A hydrogen bell-type annealing furnace is a specialized heating equipment that uses hydrogen or a hydrogen-nitrogen mixture as a protective atmosphere to anneal materials. This furnace is designed to heat materials above their recrystallization temperature, making them more ductile and easier to work with. It is widely used in industries such as metallurgy, ceramics, and semiconductors for processes like sintering, brazing, and purification. The furnace features advanced controls, precise temperature regulation, and a robust hydraulic system, ensuring high-quality results. Its ability to handle a wide range of materials and processes makes it a versatile and essential tool in modern manufacturing.
Key Points Explained:
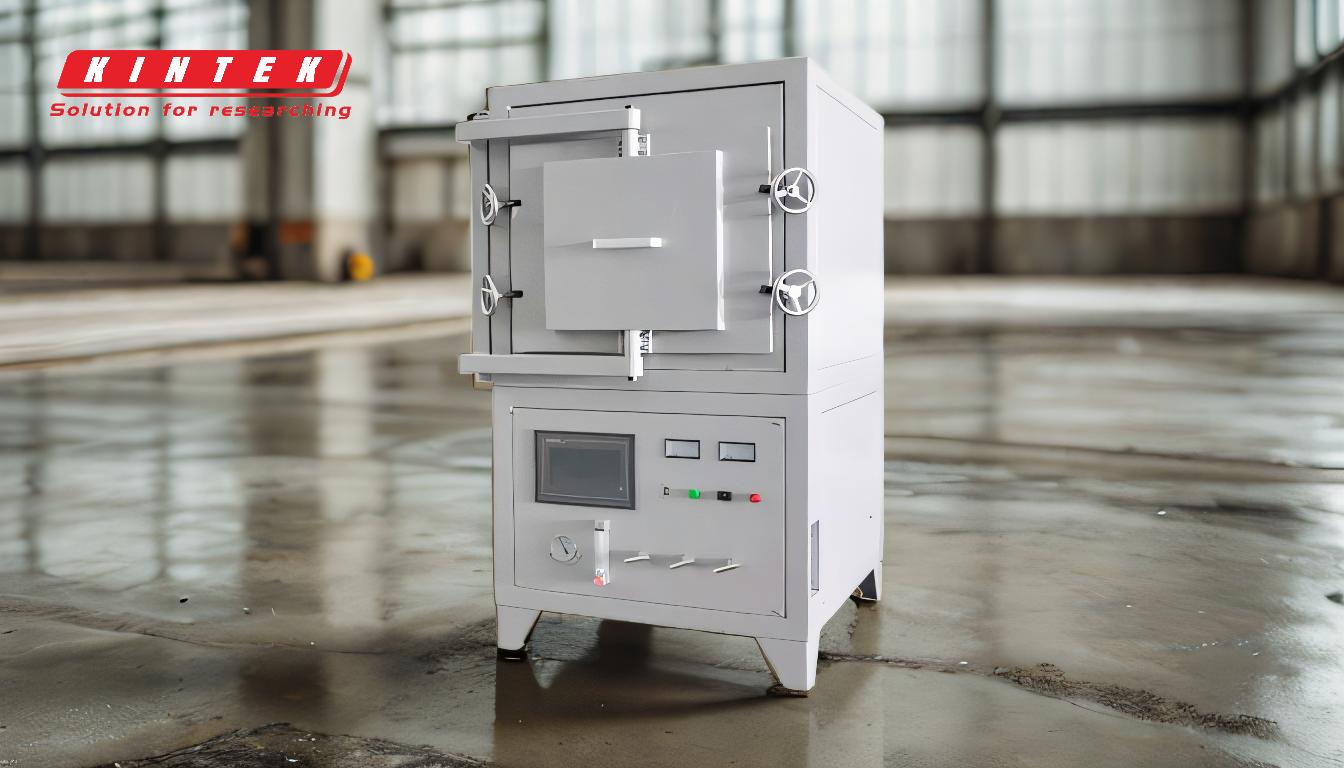
-
Definition and Purpose:
- A hydrogen bell-type annealing furnace is a heating device that uses hydrogen or a hydrogen-nitrogen mixture (with hydrogen content >5%) as a protective atmosphere. This prevents oxidation and contamination during the annealing process.
- The primary purpose of this furnace is to heat materials above their recrystallization temperature, which improves ductility, relieves internal stresses, and enhances material properties like strength and hardness.
-
Key Features:
- Temperature Control: The furnace can reach a maximum temperature of 1600℃ with automatic temperature control precision of ±1℃. Temperature uniformity ranges from ±3℃ to ±10℃, ensuring consistent results.
- Control Systems: It features both automatic and manual control options, along with a piecewise program temperature controller for precise heating cycles.
- Heating Mechanism: A magnetic transformer is used for efficient heating, while a hydraulic system ensures smooth operation and pressure control for water and air systems.
- Additional Features: The furnace is equipped with a paperless recorder for data logging and has a stainless steel table plate for durability and aesthetic appeal.
-
Applications:
- Ceramic Sintering: Used to sinter ceramic materials, making them denser and stronger.
- Metallization and Brazing: Ideal for bonding metals and creating strong joints.
- Glass Parts Sealing: Ensures airtight seals in glass components.
- Metal Parts Annealing: Enhances the mechanical properties of metal parts by relieving stresses and improving ductility.
- Purification and Powder Metallurgy: Used for purifying metals and sintering powdered metals into solid forms.
- Semiconductor Alloy Processing: Critical in the production of semiconductor materials, ensuring precise alloy compositions.
-
Working Principle:
- The furnace heats the material above its recrystallization temperature and maintains this temperature for a specific duration. This allows the material's atomic structure to redistribute, eliminating dislocations and stresses.
- After the heating phase, the material is cooled at a controlled rate, allowing recrystallization to occur, which results in improved material properties.
-
Advantages:
- Versatility: Suitable for a wide range of materials and processes, from metals to ceramics and semiconductors.
- Precision: Advanced temperature control and uniformity ensure high-quality results.
- Efficiency: The use of hydrogen as a protective atmosphere prevents oxidation, reducing material waste and improving process efficiency.
- Durability: Robust construction and high-quality components ensure long-term reliability.
-
Industries and Use Cases:
- Metallurgy: For annealing and purifying metals.
- Ceramics: For sintering and strengthening ceramic materials.
- Electronics: For semiconductor alloy processing and component manufacturing.
- Glass Manufacturing: For sealing and strengthening glass parts.
- Powder Metallurgy: For creating solid metal components from powdered metals.
In summary, the hydrogen bell-type annealing furnace is a highly advanced and versatile piece of equipment that plays a critical role in various industrial processes. Its ability to provide precise temperature control, coupled with the use of a hydrogen atmosphere, makes it indispensable for applications requiring high-quality material properties.
Summary Table:
Key Features | Details |
---|---|
Temperature Range | Up to 1600℃ with precision control (±1℃) |
Temperature Uniformity | ±3℃ to ±10℃ |
Control Systems | Automatic and manual options with piecewise program temperature controller |
Heating Mechanism | Magnetic transformer for efficient heating |
Additional Features | Paperless recorder, hydraulic system, stainless steel table plate |
Applications | Ceramic sintering, metallization, glass sealing, metal annealing, and more |
Industries | Metallurgy, ceramics, electronics, glass manufacturing, powder metallurgy |
Discover how a hydrogen bell-type annealing furnace can optimize your material processing—contact us today for expert advice!