Induction furnaces are versatile and widely used in various industries for heating, melting, refining, and processing metals. They are particularly valued for their efficiency, precision, and ability to handle a wide range of materials, from precious metals like gold and silver to industrial metals like steel and aluminum. These furnaces are essential in industries such as forging, foundry, heat treatment, and investment casting, where they perform tasks like metal melting, alloy manufacturing, and heat treatment processes such as quenching and tempering. Additionally, induction furnaces are used in specialized applications like shrink-fitting, brazing, and annealing, making them indispensable in modern metalworking and manufacturing.
Key Points Explained:
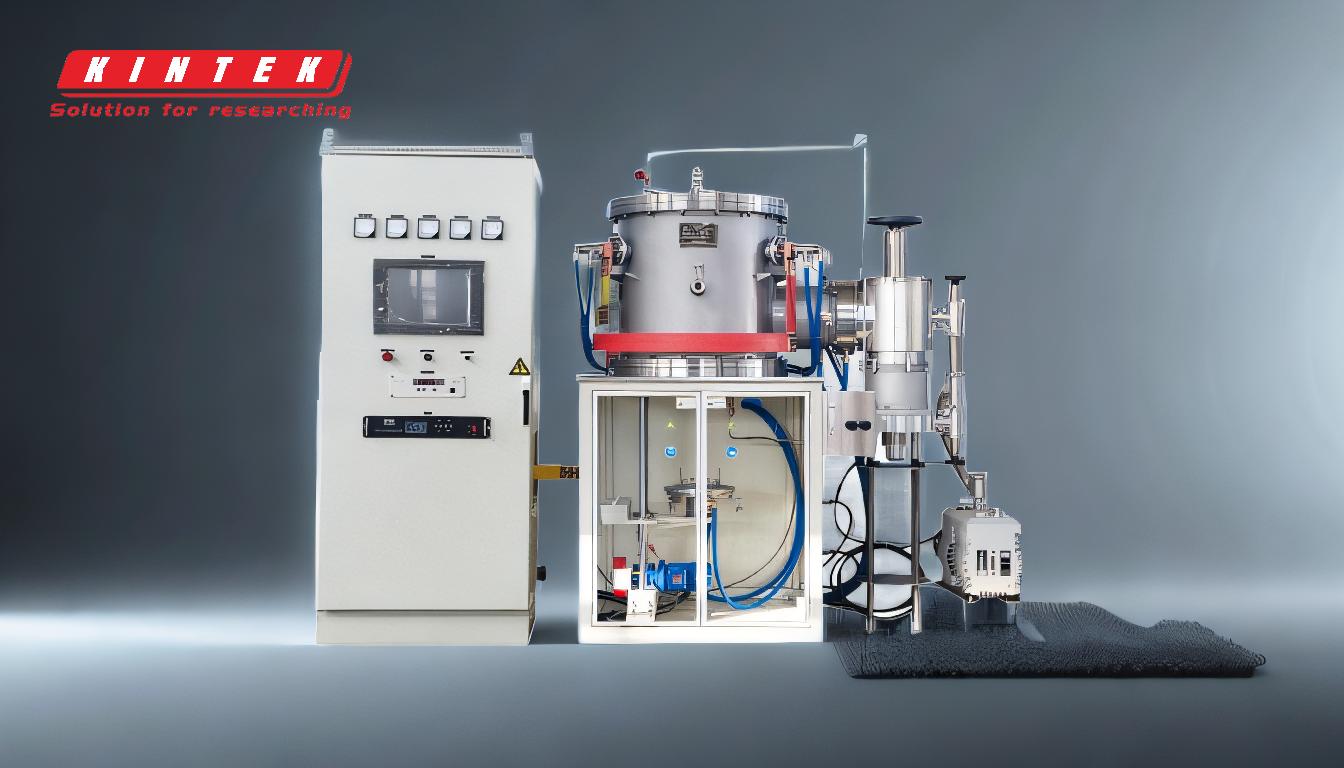
-
Metal Melting and Refining:
- Induction furnaces are extensively used for melting and refining metals, including precious metals like gold, silver, and platinum. They are also used for melting non-ferrous metals such as copper and aluminum.
- These furnaces are capable of processing raw materials and recycling waste metals, making them environmentally friendly and cost-effective.
-
Forging Industry:
- In the forging industry, induction furnaces are used to heat metal blanks before they are shaped into final products. This pre-heating process ensures that the metal is malleable and easy to work with.
- The precise temperature control offered by induction furnaces is crucial for achieving the desired properties in the forged products.
-
Foundry Industry:
- Induction furnaces play a critical role in the foundry industry by remelting and purifying waste metals. This process is essential for producing high-quality castings.
- They are also used for melting various metal materials, which are then poured into molds to create castings for a wide range of applications.
-
Heat Treatment:
- Induction furnaces are widely used in the heat treatment industry for processes such as quenching and tempering. These processes are essential for improving the mechanical properties of metals, such as hardness and toughness.
- For example, steel bars are often quenched and tempered using induction furnaces to achieve the desired strength and durability.
-
Alloy Manufacturing:
- Induction furnaces are used in the production of alloys, ensuring optimal uniformity and flexibility. They are capable of melting and mixing different metals to create alloys with specific properties.
- This is particularly important in industries that require high-performance materials, such as aerospace and automotive manufacturing.
-
Investment Casting:
- Induction furnaces are used in investment casting, where wax models and metal alloys are melted to create complex and high-quality metal parts. This process is widely used in industries that require precision components, such as jewelry and medical devices.
-
Specialized Applications:
- Induction furnaces are also used in specialized applications such as shrink-fitting, annealing, and brazing. These processes are essential for assembling and repairing metal components.
- For example, shrink-fitting involves heating a metal part so that it expands and fits tightly onto another component, while annealing is used to soften metals for further processing.
-
Energy Efficiency:
- Induction furnaces are known for their energy efficiency, particularly in applications like aluminum melting. They minimize energy requirements, making them a cost-effective solution for large-scale industrial processes.
- The ability to precisely control the heating process also reduces energy waste, further enhancing their efficiency.
-
Versatility:
- The versatility of induction furnaces makes them suitable for a wide range of applications across different industries. From melting and refining metals to heat treatment and alloy manufacturing, these furnaces are indispensable in modern manufacturing.
- Their ability to handle various metals and processes with high precision and efficiency makes them a valuable asset in any metalworking or manufacturing facility.
In summary, induction furnaces are essential tools in the metalworking and manufacturing industries, offering a wide range of applications from melting and refining metals to heat treatment and alloy manufacturing. Their efficiency, precision, and versatility make them indispensable for producing high-quality metal products and components.
Summary Table:
Application | Key Benefits |
---|---|
Metal Melting and Refining | Processes precious and non-ferrous metals; eco-friendly and cost-effective. |
Forging Industry | Pre-heats metal blanks for shaping; ensures precise temperature control. |
Foundry Industry | Remelts and purifies waste metals; produces high-quality castings. |
Heat Treatment | Enhances metal properties through quenching and tempering. |
Alloy Manufacturing | Creates uniform alloys for high-performance industries like aerospace. |
Investment Casting | Melts wax models and alloys for precision components. |
Specialized Applications | Used in shrink-fitting, annealing, and brazing for assembly and repair. |
Energy Efficiency | Minimizes energy use, especially in aluminum melting. |
Versatility | Handles diverse metals and processes with precision and efficiency. |
Transform your metalworking processes with induction furnaces—contact us today to learn more!