Low Pressure Plasma Enhanced Chemical Vapor Deposition (PECVD) is a specialized technique used to deposit thin films at relatively low temperatures by utilizing plasma to enhance chemical reactions. Unlike traditional Chemical Vapor Deposition (CVD), which often requires high temperatures, PECVD operates at lower pressures and temperatures, making it suitable for temperature-sensitive substrates. The process involves generating a low-temperature plasma to ionize and activate reaction gases, enabling the deposition of high-quality, dense, and uniform films. PECVD is widely used in industries such as nanoelectronics, power electronics, medicine, and space exploration due to its ability to produce films with excellent adhesion, uniformity, and purity.
Key Points Explained:
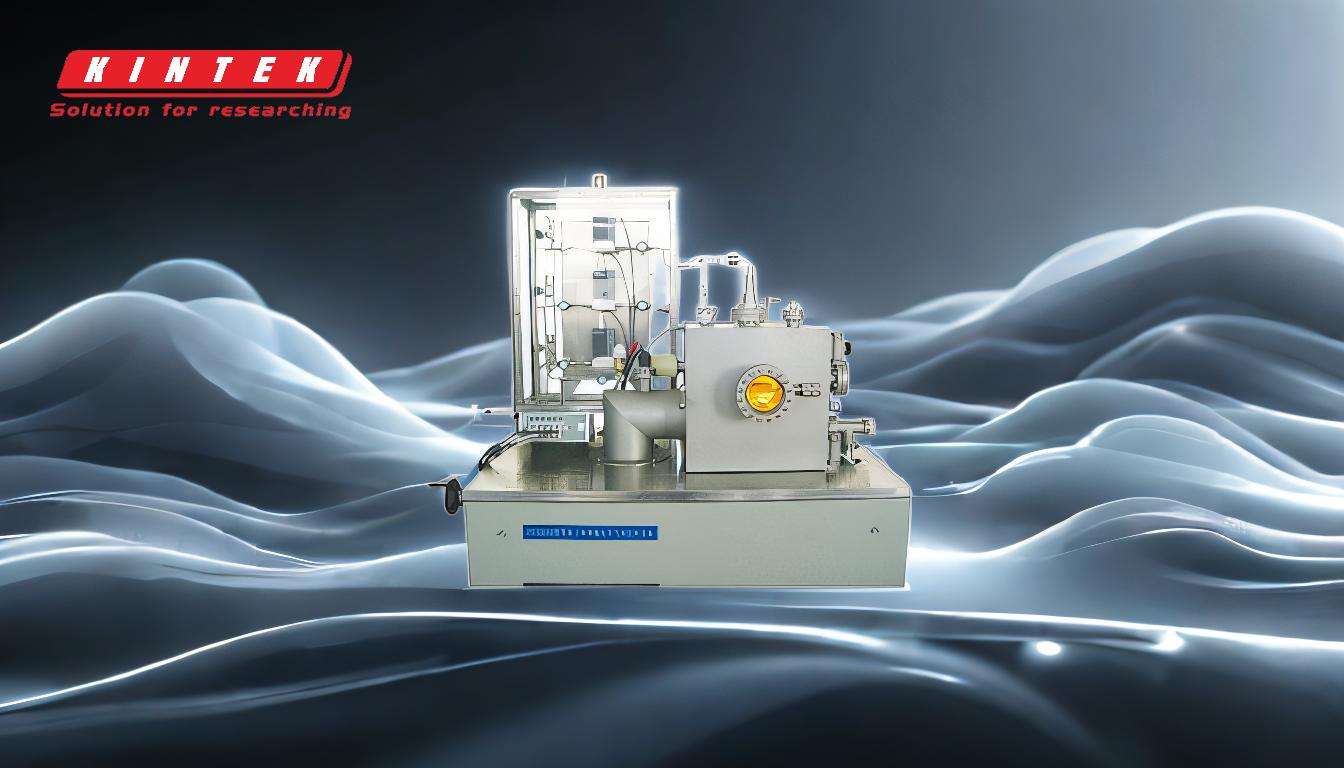
-
Definition and Mechanism of PECVD:
- PECVD is a variant of Chemical Vapor Deposition (CVD) that uses plasma to enhance chemical reactions.
- Plasma, a partially ionized gas with high free electron content (~50%), is generated by applying voltage between electrodes in a low-pressure environment.
- The energy from free electrons dissociates reactive gases, enabling the formation of solid films on the substrate at lower temperatures (as low as 200 °C).
-
Process Details:
- The substrate (e.g., a wafer) is placed on the cathode within a CVD reactor.
- Reactive gases (e.g., SiH4, C2H2, or B2H6) are introduced at low pressure.
- A glow discharge is generated to ionize the gas near the substrate surface, activating the reaction gases and improving surface activity.
- The activated gases react to form a thin film on the substrate.
-
Advantages of PECVD:
- Low Deposition Temperature: Suitable for temperature-sensitive materials and substrates.
- Minimal Impact on Substrate: Preserves the structural and physical properties of the substrate.
- High Film Quality: Produces dense, uniform films with strong adhesion and few defects (e.g., pinholes).
- Versatility: Can deposit a wide range of materials, including metals, inorganic compounds, and organic films.
- Energy Efficiency: Operates at lower temperatures, reducing energy consumption and costs.
-
Applications of PECVD:
- Nanoelectronics: Used to deposit silicon oxides, silicon nitride, amorphous silicon, and silicon oxynitrides for semiconductor devices.
- Power Electronics: Enables the fabrication of intermetallic oxide layers and hybrid structures.
- Medicine: Deposits biocompatible coatings for medical devices.
- Space and Ecology: Produces protective and functional coatings for space equipment and environmental applications.
- Isolation and Filling: Applied in shallow bath isolation, sidewall isolation, and metal-linked media isolation.
-
Comparison with Traditional CVD:
- Traditional CVD operates at atmospheric pressure and high temperatures, which can limit its use with sensitive materials.
- PECVD, by contrast, operates at low pressures and temperatures, making it more versatile and suitable for a broader range of applications.
-
Future Prospects:
- Ongoing research aims to further optimize PECVD for improved film purity, density, and throughput.
- The technique is continually evolving, with potential applications in emerging fields such as flexible electronics, energy storage, and advanced coatings.
In summary, Low Pressure Plasma Enhanced Chemical Vapor Deposition (PECVD) is a highly advanced and versatile deposition technique that leverages plasma to enable low-temperature, high-quality film deposition. Its ability to produce dense, uniform, and adherent films makes it indispensable in modern industries, particularly in nanotechnology and electronics.
Summary Table:
Aspect | Details |
---|---|
Definition | A CVD variant using plasma to enhance chemical reactions at low temperatures. |
Key Mechanism | Plasma ionizes reactive gases, enabling low-temperature film deposition. |
Advantages | Low temperature, high film quality, versatility, energy efficiency. |
Applications | Nanoelectronics, power electronics, medicine, space exploration. |
Comparison with CVD | Operates at lower pressures and temperatures, suitable for sensitive materials. |
Future Prospects | Optimization for purity, density, and emerging fields like flexible electronics. |
Interested in leveraging PECVD for your industry? Contact our experts today to learn more!