Physical vapor deposition (PVD) is a sophisticated process used to deposit thin films of material onto a substrate. This process involves the physical transformation of a solid material into a vapor, which is then condensed onto the surface of a substrate to form a thin, durable coating. PVD is widely used in various industries to enhance the properties of materials, such as increasing hardness, durability, and resistance to chemicals and oxidation. The process typically occurs in a vacuum or low-pressure environment, often involving plasma activation, to ensure precise and high-quality coating deposition.
Key Points Explained:
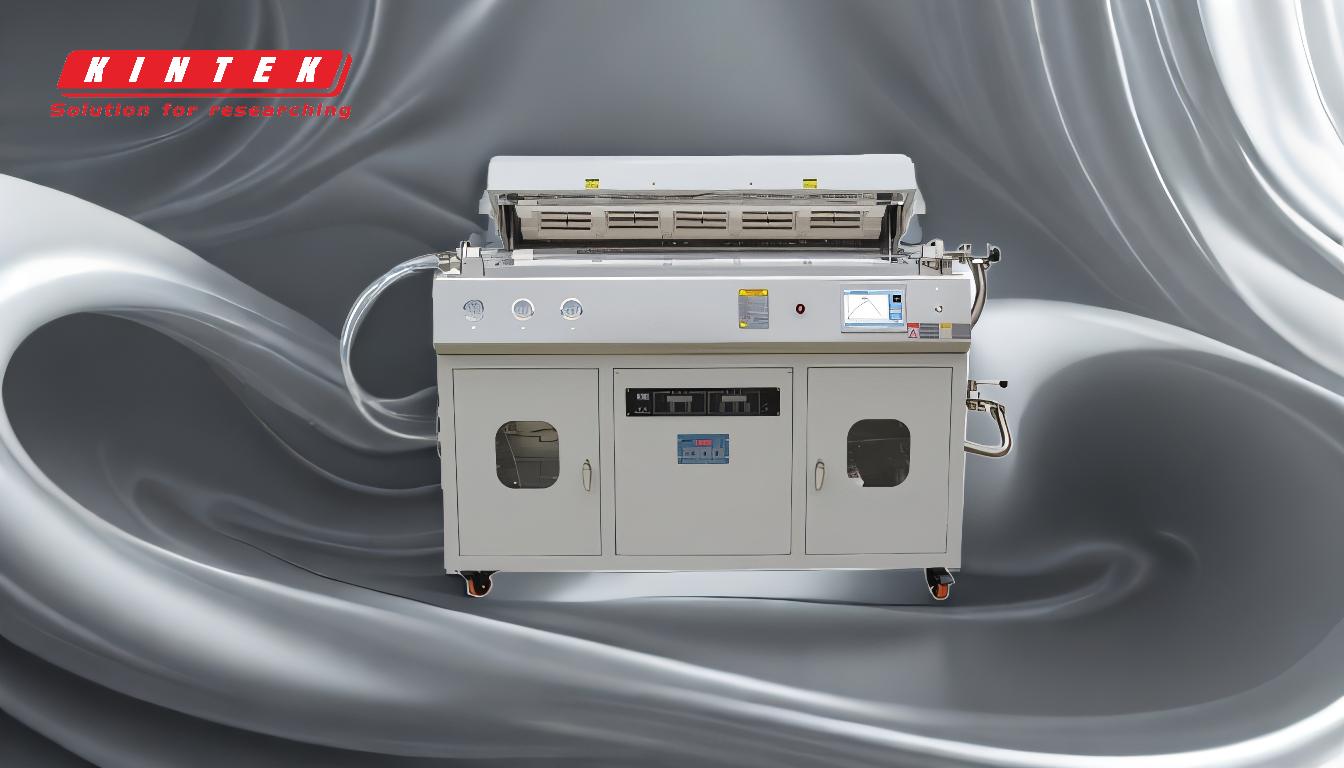
-
Definition of PVD:
- Physical Transformation: PVD involves the physical transformation of a solid material into a vapor. This is achieved through processes like evaporation or sputtering, where the material is either heated until it vaporizes or bombarded with ions to eject atoms from its surface.
- Condensation and Deposition: The vaporized material is then transported through a vacuum or low-pressure environment and condenses onto the surface of a substrate, forming a thin film.
-
Process Environment:
- Vacuum or Low-Pressure Conditions: PVD processes are typically carried out in a vacuum or low-pressure environment. This minimizes contamination and allows for precise control over the deposition process.
- Plasma Activation: In some PVD processes, plasma is used to activate the vaporized material, enhancing the deposition process and improving the quality of the coating.
-
Methods of Vaporization:
- Evaporation: In this method, the target material is heated until it vaporizes. This can be done using resistive heating, electron beams, or laser ablation.
- Sputtering: Sputtering involves bombarding the target material with high-energy ions, causing atoms to be ejected from the surface. These atoms then travel through the vacuum and deposit onto the substrate.
-
Types of PVD Coatings:
- Metal Coatings: PVD is commonly used to deposit metal coatings, such as titanium, chromium, or aluminum, onto various substrates. These coatings enhance the substrate's properties, such as hardness and corrosion resistance.
- Compound Coatings: PVD can also be used to deposit compound coatings, such as titanium nitride (TiN) or chromium nitride (CrN), which provide additional benefits like increased wear resistance and improved aesthetic appearance.
-
Applications of PVD:
- Industrial Applications: PVD is widely used in industries such as aerospace, automotive, and electronics to improve the performance and longevity of components. For example, PVD coatings are applied to cutting tools to enhance their wear resistance and extend their lifespan.
- Decorative Applications: PVD is also used in the decorative industry to create durable and aesthetically pleasing finishes on items like watches, jewelry, and architectural elements.
-
Advantages of PVD:
- Enhanced Material Properties: PVD coatings significantly improve the hardness, durability, and resistance to wear, corrosion, and oxidation of the substrate material.
- Precision and Control: The PVD process allows for precise control over the thickness and composition of the coating, resulting in high-quality and consistent results.
- Environmental Benefits: PVD is a relatively environmentally friendly process, as it typically does not involve the use of hazardous chemicals and produces minimal waste.
-
Limitations and Considerations:
- Cost and Complexity: PVD equipment and processes can be expensive and complex, requiring specialized knowledge and expertise to operate effectively.
- Substrate Compatibility: Not all materials are suitable for PVD coating. The substrate must be able to withstand the vacuum and high-energy conditions of the process without degrading.
In summary, physical vapor deposition (PVD) is a versatile and highly effective process for depositing thin films of material onto substrates. It offers numerous advantages, including enhanced material properties, precision, and environmental benefits, making it a valuable technique in various industrial and decorative applications. However, it also comes with certain limitations, such as cost and substrate compatibility, which must be carefully considered when selecting PVD as a coating method.
Summary Table:
Aspect | Details |
---|---|
Definition | Physical transformation of solid material into vapor for thin film coating. |
Process Environment | Vacuum or low-pressure, often with plasma activation. |
Vaporization Methods | Evaporation (heating) or sputtering (ion bombardment). |
Coating Types | Metal (e.g., titanium) and compound (e.g., TiN, CrN) coatings. |
Applications | Industrial (cutting tools) and decorative (watches, jewelry). |
Advantages | Enhanced hardness, precision, and environmental benefits. |
Limitations | High cost, complexity, and substrate compatibility concerns. |
Discover how PVD can transform your materials—contact our experts today!