Induction heating is a highly efficient and precise method of heating conductive materials using electromagnetic induction. It involves passing an alternating current through a coil, which generates a changing magnetic field. When a conductive material, or workpiece, is placed within this field, eddy currents are induced, leading to resistive heating (Joule Heating Effect). This process is widely used in applications such as metal melting, forging, and surface hardening. High-frequency induction furnaces, often powered by advanced technologies like IGBT induction furnace, are particularly effective for melting metals and creating alloys due to their ability to achieve high temperatures quickly and with precise control.
Key Points Explained:
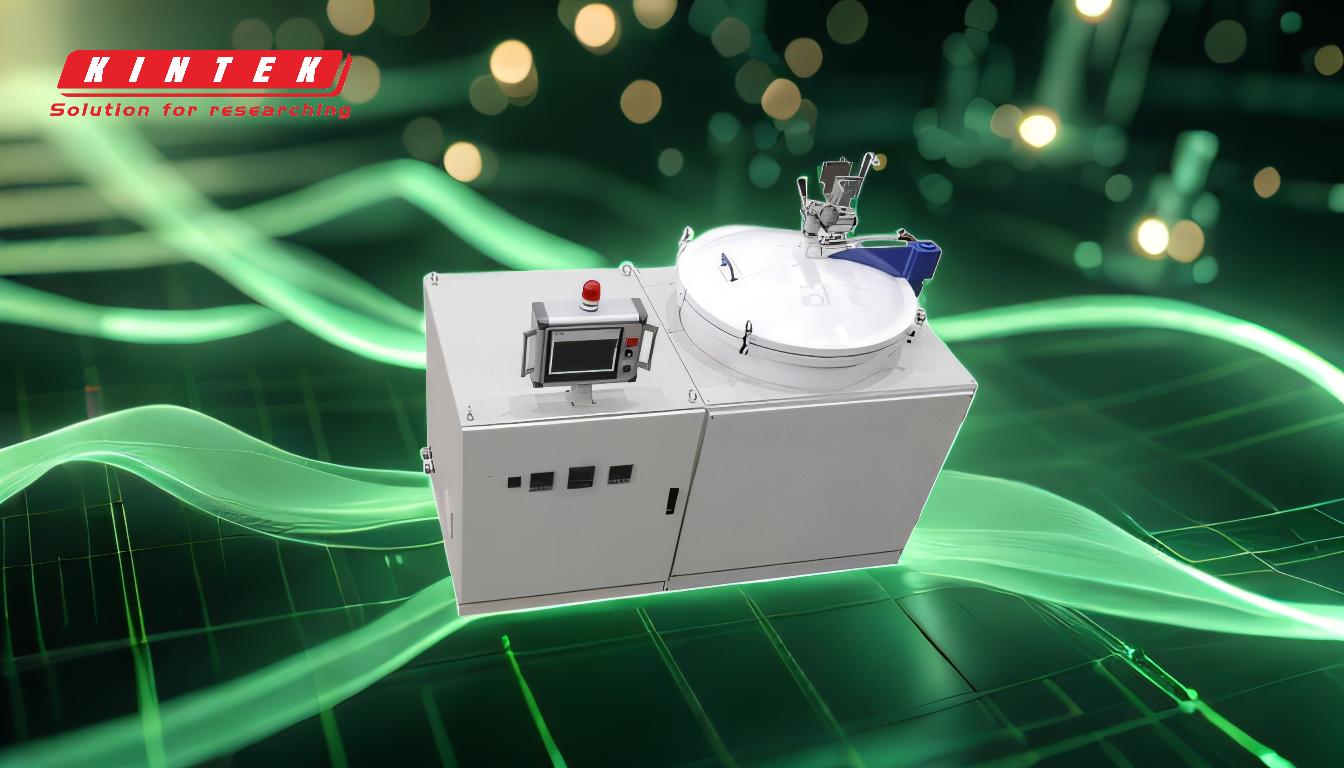
-
Principle of Induction Heating:
- Induction heating relies on electromagnetic induction to generate heat in conductive materials. An alternating current passes through a coil, creating a changing magnetic field. When a conductive workpiece is placed in this field, eddy currents are induced within the material. These currents encounter resistance, producing heat through the Joule Heating Effect. This method is contactless, efficient, and allows for localized heating.
-
Components of an Induction Heating System:
- Power Supply: Provides the alternating current required for induction. Modern systems often use IGBT induction furnace technology for higher efficiency and control.
- Induction Coil: The coil generates the magnetic field and is designed based on the application and workpiece geometry.
- Workpiece: The conductive material to be heated, which must be capable of supporting induced currents.
-
Applications of Induction Heating:
- Metal Melting: High-frequency induction furnaces are widely used in foundries to melt metals and create alloys. The process is fast, energy-efficient, and produces high-quality results.
- Surface Hardening: Induction heating is used to harden the surface of metal components, improving wear resistance while maintaining the core's toughness.
- Forging and Annealing: The precise control of heating makes it ideal for forging and annealing processes, where specific temperature profiles are required.
-
Advantages of Induction Heating:
- Efficiency: Induction heating is more energy-efficient than traditional methods like gas or resistance heating, as heat is generated directly within the workpiece.
- Precision: The process allows for localized and controlled heating, reducing the risk of damaging surrounding areas.
- Speed: Induction heating can achieve high temperatures rapidly, making it suitable for high-throughput applications.
- Clean and Safe: Since it is a contactless method, there is no contamination, and it eliminates the risks associated with open flames or hot surfaces.
-
High-Frequency Induction Furnaces:
- High-frequency induction furnaces are specialized systems designed for applications requiring rapid and intense heating, such as metal melting. These furnaces operate at frequencies ranging from a few kHz to several MHz, depending on the application. The use of IGBT induction furnace technology enhances their performance by providing better control over the heating process and improving energy efficiency.
-
Role of IGBT Technology in Induction Furnaces:
- IGBT (Insulated Gate Bipolar Transistor) technology is a key advancement in induction heating systems. It allows for precise control of the alternating current, enabling smoother operation and higher efficiency. IGBT-based systems are particularly advantageous in high-frequency induction furnaces, where they contribute to faster heating, reduced energy consumption, and improved reliability.
-
Comparison with Other Heating Methods:
- Unlike traditional heating methods, induction heating does not rely on direct contact or combustion, making it cleaner and more environmentally friendly. It also offers better temperature control and faster heating rates compared to resistance or convection heating.
By leveraging the principles of electromagnetic induction and advanced technologies like IGBT induction furnace, induction heating has become a cornerstone in modern industrial processes, offering unmatched efficiency, precision, and versatility.
Summary Table:
Aspect | Details |
---|---|
Principle | Electromagnetic induction generates heat via eddy currents in conductive materials. |
Key Components | Power supply, induction coil, and workpiece. |
Applications | Metal melting, surface hardening, forging, and annealing. |
Advantages | High efficiency, precision, speed, and clean operation. |
High-Frequency Furnace | Operates at kHz-MHz frequencies, ideal for rapid and intense heating. |
IGBT Technology | Enhances control, efficiency, and reliability in induction heating systems. |
Ready to optimize your industrial heating processes? Contact us today to learn more about induction heating solutions!