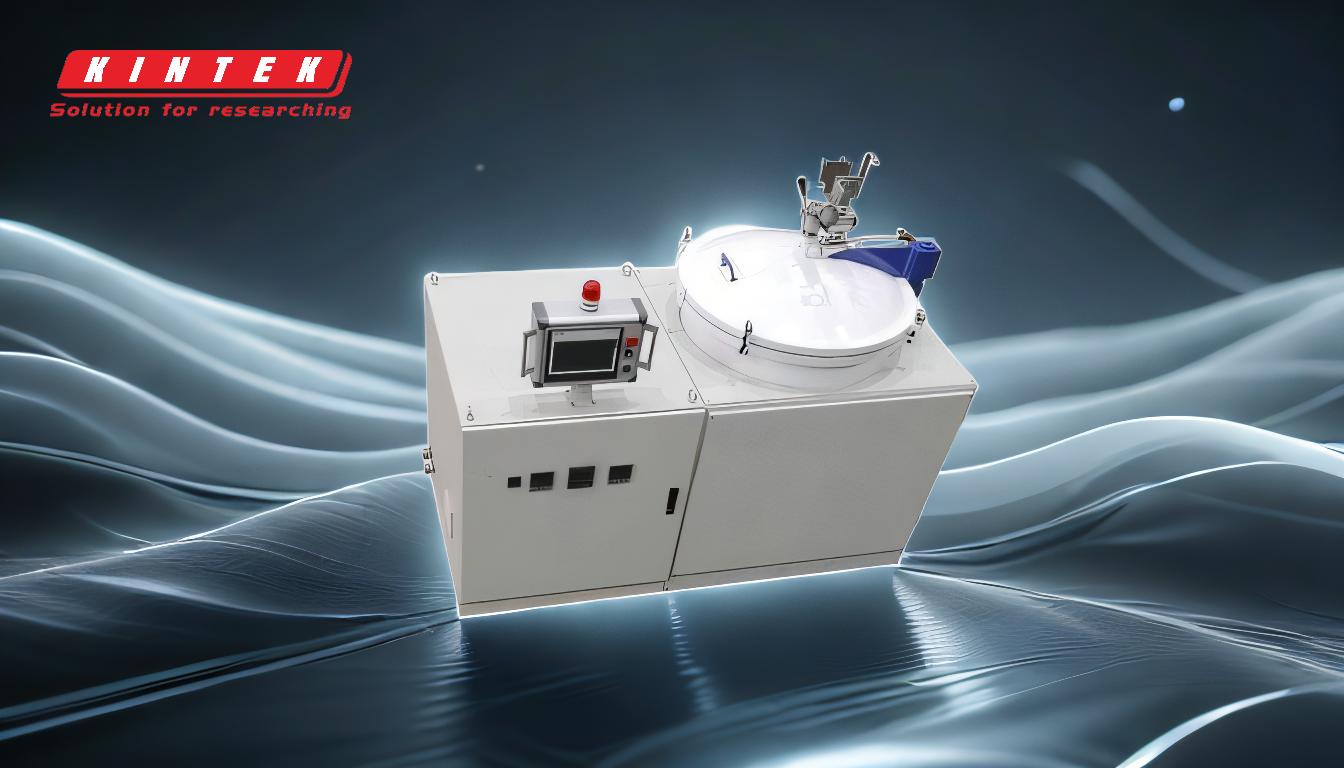
-
Working Principle of High-Frequency Induction Furnace:
- The furnace operates on the principle of electromagnetic induction. A high-frequency alternating current is passed through a copper coil, creating a fluctuating magnetic field.
- When a conductive material is placed within this magnetic field, eddy currents are induced within the material. These currents generate heat through resistance, leading to the melting or heating of the material.
- The heat is generated internally within the material, ensuring uniform heating and efficient energy use.
-
Key Components:
- Induction Coil: A hollow copper coil that carries the high-frequency current and generates the electromagnetic field.
- Crucible: A container made of refractory materials that holds the material to be heated or melted. It can be made of non-conductive or conductive materials depending on the application.
- Power Supply: Converts three-phase alternating current into high-frequency current suitable for induction heating. Modern furnaces often use IGBT induction furnace technology for efficient power conversion.
- Control System: Manages the operation of the furnace, including temperature control, power regulation, and safety features.
-
Advantages of High-Frequency Induction Furnace:
- Efficiency: The heat is generated directly within the material, reducing energy loss and ensuring high thermal efficiency.
- Precision: The furnace allows for precise control of temperature and heating rates, making it suitable for applications requiring strict temperature control.
- Uniform Heating: The eddy currents ensure uniform heating throughout the material, avoiding hot spots and ensuring consistent quality.
- Versatility: The furnace can operate under various atmospheres (e.g., air, vacuum, or inert gas), making it suitable for a wide range of materials and processes.
-
Applications:
- Metal Melting: Commonly used for melting metals such as steel, iron, aluminum, and copper alloys.
- Heat Treatment: Used for processes like annealing, hardening, and tempering of metals.
- Precision Casting: Ideal for applications requiring precise control over melting and casting processes.
- Laboratory Use: Used in research and development for small-scale melting and heating experiments.
-
Types of Induction Furnaces:
- Coreless Induction Furnace: Does not have a core, making it suitable for melting a wide range of metals.
- Channel Induction Furnace: Contains a refractory-lined steel shell with a molten metal loop acting as the secondary component of a transformer, providing a stirring action in the melt.
- Vacuum Induction Furnace: Designed to operate under vacuum conditions, ideal for melting high-purity metals and alloys.
-
Modern Innovations:
- IGBT Technology: The use of IGBT induction furnace technology in modern furnaces improves power efficiency, reduces energy consumption, and enhances control over the heating process.
- Automation: Advanced control systems and automation have made induction furnaces more user-friendly and capable of handling complex processes with minimal manual intervention.
In conclusion, the high-frequency induction furnace is a versatile and efficient tool for melting and heating conductive materials. Its ability to generate heat directly within the material, combined with precise control and uniform heating, makes it indispensable in various industrial applications. The integration of modern technologies like IGBT induction furnace further enhances its performance, making it a preferred choice for high-quality metal processing.
Summary Table:
Aspect | Details |
---|---|
Working Principle | Uses electromagnetic induction to generate heat within conductive materials |
Key Components | Induction coil, crucible, power supply, control system |
Advantages | High efficiency, precise control, uniform heating, versatile operation |
Applications | Metal melting, heat treatment, precision casting, laboratory use |
Types | Coreless, channel, vacuum induction furnaces |
Modern Innovations | IGBT technology, automation for improved efficiency and control |
Ready to enhance your metal processing capabilities? Contact us today to learn more about high-frequency induction furnaces!