Hot press forging is a manufacturing process that involves shaping metal using localized compressive forces at elevated temperatures. This method is widely used in industries to produce high-strength, durable components with precise dimensions. The process typically involves heating the metal to a temperature above its recrystallization point, making it more malleable and easier to shape under pressure. Hot press forging is essential for creating complex geometries and ensuring the material's internal grain structure is aligned, which enhances the mechanical properties of the final product.
Key Points Explained:
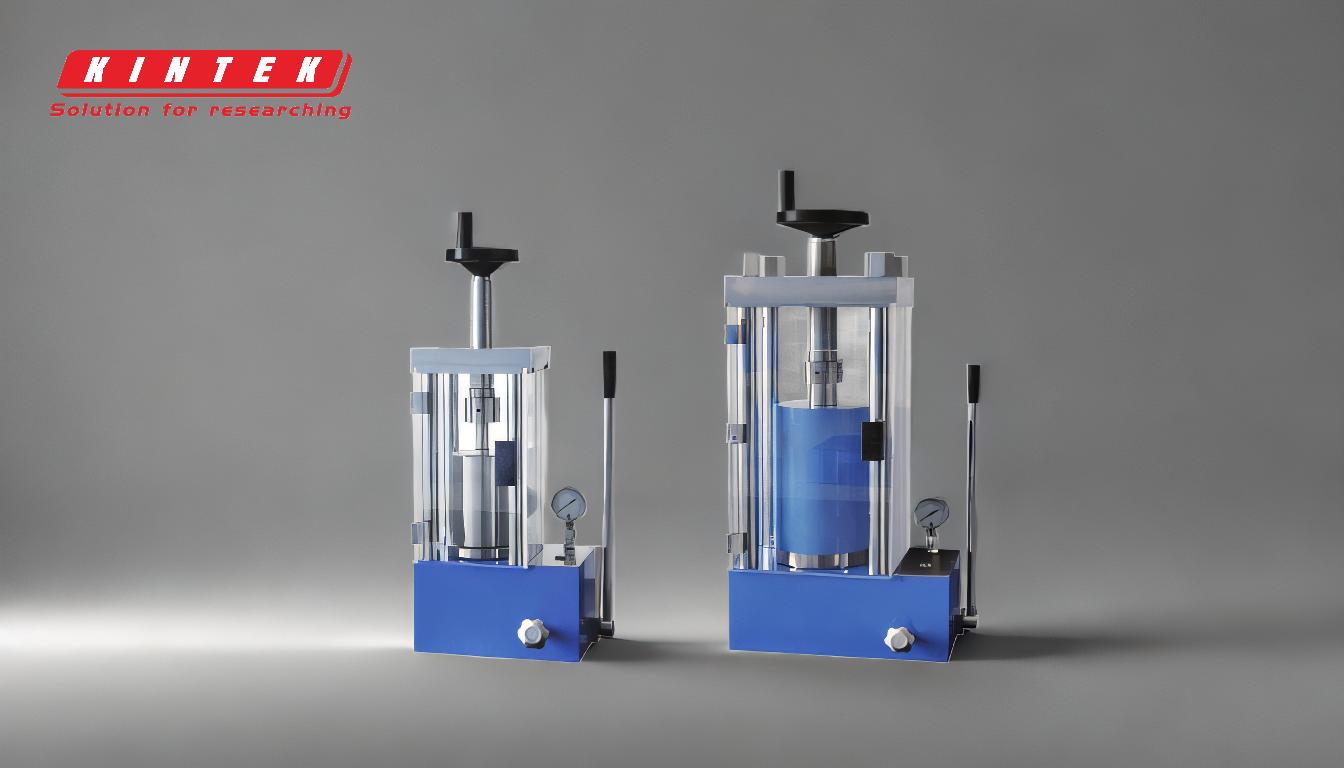
-
Definition of Hot Press Forging:
- Hot press forging is a metalworking process where metal is heated to a high temperature and then shaped using compressive forces. The elevated temperature reduces the metal's yield strength and allows it to deform more easily under pressure. This process is particularly useful for creating parts with intricate shapes and high strength requirements.
-
Industrial Applications:
- Hot press forging is widely used in various industries, including automotive, aerospace, and manufacturing. It is employed to produce components such as gears, crankshafts, and connecting rods, which require high strength and durability. Additionally, it is used in the production of coins, silver articles, and other precision parts where material integrity and dimensional accuracy are critical.
-
Advantages of Hot Press Forging:
- Improved Mechanical Properties: The process aligns the metal's grain structure, enhancing its strength, toughness, and fatigue resistance.
- Complex Geometries: Hot press forging allows for the creation of intricate shapes that would be difficult or impossible to achieve with cold forging.
- Material Efficiency: The process minimizes material waste, as the metal is shaped precisely to the desired form.
-
Role of the Hot Press Machine:
- The hot press machine is a critical component in the forging process. It applies the necessary compressive force to shape the heated metal. These machines are designed to handle high temperatures and pressures, ensuring consistent and precise results. They come in various configurations, including hydraulic and mechanical presses, each suited for specific applications.
-
Comparison with Other Forging Methods:
- Cold Forging: Unlike hot press forging, cold forging is performed at or near room temperature. While it offers higher precision and surface finish, it is limited to simpler shapes and requires more force to deform the metal.
- Warm Forging: This method operates at intermediate temperatures, offering a balance between the benefits of hot and cold forging. It is often used for materials that are difficult to forge at room temperature but do not require the high temperatures of hot forging.
-
Material Considerations:
- The choice of material is crucial in hot press forging. Common materials include carbon steel, alloy steel, stainless steel, and non-ferrous metals like aluminum and copper. The material's properties, such as melting point and ductility, determine the optimal forging temperature and pressure.
-
Process Steps:
- Heating: The metal is heated to a temperature above its recrystallization point, typically between 950°C and 1250°C for steel.
- Forging: The heated metal is placed in the hot press machine, where it is shaped using dies that apply compressive force.
- Cooling: The forged part is cooled, either naturally or through controlled processes, to achieve the desired mechanical properties.
- Finishing: The final product may undergo additional processes such as machining, heat treatment, or surface finishing to meet specific requirements.
-
Quality Control:
- Ensuring the quality of hot press forged parts involves rigorous inspection and testing. Techniques such as ultrasonic testing, magnetic particle inspection, and dimensional checks are used to verify the integrity and accuracy of the forged components.
By understanding these key points, one can appreciate the significance of hot press forging in modern manufacturing and its role in producing high-performance components across various industries.
Summary Table:
Aspect | Details |
---|---|
Definition | Shaping metal using compressive forces at elevated temperatures. |
Applications | Automotive, aerospace, manufacturing (gears, crankshafts, etc.). |
Advantages | Improved strength, complex geometries, material efficiency. |
Key Equipment | Hot press machine for applying compressive force. |
Comparison | Superior to cold forging for complex shapes and strength. |
Materials | Carbon steel, alloy steel, stainless steel, aluminum, copper. |
Process Steps | Heating, forging, cooling, finishing. |
Quality Control | Ultrasonic testing, magnetic particle inspection, dimensional checks. |
Learn how hot press forging can enhance your manufacturing process—contact our experts today!