Hot isostatic pressing (HIP) treatment porosity refers to the process of eliminating internal voids or porosities in materials, particularly metals and alloys, through the application of high temperature and uniform pressure. This process results in materials that are nearly fully dense, with improved mechanical properties such as increased resistance to heat, wear, fatigue, and abrasion. The HIP process involves loading components into a chamber, heating them, and applying inert gas pressure to uniformly compress and eliminate internal defects. This technique is widely used in industries requiring high-performance materials, such as aerospace and automotive, to enhance the quality and reliability of components.
Key Points Explained:
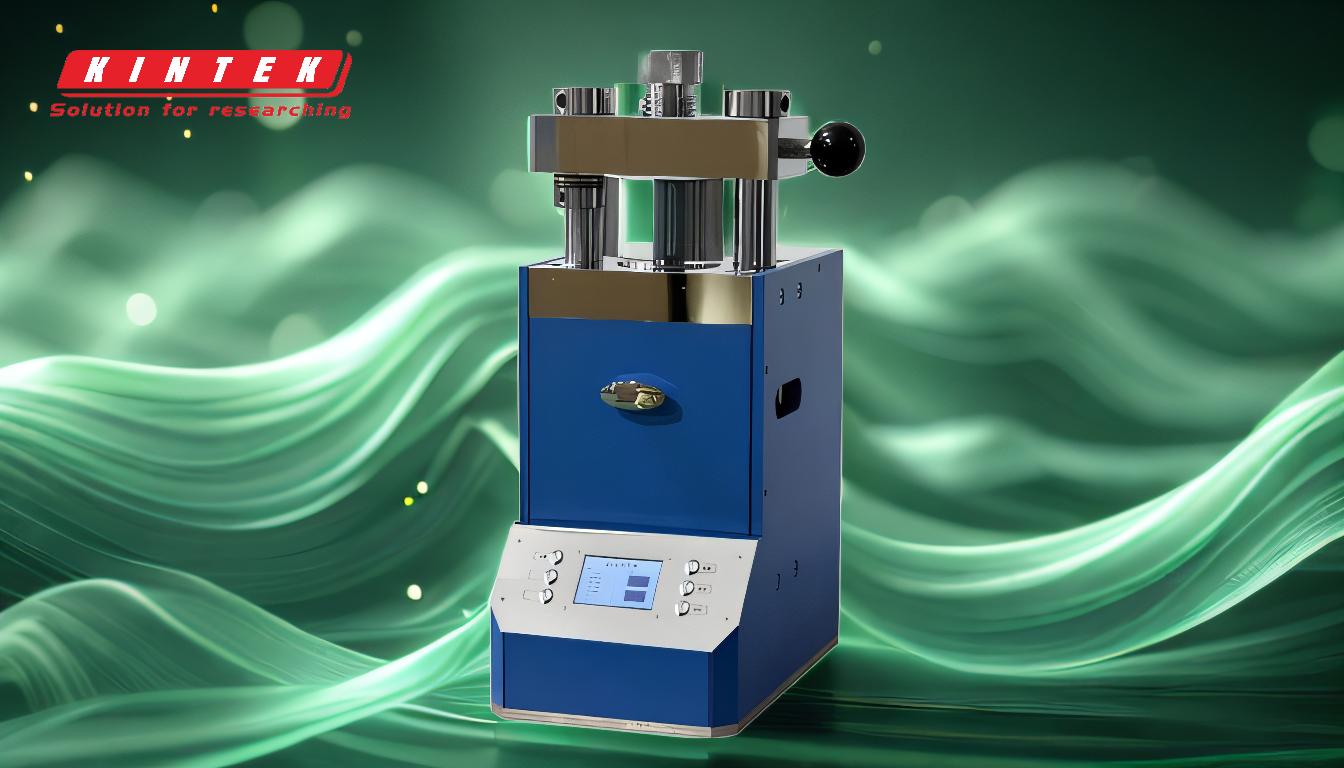
-
Definition of Hot Isostatic Pressing (HIP) Treatment Porosity:
- HIP treatment porosity is a process that removes internal voids or porosities in materials by applying high temperature and uniform pressure. This results in materials with nearly full density and improved mechanical properties.
-
Process of Hot Isostatic Pressing:
- Loading: Parts or components are placed into a heating chamber.
- Heating and Pressurization: The chamber is heated, and inert argon gas is applied under high pressure.
- Monitoring: Temperature, pressure, and process time are closely controlled.
- Depressurization and Cooling: The process ends with a gradual reduction in pressure and a cooling phase to ensure the parts are safe to handle.
-
Benefits of HIP Treatment:
- Elimination of Porosities: HIP completely removes internal voids, leading to higher density and improved material integrity.
- Enhanced Mechanical Properties: The process increases resistance to heat, wear, fatigue, and abrasion.
- Improved Production Efficiency: HIP allows for the production of higher quality parts that can withstand harsh environments.
-
Applications of HIP:
- Metal Types: Commonly used on titanium, aluminum, and high-temperature alloys.
- Material Forms: Applicable to both solid and powder forms, including powder alloys.
- Industries: Widely used in aerospace, automotive, and other industries requiring high-performance materials.
-
Comparison with Other Methods:
- Lower Temperature Operation: Compared to hot pressing, HIP operates at lower temperatures while achieving higher density products.
- Uniform Density: HIP ensures a uniform distribution of phases and fine grain structure, resulting in isotropic properties.
-
Technological Advantages:
- Defect Elimination: HIP technology is effective in removing internal defects caused by uneven cooling rates during the forming process of castings.
- Material Bonding: HIP enables the bonding or cladding of multiple materials, enhancing the versatility of the process.
-
Role of Warm Isostatic Press:
- A warm isostatic press is a variant of HIP that operates at lower temperatures, typically using a heated liquid medium. This method is particularly useful for materials that require precise temperature control and uniform pressure application.
By understanding the principles and benefits of hot isostatic pressing treatment porosity, manufacturers can produce high-quality, durable components that meet the demanding requirements of various industries.
Summary Table:
Aspect | Details |
---|---|
Definition | Process to eliminate internal voids using high temperature and pressure. |
Process Steps | Loading, heating, pressurization, monitoring, depressurization, cooling. |
Benefits | Higher density, improved heat/wear resistance, enhanced material integrity. |
Applications | Aerospace, automotive, titanium, aluminum, high-temperature alloys. |
Comparison | Lower temperature operation, uniform density, isotropic properties. |
Technological Advantages | Defect elimination, material bonding, versatility. |
Learn how HIP can transform your materials—contact us today for expert guidance!