Uniformity of the film refers to the consistency of the film's properties across the entire substrate. This primarily includes the thickness of the film but can also extend to other properties such as the index of refraction. Achieving uniform film deposition is critical in applications where consistent performance is required, such as in optical coatings, semiconductor devices, or protective layers. Understanding the specific requirements of the application helps in determining the acceptable levels of uniformity, ensuring that the film meets the desired performance criteria without over-specifying or under-specifying the uniformity requirements.
Key Points Explained:
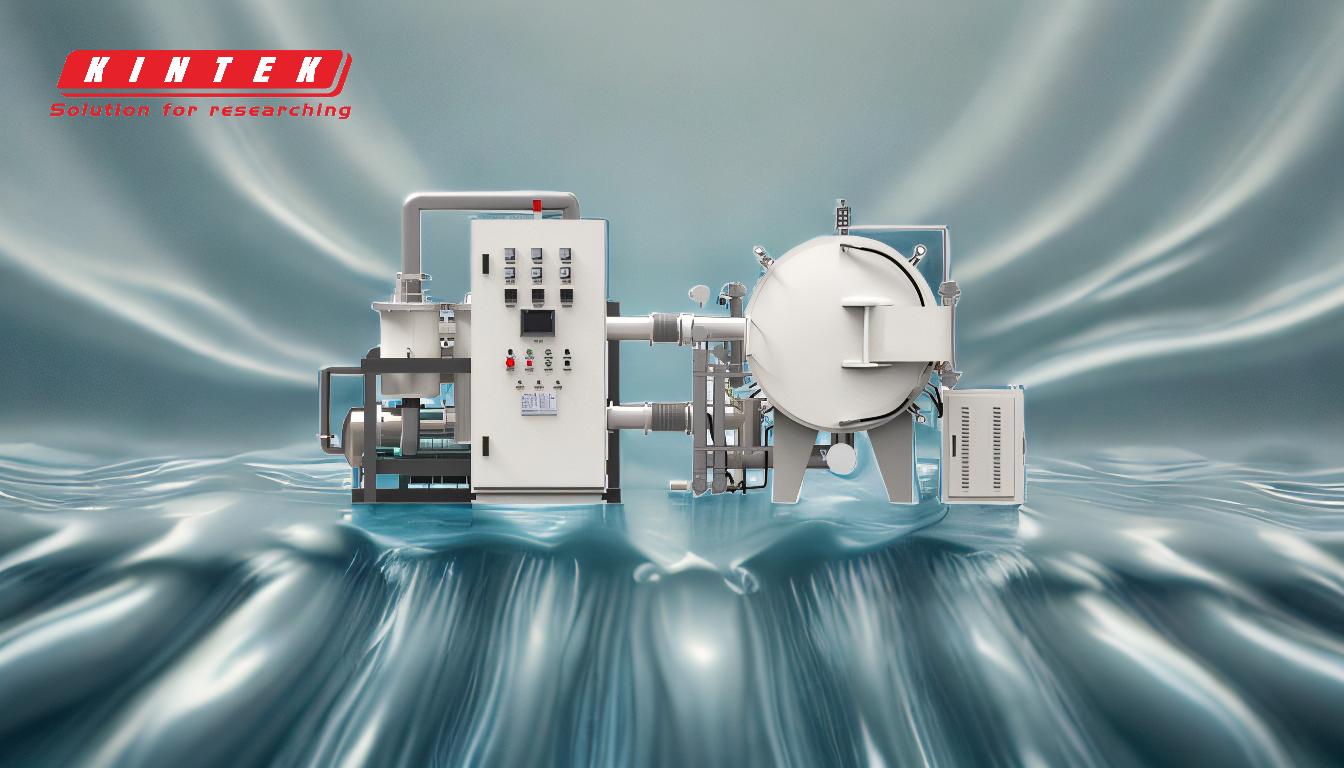
-
Definition of Film Uniformity:
- Film uniformity refers to the consistency of the film's properties across the substrate. This is most commonly measured in terms of thickness but can also include other properties like refractive index, density, or chemical composition.
- Uniformity is crucial because variations in these properties can lead to inconsistent performance in the final product, affecting functionality, durability, or optical characteristics.
-
Importance of Thickness Uniformity:
- Thickness uniformity is often the primary concern in thin film deposition. Variations in thickness can lead to:
- Optical Inconsistencies: In applications like anti-reflective coatings or mirrors, uneven thickness can cause variations in light transmission or reflection.
- Electrical Performance: In semiconductor devices, non-uniform thickness can affect electrical properties, leading to poor device performance.
- Mechanical Stability: In protective coatings, uneven thickness can result in weak spots, reducing the coating's effectiveness.
- Thickness uniformity is often the primary concern in thin film deposition. Variations in thickness can lead to:
-
Other Properties Affected by Uniformity:
- Refractive Index: In optical applications, the refractive index must be consistent across the film to ensure predictable light behavior.
- Density and Composition: Variations in density or chemical composition can affect the film's mechanical, thermal, or chemical properties, impacting its performance in specific applications.
-
Application-Specific Uniformity Requirements:
- Different applications have varying tolerance levels for uniformity. For example:
- High-Precision Optics: Requires extremely high uniformity to ensure consistent optical performance.
- Semiconductor Manufacturing: Needs precise control over thickness and composition to ensure reliable electrical properties.
- Protective Coatings: May tolerate slightly higher variations in uniformity, depending on the application's demands.
- Understanding the application helps in setting realistic and achievable uniformity specifications, avoiding unnecessary costs or performance issues.
- Different applications have varying tolerance levels for uniformity. For example:
-
Challenges in Achieving Uniformity:
- Achieving uniform film deposition can be challenging due to factors such as:
- Substrate Geometry: Complex or uneven substrates can make it difficult to achieve uniform deposition.
- Deposition Technique: Different deposition methods (e.g., sputtering, evaporation, chemical vapor deposition) have varying capabilities in terms of uniformity.
- Process Parameters: Factors like temperature, pressure, and deposition rate must be carefully controlled to ensure uniformity.
- Achieving uniform film deposition can be challenging due to factors such as:
-
Measuring and Specifying Uniformity:
- Uniformity is typically measured using techniques like profilometry, ellipsometry, or interferometry. The results are often expressed as a percentage variation across the substrate.
- When specifying uniformity, it's important to consider:
- Tolerance Levels: Define acceptable variations based on the application's requirements.
- Measurement Methods: Ensure that the chosen method is appropriate for the specific film properties being evaluated.
- Substrate Size and Shape: Larger or more complex substrates may require more stringent control to achieve uniform deposition.
-
Balancing Uniformity with Other Requirements:
- While uniformity is important, it must be balanced with other factors such as deposition rate, cost, and material properties. Over-specifying uniformity can lead to increased costs and complexity, while under-specifying can result in poor performance.
In summary, uniformity of the film is a critical parameter in thin film deposition, affecting the performance and reliability of the final product. By understanding the specific requirements of the application and carefully controlling the deposition process, it is possible to achieve the desired level of uniformity, ensuring consistent and reliable performance.
Summary Table:
Aspect | Details |
---|---|
Definition | Consistency of film properties (thickness, refractive index, etc.) across the substrate. |
Importance of Thickness | Ensures optical, electrical, and mechanical performance in applications. |
Other Affected Properties | Refractive index, density, and chemical composition. |
Application Requirements | Varies by industry: high-precision optics, semiconductors, protective coatings. |
Challenges | Substrate geometry, deposition techniques, and process parameters. |
Measurement Techniques | Profilometry, ellipsometry, interferometry. |
Balancing Uniformity | Must align with deposition rate, cost, and material properties. |
Need help achieving film uniformity for your application? Contact our experts today!