Injection molding is a manufacturing process used to produce large quantities of identical parts by injecting molten material into a mold. Once the material cools and solidifies, the mold opens, and the finished part is ejected. This method is highly efficient for mass production, as it allows for the creation of complex shapes with high precision and repeatability. Common materials used include plastics, metals, and glass, with plastics being the most prevalent due to their versatility and cost-effectiveness.
Key Points Explained:
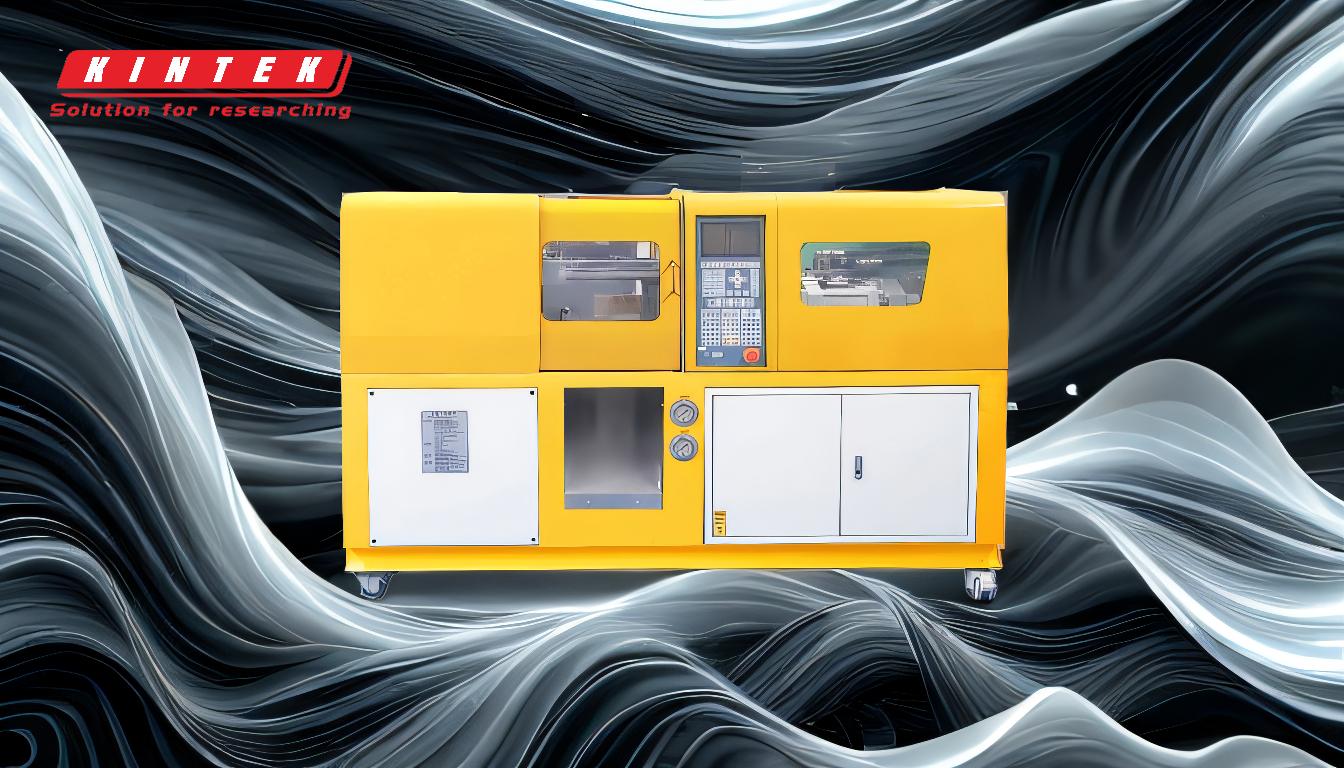
-
Definition of Injection Molding:
- Injection molding is a manufacturing technique where molten material is injected into a mold to create parts. The process is widely used for mass production due to its ability to produce large volumes of identical items quickly and efficiently.
-
How It Works:
- Material Preparation: Raw material, often in the form of pellets, is fed into the injection molding machine.
- Melting: The material is heated until it becomes molten.
- Injection: The molten material is injected into a mold under high pressure.
- Cooling: The material cools and solidifies within the mold, taking its shape.
- Ejection: Once solidified, the mold opens, and the finished part is ejected.
-
Materials Used:
- Plastics: The most common material due to its versatility, cost-effectiveness, and ease of molding. Examples include polyethylene, polypropylene, and polystyrene.
- Metals: Used in metal injection molding (MIM) for producing small, complex metal parts.
- Glass: Less common but used for specialized applications requiring high transparency or thermal resistance. Optical glass sheets are an example of such specialized materials.
-
Advantages of Injection Molding:
- High Efficiency: Capable of producing thousands of parts in a short time.
- Precision: Allows for the creation of complex and detailed shapes with high accuracy.
- Repeatability: Ensures each part is identical, which is crucial for mass production.
- Material Versatility: Can be used with a wide range of materials, each offering different properties.
-
Applications:
- Consumer Goods: Items like bottle caps, toys, and containers.
- Automotive: Components such as dashboards, bumpers, and interior trim.
- Medical: Syringes, surgical instruments, and diagnostic equipment.
- Electronics: Housings for devices, connectors, and insulators.
-
Considerations for Purchasers:
- Mold Design: The initial cost of mold design and fabrication can be high, but it is amortized over large production runs. Press mold designs are often considered for specific applications.
- Material Selection: Choosing the right material is crucial for the part's performance and durability.
- Production Volume: Injection molding is most cost-effective for high-volume production. For low-volume or custom parts, other manufacturing methods may be more suitable.
- Quality Control: Ensuring consistent quality requires regular maintenance of the molding machine and molds, as well as rigorous inspection of the finished parts.
Injection molding is a cornerstone of modern manufacturing, enabling the production of a vast array of products that we use daily. Its efficiency, precision, and versatility make it an indispensable process in industries ranging from consumer goods to medical devices.
Summary Table:
Aspect | Details |
---|---|
Definition | A manufacturing process for producing large quantities of identical parts. |
How It Works | Melts material, injects into a mold, cools, and ejects the finished part. |
Materials Used | Plastics (most common), metals, and glass. |
Advantages | High efficiency, precision, repeatability, and material versatility. |
Applications | Consumer goods, automotive, medical, and electronics industries. |
Considerations | Mold design, material selection, production volume, and quality control. |
Discover how injection molding can revolutionize your production process—contact us today for expert guidance!