A muffle furnace is a specialized piece of equipment used to heat materials to extremely high temperatures in a controlled and isolated environment. It operates on the principle of indirect heating, where the material being heated is placed inside a separate chamber called a muffle, which is typically made of ceramic or other high-temperature-resistant materials. The heating elements are located outside the muffle, ensuring that the material is not directly exposed to the flame or heating coils. This design allows for precise temperature control, rapid heating, and efficient energy use, making it ideal for applications in chemistry, material science, and other fields where high-temperature processing is required without contaminating or damaging the sample.
Key Points Explained:
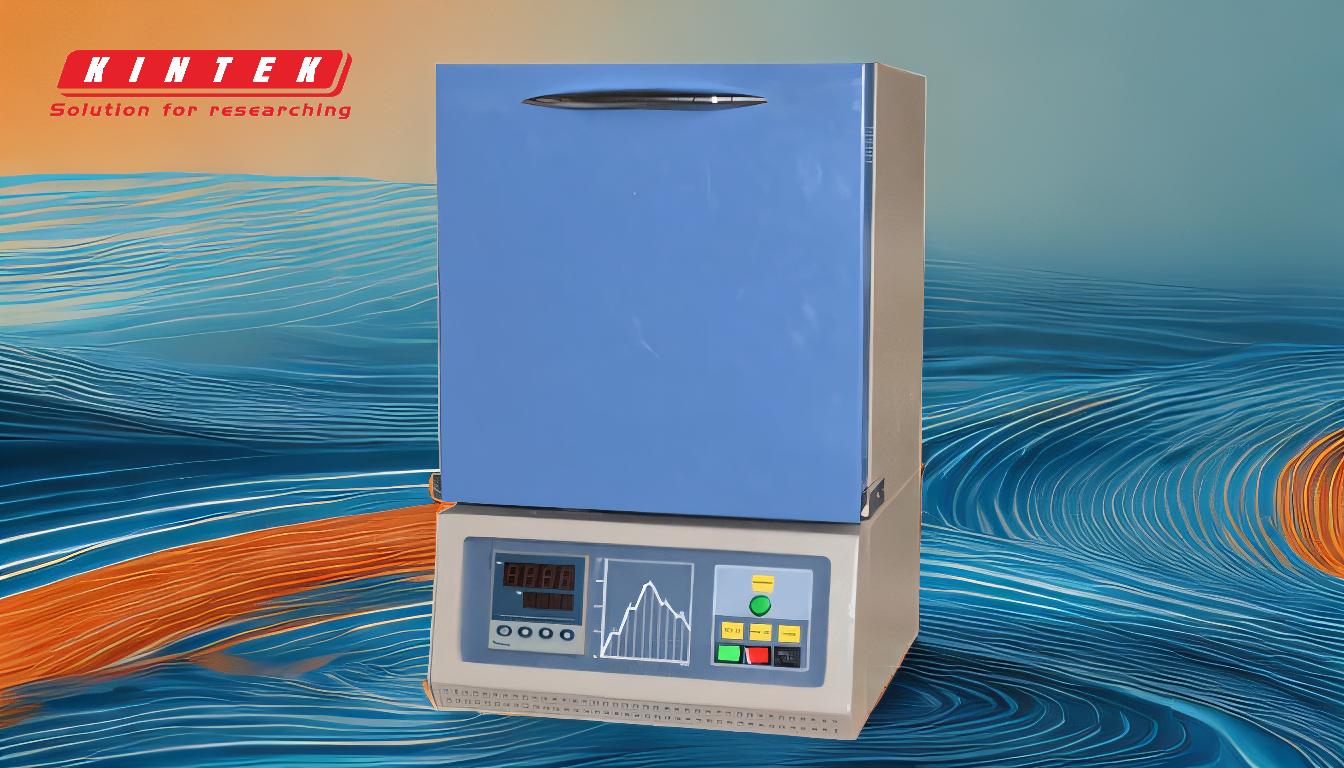
-
Definition and Purpose of a Muffle Furnace:
- A muffle furnace is an oven-type device designed to heat materials to high temperatures (often exceeding 1000°C) in a controlled environment.
- Its primary purpose is to isolate the material being heated from direct contact with flames or heating elements, ensuring that the sample remains uncontaminated and intact during the heating process.
- This makes it particularly useful in applications such as material testing, chemical analysis, and heat treatment processes.
-
Working Principle:
- The muffle furnace operates on the principle of indirect heating. The heating elements (usually electric coils) are placed outside the chamber where the material is housed.
- The material is placed inside a separate chamber called the muffle, which is made of high-temperature-resistant materials like ceramic (e.g., alumina).
- The muffle absorbs heat from the heating elements and transfers it to the material inside, ensuring uniform and controlled heating.
-
Key Components:
- Muffle Chamber: The inner chamber where the material is placed. It is made of ceramic or other refractory materials to withstand high temperatures and prevent contamination.
- Heating Elements: Typically made of high-resistance alloys like Kanthal or silicon carbide, these elements generate heat when an electric current passes through them.
- Insulation: The furnace is insulated with materials like ceramic fiber or refractory bricks to minimize heat loss and improve energy efficiency.
- Temperature Control System: Includes thermocouples and controllers to monitor and regulate the temperature inside the furnace accurately.
-
Advantages of Using a Muffle Furnace:
- Controlled Environment: The muffle isolates the material from external contaminants, ensuring clean and precise heating.
- High-Temperature Capability: Muffle furnaces can reach temperatures exceeding 1700°C, making them suitable for a wide range of high-temperature applications.
- Energy Efficiency: The insulated design and indirect heating mechanism reduce heat loss, making the furnace more energy-efficient.
- Versatility: Used in various industries, including metallurgy, ceramics, chemistry, and material science, for processes like annealing, sintering, ashing, and heat treatment.
-
Applications:
- Material Testing: Used to study the behavior of materials at high temperatures, such as thermal expansion, melting points, and phase transitions.
- Chemical Analysis: Employed in processes like ashing, where organic materials are burned off to analyze inorganic residues.
- Heat Treatment: Used for processes like annealing, tempering, and hardening of metals and alloys.
- Ceramics and Glass Manufacturing: Ideal for sintering ceramics and fusing glass at high temperatures.
-
Design Features:
- Compact and Self-Contained: Muffle furnaces are designed to be compact, with all components housed in a single cabinet for easy operation and maintenance.
- Rapid Heating and Cooling: The insulated design allows for quick heating and cooling cycles, improving productivity.
- Safety Features: Many modern muffle furnaces include safety features like over-temperature protection and automatic shut-off to prevent accidents.
-
Selection Criteria for Purchasers:
- Temperature Range: Choose a furnace that meets the required temperature range for your application.
- Chamber Size: Ensure the muffle chamber is large enough to accommodate your samples.
- Heating Rate: Consider the heating rate if rapid temperature changes are required.
- Control System: Look for precise temperature control and programmable settings for repeatability.
- Energy Efficiency: Opt for models with good insulation and energy-saving features to reduce operating costs.
By understanding the working principles, components, and applications of a muffle furnace, purchasers can make informed decisions when selecting the right equipment for their specific needs.
Summary Table:
Aspect | Details |
---|---|
Definition | Oven-type device for high-temperature heating in a controlled environment. |
Working Principle | Indirect heating via a ceramic muffle chamber. |
Key Components | Muffle chamber, heating elements, insulation, temperature control system. |
Advantages | Controlled environment, high-temperature capability, energy efficiency. |
Applications | Material testing, chemical analysis, heat treatment, ceramics manufacturing. |
Selection Criteria | Temperature range, chamber size, heating rate, control system, efficiency. |
Ready to enhance your lab’s capabilities? Contact us today to find the perfect muffle furnace for your needs!