Microwave sintering is an advanced sintering technique that utilizes microwave energy to heat ceramic materials, enabling high-speed and efficient densification. This process involves placing the material in a furnace, evacuating gases, heating the material using microwave energy, maintaining the temperature for chemical reactions, and gradually cooling it. The use of susceptor plates and materials helps convert microwave energy into heat, making the process scalable for larger volumes. However, cooling the equipment can be challenging, often requiring auxiliary systems. This method is particularly advantageous for achieving precise control over material properties and reducing processing times.
Key Points Explained:
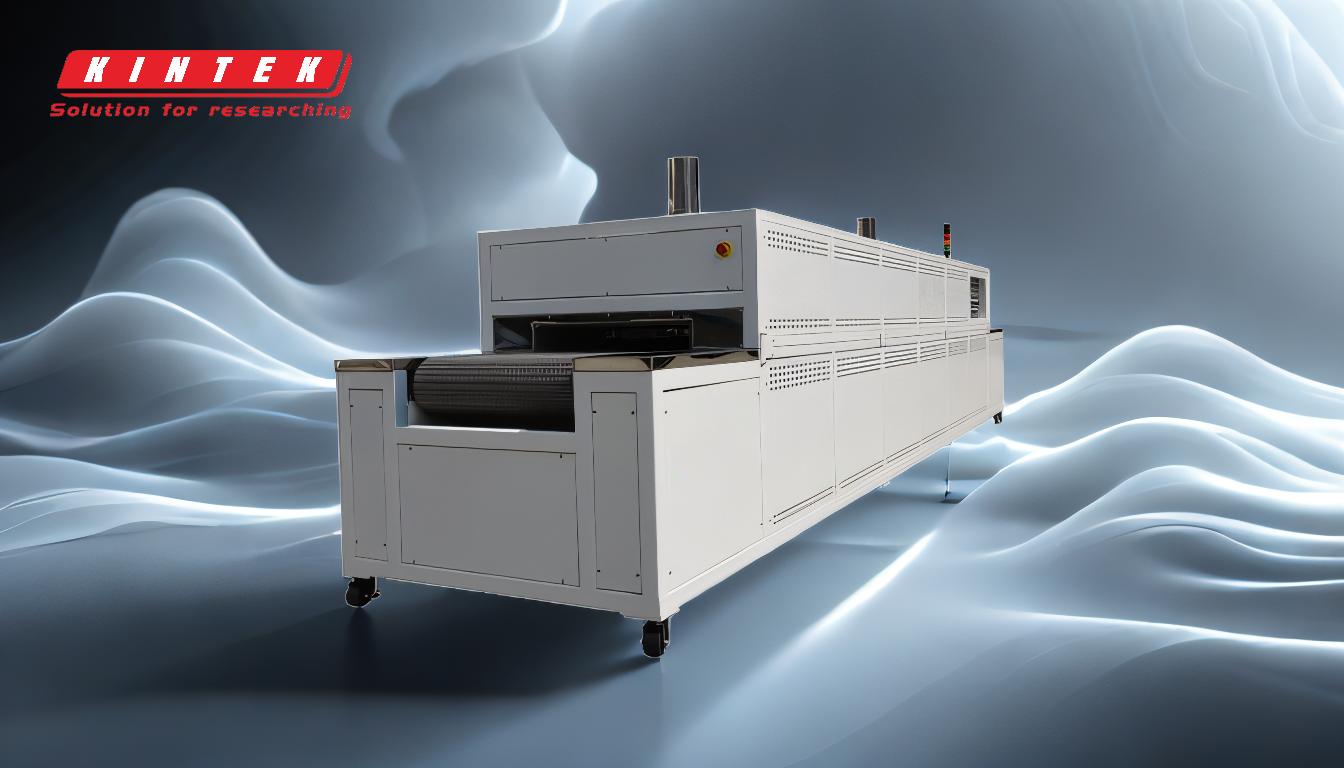
-
Definition and Purpose of Microwave Sintering
- Microwave sintering is a modern sintering method that uses microwave energy to heat ceramic materials, facilitating high-speed and efficient densification.
- It is particularly useful for achieving precise control over material properties and reducing processing times.
-
Components of a Microwave Sintering Furnace
- Microwave Source: Generates the microwave energy required for heating.
- Heating Cavity: The area where the material is placed and heated.
- Material Transfer System: Facilitates the movement of materials into and out of the furnace.
-
Steps in the Microwave Sintering Process
- Charging: The ceramic material is placed into the furnace.
- Vacuuming: The furnace is evacuated to remove gases and impurities, ensuring a clean environment for sintering.
- Microwave Heating: Microwave energy is used to heat the material to the sintering temperature, causing the material to densify.
- Insulation: The temperature is maintained for a specific period to allow chemical reactions and crystallization to occur.
- Cooling: The material is gradually cooled to room temperature to prevent thermal shock and ensure structural integrity.
-
Role of Susceptor Plates and Materials
- Susceptor plates and materials are used to absorb microwave energy and convert it into heat, which is then transferred to the ceramic material.
- This helps in achieving uniform heating and efficient sintering.
-
Advantages of Microwave Sintering
- High-Speed Sintering: The process is significantly faster than traditional sintering methods.
- Scalability: It can be scaled for larger volume production.
- Precision: Offers precise control over material properties, leading to improved product quality.
-
Challenges and Solutions
- Cooling the Equipment: The rapid heating process can make cooling the operating equipment challenging.
- Auxiliary Cooling Systems: These systems are often employed to manage the cooling process effectively, ensuring the longevity and efficiency of the equipment.
-
Applications and Benefits
- Microwave sintering is widely used in the production of advanced ceramics, including those used in electronics, aerospace, and biomedical applications.
- The process offers benefits such as reduced energy consumption, shorter processing times, and enhanced material properties.
By understanding these key points, one can appreciate the efficiency and precision of the microwave sintering process, making it a valuable technique in modern material science and engineering.
Summary Table:
Aspect | Details |
---|---|
Definition | Uses microwave energy to heat ceramic materials for densification. |
Key Components | Microwave source, heating cavity, material transfer system. |
Process Steps | Charging, vacuuming, microwave heating, insulation, cooling. |
Role of Susceptors | Convert microwave energy into heat for uniform heating. |
Advantages | High-speed sintering, scalability, precise material control. |
Challenges | Cooling equipment requires auxiliary systems. |
Applications | Advanced ceramics in electronics, aerospace, and biomedical fields. |
Learn how microwave sintering can transform your material processing—contact our experts today!