Low Pressure Chemical Vapor Deposition (LPCVD) is a specialized thin-film deposition technique used in semiconductor and microelectronics manufacturing. It operates at low pressures (0.1–10 Torr) and moderate to high temperatures (200–800°C) to deposit uniform and high-quality thin films on substrates. LPCVD involves introducing reactant gases into a chamber through a precursor delivery system, where they undergo chemical reactions on the heated substrate surface. The by-products are removed using vacuum pumps. This method is widely used for applications such as resistors, capacitor dielectrics, MEMS (Micro-Electro-Mechanical Systems), and anti-reflective coatings due to its ability to produce highly conformal and precise films.
Key Points Explained:
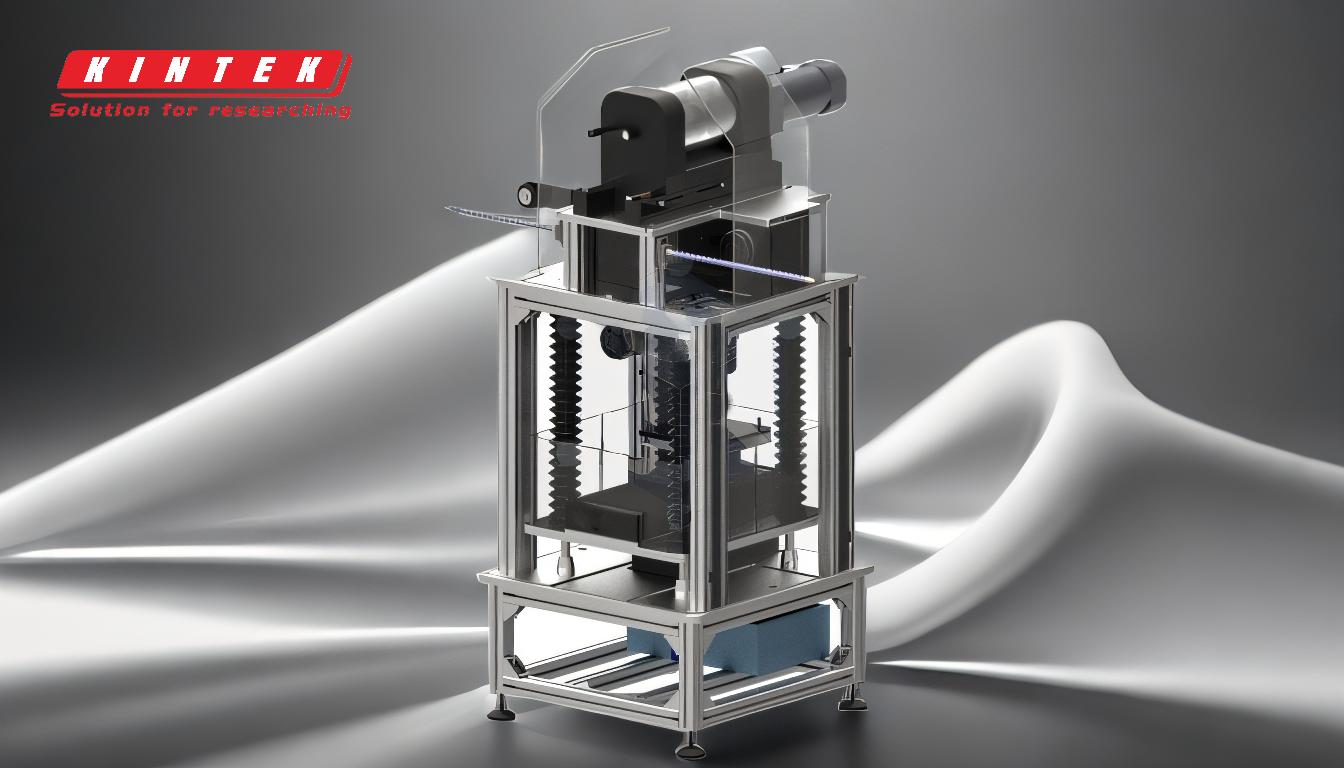
-
Definition and Process of LPCVD:
- LPCVD is a variant of Chemical Vapor Deposition (CVD) that operates at reduced pressures (0.1–10 Torr) and elevated temperatures (200–800°C).
- The process involves introducing reactant gases into a chamber, where they decompose or react on the heated substrate surface to form a thin film.
- By-products of the reaction are removed using vacuum pumps, ensuring a clean deposition environment.
-
Key Components of LPCVD:
- Precursor Delivery System: Reactant gases are introduced into the chamber through a specialized showerhead or delivery system.
- Heated Substrate: The substrate is heated to promote heterogeneous surface reactions, ensuring uniform film deposition.
- Vacuum System: A vacuum pump maintains low pressure and removes reaction by-products.
-
Advantages of LPCVD:
- Uniform Film Deposition: The low-pressure environment ensures a uniform gas flow, leading to highly conformal and consistent thin films.
- High-Quality Films: LPCVD produces films with excellent step coverage, making it ideal for complex geometries and microstructures.
- Versatility: It can deposit a wide range of materials, including silicon dioxide, silicon nitride, and polysilicon.
-
Applications of LPCVD:
- Resistors and Capacitors: LPCVD is used to deposit dielectric layers and conductive materials for resistors and capacitors.
- MEMS Fabrication: The technique is critical for creating microstructures in MEMS devices due to its precision and uniformity.
- Anti-Reflective Coatings: LPCVD is employed to deposit thin films that reduce reflection in optical and semiconductor devices.
-
Comparison with Other CVD Techniques:
- Atmospheric Pressure CVD (APCVD): Operates at atmospheric pressure, which can lead to less uniform films compared to LPCVD.
- Plasma-Enhanced CVD (PECVD): Uses plasma to lower the reaction temperature, but the films may have lower quality than those produced by LPCVD.
- LPCVD vs. PVD: Unlike Physical Vapor Deposition (PVD), which involves physical processes like sputtering, LPCVD relies on chemical reactions, enabling better conformality and material versatility.
-
Process Parameters:
- Pressure: Maintained at 0.1–10 Torr to ensure controlled gas flow and reaction kinetics.
- Temperature: Ranges from 200–800°C, depending on the material being deposited and the desired film properties.
- Gas Flow Rate: Precise control of reactant gas flow is essential for uniform deposition.
-
Challenges and Considerations:
- High Temperature: The elevated temperatures required for LPCVD can limit the types of substrates that can be used.
- Slow Deposition Rates: Compared to other CVD techniques, LPCVD may have slower deposition rates due to the low-pressure environment.
- Equipment Complexity: The need for vacuum systems and precise temperature control increases the complexity and cost of LPCVD equipment.
By understanding these key aspects, an equipment or consumable purchaser can evaluate the suitability of LPCVD for specific applications, considering factors such as film quality, uniformity, and process requirements.
Summary Table:
Aspect | Details |
---|---|
Definition | A CVD variant operating at low pressure (0.1–10 Torr) and high temperature (200–800°C). |
Key Components | Precursor delivery system, heated substrate, vacuum system. |
Advantages | Uniform film deposition, high-quality films, material versatility. |
Applications | Resistors, capacitors, MEMS fabrication, anti-reflective coatings. |
Process Parameters | Pressure: 0.1–10 Torr, Temperature: 200–800°C, precise gas flow control. |
Challenges | High temperature limits, slow deposition rates, complex equipment. |
Interested in LPCVD solutions for your manufacturing needs? Contact our experts today to learn more!