Maintenance in a laboratory context refers to the systematic process of ensuring that equipment, facilities, and consumables are in optimal working condition to support accurate and reliable scientific research. It involves regular inspections, cleaning, calibration, and repairs to prevent equipment failure, contamination, or deviations in experimental results. Proper laboratory maintenance also includes adhering to safety protocols, managing inventory, and ensuring compliance with regulatory standards. To maintain a laboratory effectively, one must establish a maintenance schedule, train personnel, document procedures, and prioritize preventive measures over reactive fixes. This approach minimizes downtime, extends equipment lifespan, and ensures a safe and efficient working environment.
Key Points Explained:
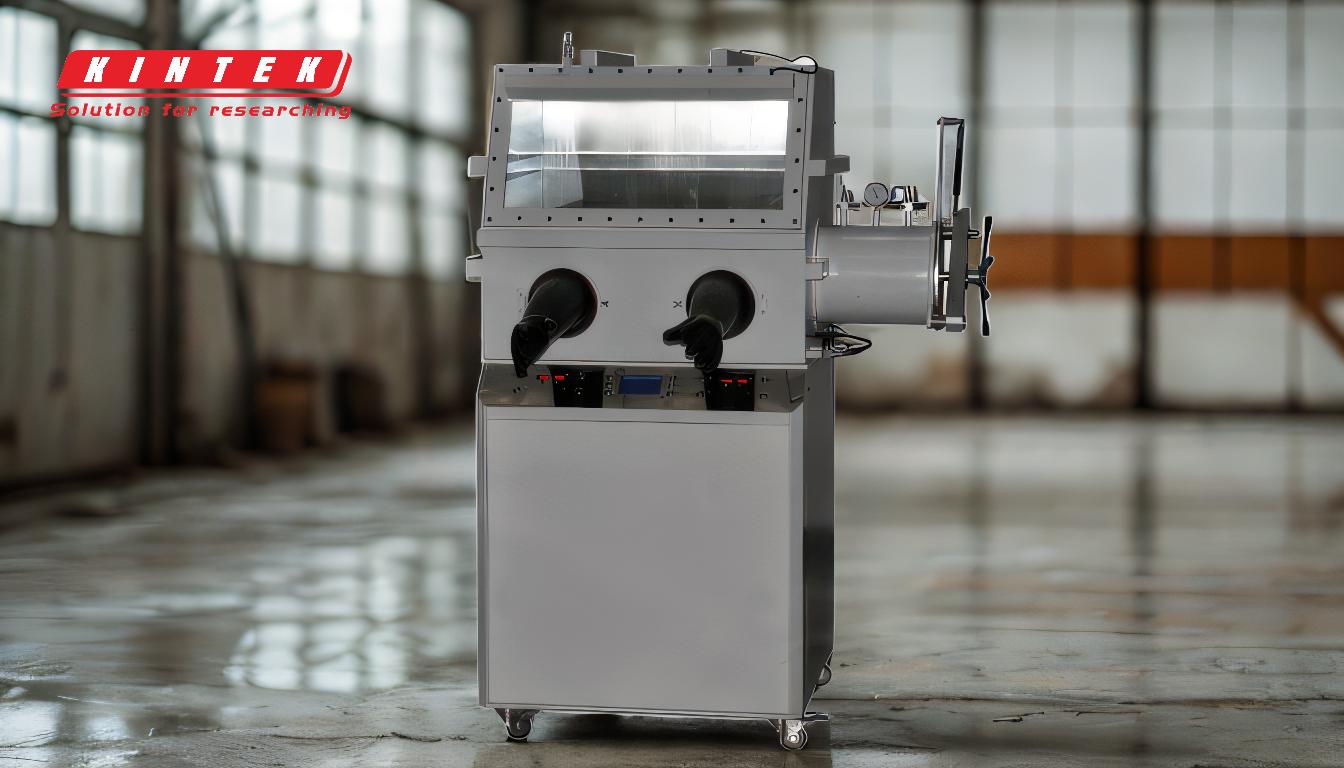
-
Definition of Laboratory Maintenance
- Laboratory maintenance encompasses all activities aimed at preserving the functionality, accuracy, and safety of laboratory equipment, facilities, and consumables.
- It includes preventive measures (e.g., regular cleaning and calibration) and corrective actions (e.g., repairs and replacements) to avoid disruptions in research activities.
-
Importance of Laboratory Maintenance
- Ensures the accuracy and reliability of experimental results by maintaining equipment in optimal condition.
- Reduces the risk of contamination, equipment failure, and accidents, thereby enhancing safety.
- Extends the lifespan of expensive laboratory equipment, saving costs in the long run.
- Complies with regulatory and accreditation standards, which often require documented maintenance procedures.
-
Types of Maintenance in Laboratories
- Preventive Maintenance (PM): Regular, scheduled tasks such as cleaning, calibration, and inspections to prevent equipment failure.
- Corrective Maintenance: Repairs or replacements performed after a malfunction or breakdown.
- Predictive Maintenance: Using data and monitoring tools to predict when maintenance is needed before a failure occurs.
-
Steps to Maintain a Laboratory
- Develop a Maintenance Schedule: Create a detailed plan outlining when and how each piece of equipment should be maintained.
- Train Personnel: Ensure all laboratory staff are trained in proper maintenance procedures and safety protocols.
- Document Procedures: Keep detailed records of maintenance activities, including dates, tasks performed, and any issues identified.
- Monitor Equipment Performance: Regularly check equipment for signs of wear or malfunction and address issues promptly.
- Manage Inventory: Keep track of consumables and spare parts to avoid shortages that could disrupt operations.
-
Common Maintenance Tasks
- Cleaning: Regularly clean equipment, work surfaces, and storage areas to prevent contamination.
- Calibration: Ensure instruments like pipettes, balances, and spectrophotometers are calibrated to maintain accuracy.
- Lubrication: Apply lubricants to moving parts of equipment to reduce wear and tear.
- Inspection: Check for signs of damage, leaks, or unusual noises that could indicate a problem.
-
Challenges in Laboratory Maintenance
- Resource Constraints: Limited budgets or personnel can make it difficult to perform regular maintenance.
- Complex Equipment: Advanced instruments may require specialized knowledge or external service providers for maintenance.
- Compliance Requirements: Keeping up with regulatory standards and documentation can be time-consuming.
-
Best Practices for Effective Maintenance
- Prioritize preventive maintenance to avoid costly repairs and downtime.
- Use a centralized system (e.g., a laboratory information management system or maintenance software) to track tasks and schedules.
- Collaborate with equipment manufacturers or service providers for specialized maintenance needs.
- Regularly review and update maintenance procedures to adapt to new equipment or changing laboratory needs.
-
Safety Considerations
- Always follow safety protocols when performing maintenance, such as wearing personal protective equipment (PPE) and de-energizing equipment before servicing.
- Dispose of hazardous materials (e.g., chemicals or biological waste) properly to prevent contamination or injury.
- Ensure emergency equipment (e.g., fire extinguishers, eyewash stations) is functional and accessible.
By implementing a structured maintenance program, laboratories can ensure operational efficiency, data integrity, and a safe working environment for all personnel.
Summary Table:
Aspect | Details |
---|---|
Definition | Preserving functionality, accuracy, and safety of lab equipment and facilities. |
Importance | Ensures reliable results, reduces risks, extends equipment life, and complies with regulations. |
Types of Maintenance | Preventive, Corrective, and Predictive maintenance. |
Key Steps | Develop schedules, train personnel, document procedures, monitor equipment, and manage inventory. |
Common Tasks | Cleaning, calibration, lubrication, and inspection. |
Challenges | Resource constraints, complex equipment, and compliance requirements. |
Best Practices | Prioritize preventive maintenance, use centralized systems, and collaborate with experts. |
Safety Considerations | Follow safety protocols, dispose of hazardous materials properly, and ensure emergency equipment is functional. |
Optimize your lab's performance and safety—contact us today to learn more about effective maintenance strategies!