Liquid-phase sintering (LPS) and solid-state sintering (SSS) are two distinct methods used in the densification of ceramic and metal powders. While both aim to achieve a dense, solid material, they differ significantly in their mechanisms, applications, and the types of materials they are suited for. Liquid-phase sintering involves the addition of a low-melting-point additive that forms a liquid phase during sintering, facilitating particle rearrangement and bonding through capillary forces. This method is particularly useful for materials with high melting points or those that are difficult to densify. In contrast, solid-state sintering relies solely on diffusion mechanisms to transport material and achieve densification, making it suitable for materials like zirconia and alumina that can densify without the need for a liquid phase.
Key Points Explained:
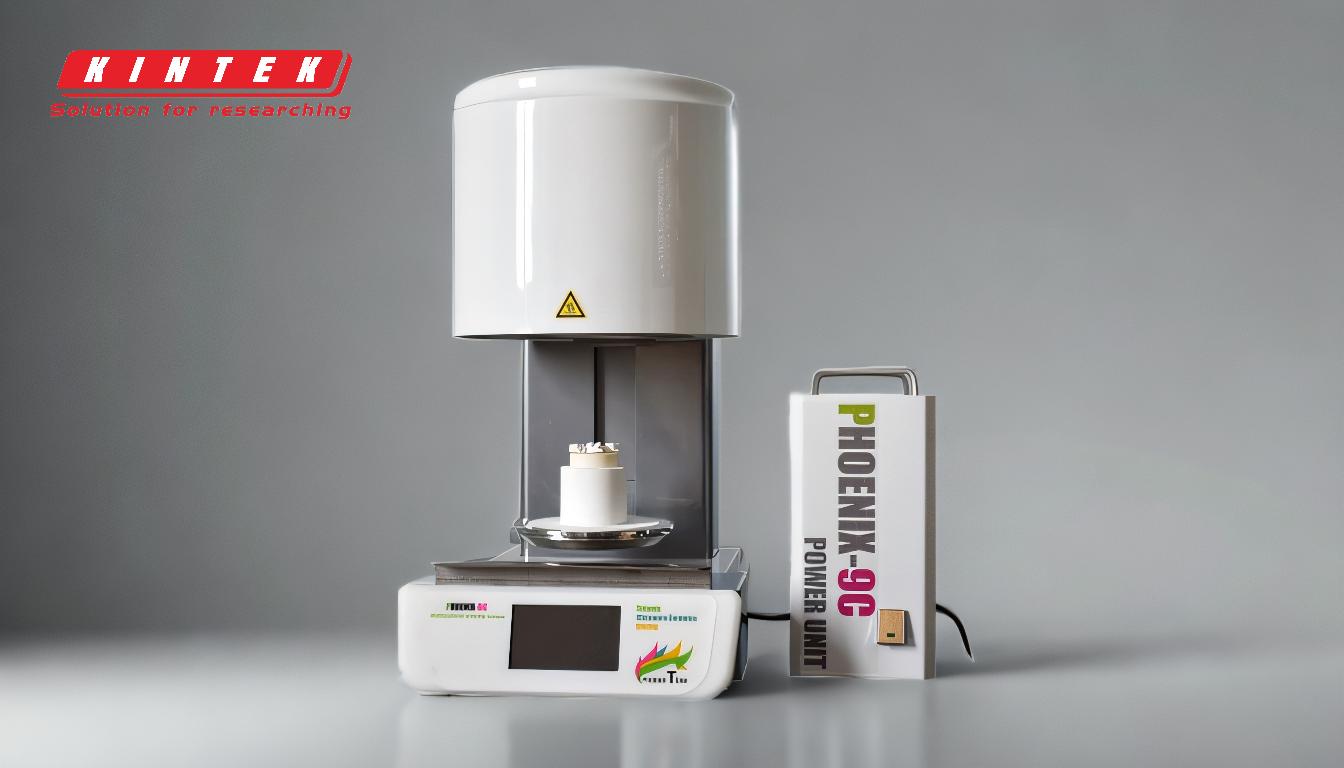
-
Mechanism of Sintering:
- Solid-State Sintering: In SSS, the densification process occurs entirely in the solid state. Material transport is driven by diffusion, where atoms move from areas of high concentration (e.g., grain boundaries) to areas of low concentration (e.g., pores). This process typically requires high temperatures but does not involve any liquid phase.
- Liquid-Phase Sintering: LPS involves the introduction of a liquid phase during sintering. The liquid forms from a low-melting-point additive that melts at the sintering temperature. This liquid facilitates particle rearrangement through capillary forces, leading to faster densification and lower sintering temperatures compared to SSS.
-
Materials and Applications:
- Solid-State Sintering: SSS is commonly used for ceramics like zirconia and alumina, which have relatively low diffusion rates but can still densify effectively through solid-state diffusion. These materials are often used in applications requiring high mechanical strength and thermal stability.
- Liquid-Phase Sintering: LPS is employed for harder-to-densify ceramics such as silicon nitride and silicon carbide. These materials have high melting points and are difficult to sinter using only solid-state diffusion. The addition of a liquid phase allows for better densification and is particularly useful in applications where enhanced mechanical properties or complex shapes are required.
-
Temperature Requirements:
- Solid-State Sintering: SSS typically requires higher temperatures to achieve sufficient diffusion rates for densification. The absence of a liquid phase means that the material must rely solely on thermal energy to drive atomic movement.
- Liquid-Phase Sintering: LPS can achieve densification at lower temperatures due to the presence of the liquid phase, which enhances particle mobility and rearrangement. This is especially beneficial for materials with high melting points, as it reduces the energy required for sintering.
-
Densification Rate:
- Solid-State Sintering: The densification rate in SSS is generally slower because it relies on solid-state diffusion, which is a slower process compared to the capillary-driven rearrangement in LPS.
- Liquid-Phase Sintering: LPS typically results in faster densification due to the rapid rearrangement of particles facilitated by the liquid phase. This can lead to shorter processing times and improved efficiency in manufacturing.
-
Microstructural Development:
- Solid-State Sintering: In SSS, the microstructure develops through grain growth and pore elimination, driven by diffusion. The resulting material often has a more uniform grain structure but may contain residual porosity if the sintering conditions are not optimal.
- Liquid-Phase Sintering: LPS can lead to a more complex microstructure, with the liquid phase often forming a secondary phase at grain boundaries. This can enhance certain properties, such as toughness, but may also introduce challenges in controlling the final microstructure.
-
Advantages and Limitations:
- Solid-State Sintering: SSS is advantageous for materials that can densify effectively through diffusion, offering a simpler process without the need for additives. However, it may not be suitable for materials with very high melting points or those that are difficult to densify.
- Liquid-Phase Sintering: LPS is advantageous for densifying challenging materials and achieving faster densification rates. However, it requires careful selection of the liquid-forming additive and may result in a more complex microstructure that needs to be controlled.
In summary, the choice between liquid-phase sintering and solid-state sintering depends on the material properties, desired densification rate, and the specific application requirements. While SSS is suitable for materials like zirconia and alumina, LPS is essential for harder-to-densify ceramics like silicon nitride and silicon carbide, offering lower sintering temperatures and faster densification rates.
Summary Table:
Aspect | Solid-State Sintering (SSS) | Liquid-Phase Sintering (LPS) |
---|---|---|
Mechanism | Relies on solid-state diffusion for densification. | Uses a liquid phase to facilitate particle rearrangement and bonding. |
Materials | Suitable for zirconia, alumina, and other materials with low diffusion rates. | Ideal for silicon nitride, silicon carbide, and other hard-to-densify ceramics. |
Temperature | Requires higher temperatures for effective densification. | Achieves densification at lower temperatures due to the liquid phase. |
Densification Rate | Slower due to reliance on solid-state diffusion. | Faster due to capillary-driven particle rearrangement. |
Microstructure | Uniform grain structure, but may have residual porosity. | Complex microstructure with secondary phases at grain boundaries. |
Advantages | Simpler process, no additives required. | Faster densification, suitable for high-melting-point materials. |
Limitations | Not ideal for materials with very high melting points or difficult-to-densify ceramics. | Requires careful additive selection and may result in complex microstructures. |
Still unsure which sintering method is right for your materials? Contact our experts today for personalized advice!