Magnetron plasma is a key component of the magnetron sputtering process, which is a widely used physical vapor deposition (PVD) technique. It involves the generation of a plasma in a low-pressure environment using a magnetic field to confine electrons, enhancing ionization and enabling efficient sputtering of target materials. This plasma is created by applying a high voltage between a cathode (target material) and an anode, ionizing a gas (usually argon) to form a plasma. The magnetic field traps electrons, increasing their path length and the likelihood of collisions with gas atoms, which sustains the plasma and improves sputtering efficiency. This process is crucial for depositing thin films with high precision and uniformity in various industrial and research applications.
Key Points Explained:
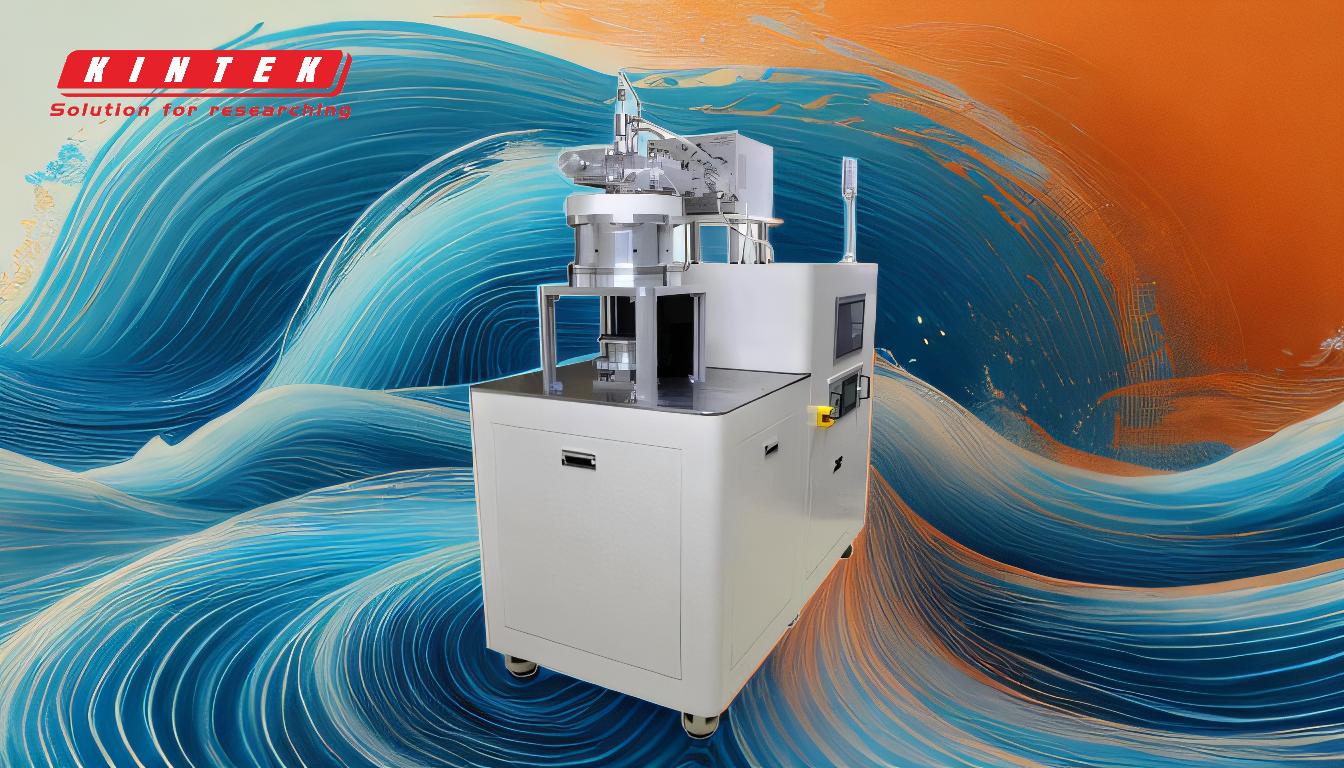
-
Definition of Magnetron Plasma:
- Magnetron plasma is a state of ionized gas created in a vacuum chamber during the magnetron sputtering process. It consists of free electrons, ions, and neutral atoms, which interact under the influence of a magnetic field. This plasma is essential for the sputtering process, as it enables the ejection of atoms from the target material to deposit thin films on a substrate.
-
Role of Magnetic Field:
- The magnetic field in magnetron sputtering is critical for confining electrons near the target surface. This confinement increases the ionization of the sputtering gas (typically argon) by prolonging the path length of electrons. As a result, the plasma density is enhanced, leading to more efficient sputtering and higher deposition rates.
-
Plasma Generation Process:
- Plasma is generated by applying a high voltage between the cathode (target material) and the anode. This voltage ionizes the sputtering gas, creating a plasma. The magnetic field ensures that the electrons spiral along the field lines, increasing their chances of colliding with gas atoms and sustaining the plasma.
-
Advantages of Magnetron Plasma:
- High Deposition Rates: The enhanced plasma density allows for faster sputtering and deposition of thin films.
- Low Temperature: The process can be performed at relatively low temperatures, making it suitable for temperature-sensitive substrates.
- Low Damage: The controlled plasma environment minimizes damage to the substrate, ensuring high-quality thin films.
-
Applications of Magnetron Plasma:
- Magnetron plasma is used in various industries, including:
- Semiconductors: For depositing thin films in the manufacturing of integrated circuits.
- Optics: For creating anti-reflective coatings and other optical films.
- Decorative Coatings: For applying durable and aesthetically pleasing finishes.
- Research: For developing advanced materials such as high-temperature superconducting films, ferroelectric films, and solar cells.
- Magnetron plasma is used in various industries, including:
-
Components of Magnetron Sputtering System:
- Target Material: The material to be sputtered, which forms the thin film.
- Vacuum Chamber: Maintains the low-pressure environment required for plasma generation.
- Magnetic Field Assembly: Generates the magnetic field to confine electrons.
- Power Supply: Provides the high voltage needed to ionize the gas and sustain the plasma.
- Substrate Holder: Holds the substrate where the thin film is deposited.
-
Plasma Characteristics:
- Electron Density: The number of free electrons in the plasma, which determines the ionization rate.
- Ion Energy: The energy of ions in the plasma, which affects the sputtering yield and film quality.
- Plasma Potential: The electric potential of the plasma, which influences the movement of charged particles.
-
Challenges and Considerations:
- Uniformity: Ensuring uniform deposition across the substrate can be challenging due to variations in plasma density.
- Target Erosion: The target material erodes over time, requiring periodic replacement or maintenance.
- Contamination: Impurities in the sputtering gas or target material can affect the quality of the deposited film.
-
Future Trends:
- Advanced Materials: Research is ongoing to develop new target materials and improve the properties of deposited films.
- Process Optimization: Efforts are being made to enhance plasma stability and deposition uniformity.
- Sustainability: Reducing energy consumption and waste in the magnetron sputtering process is a growing focus.
By understanding the principles and applications of magnetron plasma, equipment and consumable purchasers can make informed decisions about the tools and materials needed for their specific applications. This knowledge also helps in optimizing the process for better performance and cost-effectiveness.
Summary Table:
Key Aspect | Description |
---|---|
Definition | Ionized gas in a vacuum chamber, essential for sputtering target materials. |
Role of Magnetic Field | Confines electrons, increases ionization, and enhances plasma density. |
Advantages | High deposition rates, low temperature, and minimal substrate damage. |
Applications | Semiconductors, optics, decorative coatings, and advanced material research. |
Components | Target material, vacuum chamber, magnetic field assembly, power supply, substrate holder. |
Challenges | Uniformity, target erosion, and contamination. |
Future Trends | Advanced materials, process optimization, and sustainability. |
Discover how magnetron plasma can revolutionize your thin film processes—contact our experts today!