Magnetron sputtering is a highly efficient physical vapor deposition (PVD) technique used to deposit thin films onto substrates. It involves creating a plasma in a high-vacuum environment using an inert gas like argon. A high negative voltage is applied to a target material (cathode), ionizing the gas and creating positively charged ions. These ions collide with the target, ejecting atoms that then deposit onto a substrate. A magnetic field confines electrons near the target, increasing plasma density and deposition rates while protecting the substrate from ion bombardment. This method is widely used for producing high-quality coatings in industries such as electronics, optics, and automotive.
Key Points Explained:
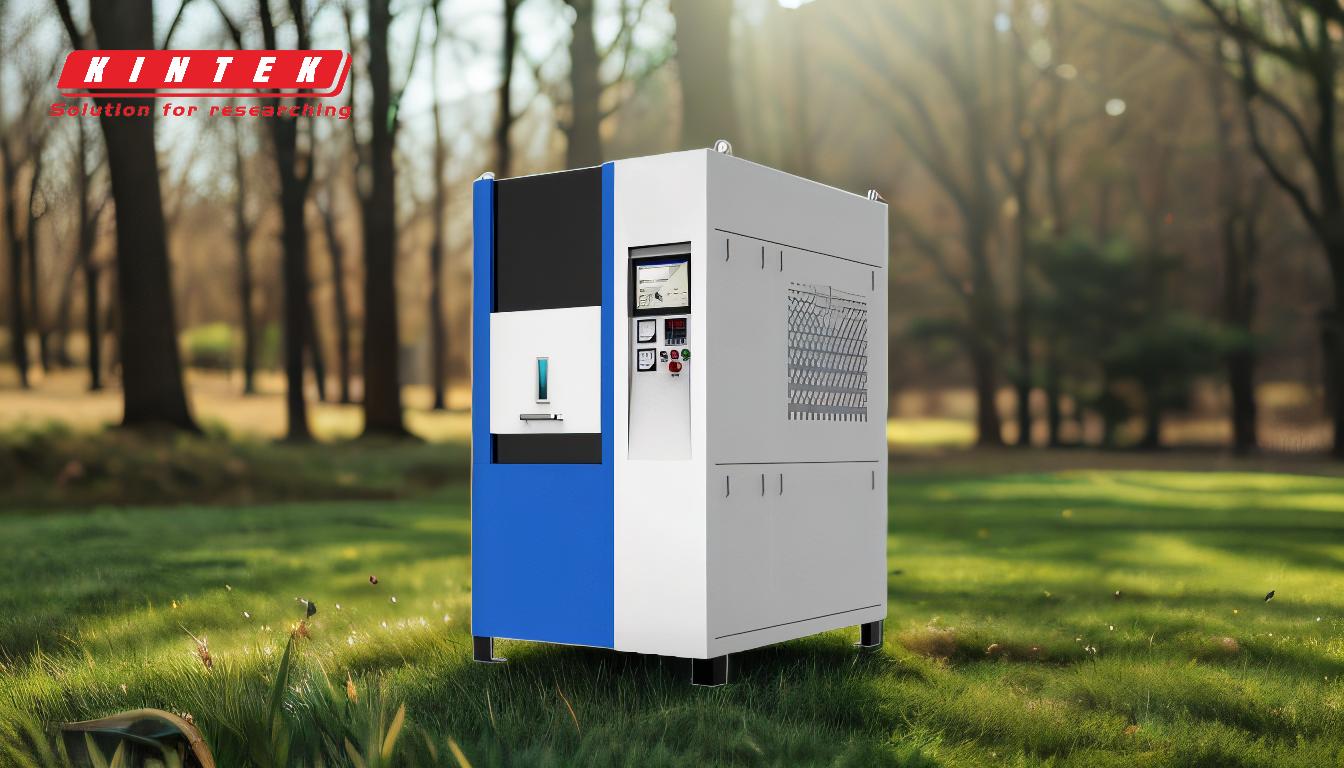
-
Basic Principle of Magnetron Sputtering:
- Magnetron sputtering is a physical vapor deposition (PVD) method.
- It uses a high vacuum chamber to create a low-pressure environment.
- An inert gas (typically argon) is introduced and ionized by applying a high negative voltage between the cathode (target) and anode.
- Positive argon ions collide with the negatively charged target, ejecting atoms from the target surface.
- These ejected atoms deposit onto a substrate, forming a thin film.
-
Role of the Magnetic Field:
- A strong magnetic field is applied near the target surface.
- This magnetic field confines electrons, increasing the density of the plasma near the target.
- The confined electrons enhance the ionization of the inert gas, leading to a higher deposition rate.
- The magnetic field also protects the substrate from excessive ion bombardment, reducing damage.
-
Plasma Generation and Ion Bombardment:
- The process begins with the creation of a plasma by ionizing the inert gas.
- Positive ions are accelerated toward the negatively charged target due to the applied voltage.
- When these high-energy ions strike the target, they transfer kinetic energy to the target atoms.
- If the energy is sufficient, target atoms are ejected (sputtered) and travel toward the substrate.
-
Deposition of Thin Films:
- The sputtered atoms move in a line-of-sight cosine distribution toward the substrate.
- Upon reaching the substrate, the atoms condense and form a thin film.
- The process allows for precise control over film thickness and composition, making it suitable for high-quality coatings.
-
Advantages of Magnetron Sputtering:
- High deposition rates due to the increased plasma density near the target.
- Ability to deposit a wide range of materials, including metals, alloys, and compounds.
- Produces uniform and dense coatings with excellent adhesion to the substrate.
- Suitable for large-scale industrial applications due to its scalability and efficiency.
-
Applications of Magnetron Sputtering:
- Electronics: Used for depositing thin films in semiconductors, solar cells, and displays.
- Optics: Applied in anti-reflective coatings, mirrors, and optical filters.
- Automotive: Used for wear-resistant and decorative coatings on automotive parts.
- Medical Devices: Deposits biocompatible coatings on implants and surgical tools.
-
Process Control and Parameters:
- Vacuum Level: A high vacuum is essential to minimize contamination and ensure efficient plasma generation.
- Gas Pressure: The pressure of the inert gas (argon) affects plasma density and sputtering efficiency.
- Magnetic Field Strength: Determines the confinement of electrons and plasma density near the target.
- Power Supply: The applied voltage and current influence the energy of the ions and the sputtering rate.
-
Challenges and Considerations:
- Target Erosion: Continuous ion bombardment can lead to target wear, requiring periodic replacement.
- Substrate Heating: Ion bombardment can cause substrate heating, which may affect temperature-sensitive materials.
- Uniformity: Achieving uniform film thickness across large or complex substrates can be challenging.
By understanding these key points, equipment and consumable purchasers can better evaluate the suitability of magnetron sputtering for their specific applications and make informed decisions about the necessary equipment and materials.
Summary Table:
Aspect | Details |
---|---|
Principle | Physical vapor deposition (PVD) using a high-vacuum environment and argon gas. |
Key Components | Target (cathode), inert gas, magnetic field, and power supply. |
Advantages | High deposition rates, uniform coatings, and excellent adhesion. |
Applications | Electronics, optics, automotive, and medical devices. |
Challenges | Target erosion, substrate heating, and uniformity issues. |
Ready to enhance your coating processes with magnetron sputtering? Contact our experts today for tailored solutions!