Isostatic pressing of ceramics is a manufacturing process that involves applying uniform pressure from all directions to compact powdered materials into a dense, cohesive form. This technique is particularly useful for producing complex shapes and large parts that are difficult to achieve with traditional uniaxial pressing methods. Cold isostatic pressing (CIP) is performed at room temperature or slightly elevated temperatures, using a liquid medium to apply pressure, while hot isostatic pressing (HIP) involves higher temperatures for densification. The process is widely used in industries requiring high-performance materials with superior structural integrity, such as wear-resistant tools, solid-state batteries, and intricate ceramic components.
Key Points Explained:
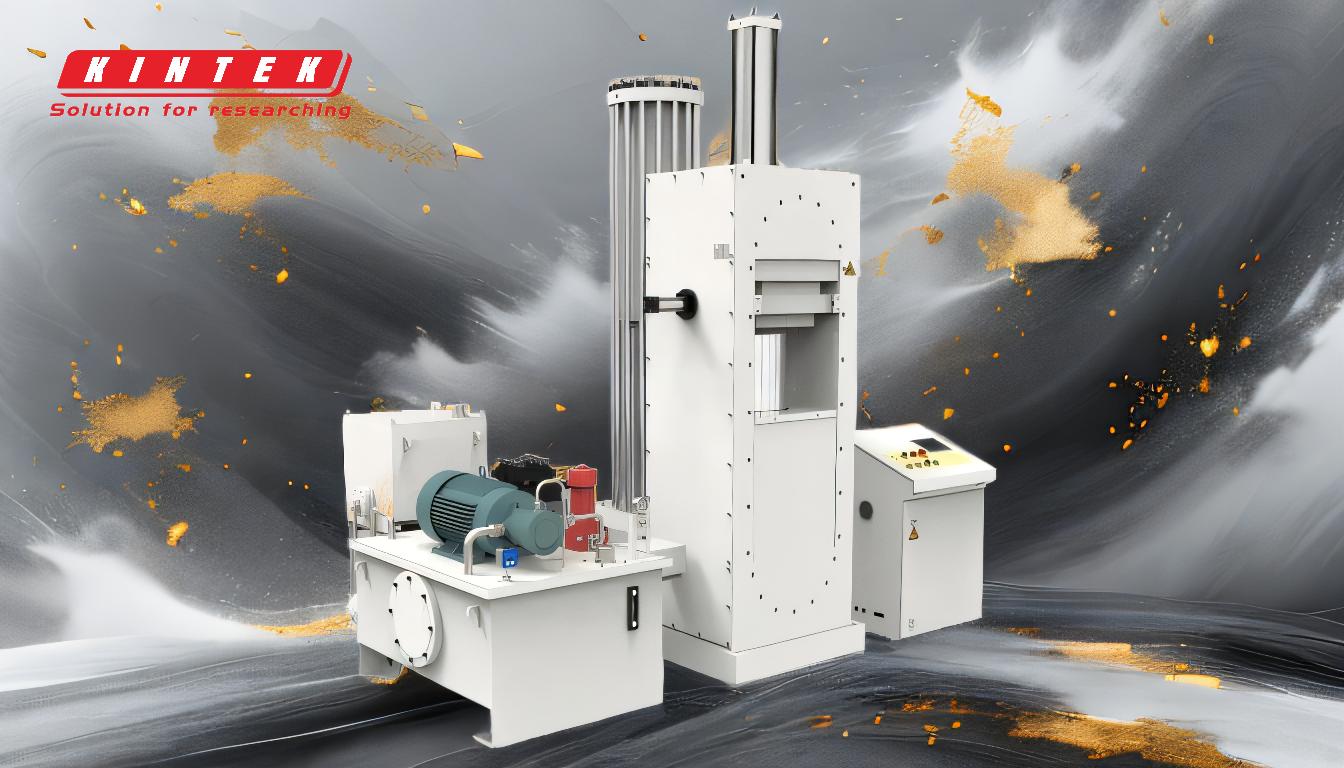
-
Definition and Purpose of Isostatic Pressing:
- Isostatic pressing is a method that applies uniform hydrostatic pressure to powdered materials, ensuring even compaction regardless of the shape or size of the part. This process is ideal for creating high-density, high-performance materials with complex geometries that are challenging to produce using conventional methods.
- It is commonly used for ceramics, metals, and composites, particularly in applications requiring superior mechanical properties like hardness, wear resistance, and thermal stability.
-
Cold Isostatic Pressing (CIP):
- CIP is performed at room temperature or slightly higher temperatures (below 93°C) using a liquid medium such as water, oil, or glycol mixtures. This method is suitable for forming "raw" parts that have sufficient strength for handling and further processing.
- A cold isostatic pressing machine is used to apply pressure uniformly, enabling the production of large or intricate parts that do not require high precision in their sintered state.
-
Process Steps:
- Loading Powder: The powdered material is loaded into a flexible mold, typically made of polyurethane or similar materials.
- Sealing the Mold: The mold is sealed to prevent leakage of the powder or the pressurizing fluid.
- Applying Pressure: The sealed mold is placed in a pressure vessel, where a liquid medium applies uniform hydrostatic pressure.
- Releasing Pressure: After compaction, the pressure is released, and the compacted powder body is removed from the mold.
-
Wet-Bag vs. Dry-Bag Techniques:
- Wet-Bag Technique: The flexible mold containing the powder is submerged in a pressure vessel filled with pressurizing fluid. This method is suitable for small-scale or custom production.
- Dry-Bag Technique: The flexible mold is fixed within the pressure vessel, allowing for faster and more efficient production cycles. This technique is often used in industrial applications.
-
Advantages of Isostatic Pressing:
- Uniform Density: The uniform pressure ensures consistent density throughout the part, reducing defects and improving structural integrity.
- Complex Shapes: The process can produce intricate and complex shapes that are difficult to achieve with other methods.
- Improved Mechanical Properties: The resulting materials exhibit enhanced hardness, wear resistance, and thermal stability.
-
Applications:
- Wear and Metal Forming Tools: CIP is used to manufacture tools with high wear resistance and durability.
- Solid-State Batteries: Isostatic pressing is employed to create thin, dense solid electrolyte layers and integrate them into tri-layer systems for solid-state battery applications.
- Large or Complex Parts: The process is ideal for producing large components or parts with intricate geometries that cannot be formed using uniaxial pressing.
-
Comparison with Hot Isostatic Pressing (HIP):
- While CIP is performed at lower temperatures, HIP involves higher temperatures and is primarily used for densification treatment of castings and other metal products. HIP is more suitable for achieving near-net-shape components with minimal porosity.
-
Equipment and Control:
- Modern cold isostatic pressing machine systems offer advanced control features, such as adjustable pressure increasing speed, pressure holding time, and multi-pressure section processes. These machines also support pressure curve visualization, data storage, and export for quality control and process optimization.
By leveraging the principles of isostatic pressing, manufacturers can produce high-quality ceramic and metal components with exceptional performance characteristics, making it a vital process in advanced material manufacturing.
Summary Table:
Aspect | Details |
---|---|
Process | Applies uniform hydrostatic pressure to compact powdered materials. |
Types | Cold Isostatic Pressing (CIP) and Hot Isostatic Pressing (HIP). |
Key Benefits | Uniform density, complex shapes, improved mechanical properties. |
Applications | Wear-resistant tools, solid-state batteries, large/complex ceramic parts. |
Techniques | Wet-Bag (custom production) and Dry-Bag (industrial production). |
Equipment | Advanced CIP machines with adjustable pressure and data visualization. |
Discover how isostatic pressing can transform your material manufacturing—contact our experts today!