Plasma-assisted physical vapor deposition (PAPVD) is an advanced thin-film coating technique that combines the principles of physical vapor deposition (PVD) with plasma activation. This method enhances the deposition process by using plasma to ionize and excite the vaporized material, improving adhesion, uniformity, and film quality. PAPVD is widely used in industries requiring high-performance coatings, such as aerospace, automotive, and electronics, due to its ability to produce durable, corrosion-resistant, and temperature-tolerant films at relatively low temperatures.
Key Points Explained:
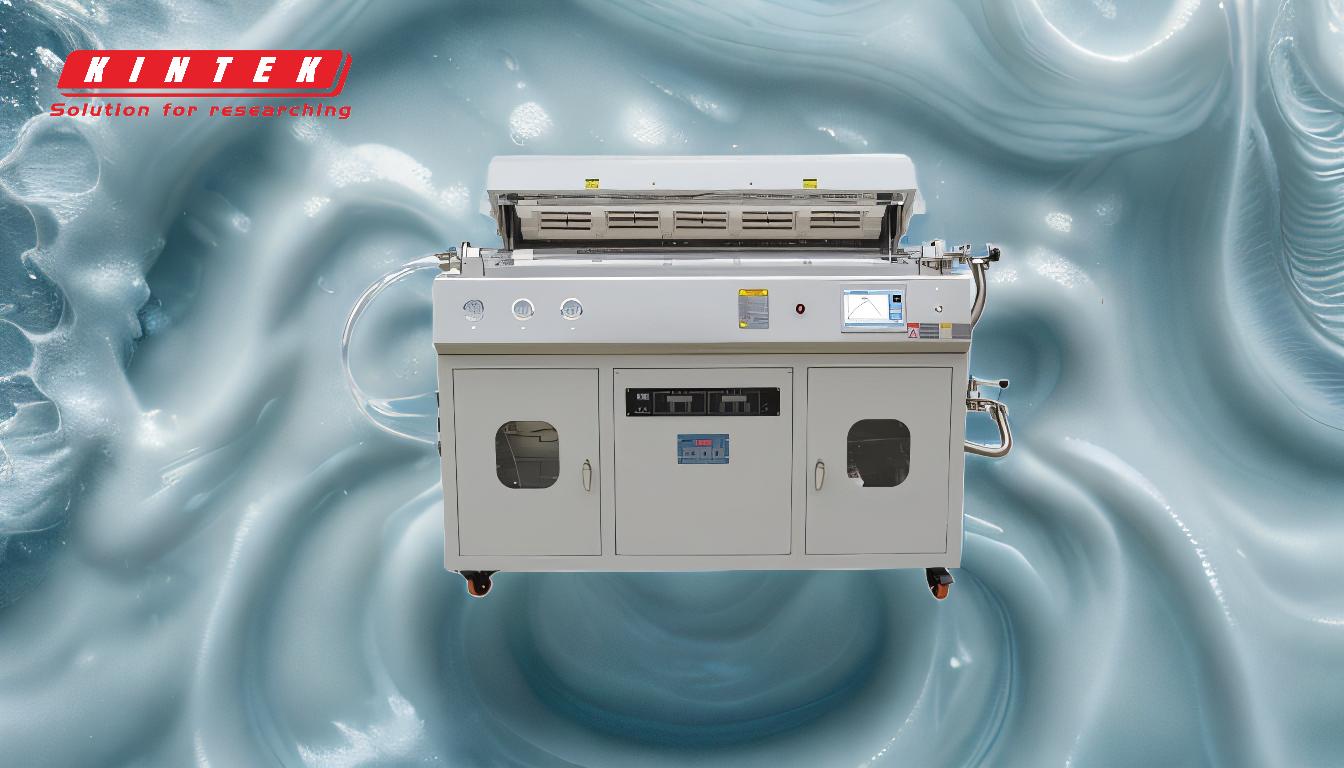
-
Definition of Plasma-Assisted Physical Vapor Deposition (PAPVD):
- PAPVD is a hybrid coating technique that integrates plasma activation with traditional PVD methods.
- It involves vaporizing a solid precursor material (e.g., metals or ceramics) and using plasma to ionize the vapor, enhancing the deposition process.
-
Core Principles of PAPVD:
- Vaporization: The solid precursor material is gasified using high-energy methods such as sputtering, thermal evaporation, or laser ablation.
- Plasma Activation: A plasma discharge (e.g., pulsed-glow or high-frequency) ionizes and excites the vaporized material, increasing its reactivity and energy.
- Deposition: The ionized vapor is transported to the substrate, where it condenses and forms a thin, uniform film.
-
Advantages of PAPVD:
- Lower Deposition Temperatures: Plasma activation allows deposition at temperatures as low as 200 °C, making it suitable for temperature-sensitive substrates.
- Improved Film Quality: Plasma enhances adhesion, density, and uniformity of the deposited film.
- Versatility: PAPVD can deposit a wide range of materials, including metals, ceramics, and composites.
- Durability: The resulting coatings are highly durable, corrosion-resistant, and capable of withstanding high temperatures.
-
Comparison with Traditional PVD:
- Energy Source: Traditional PVD relies solely on physical means (e.g., sputtering or evaporation) to vaporize the material, while PAPVD uses plasma to enhance the process.
- Film Properties: PAPVD produces films with better adhesion and uniformity compared to conventional PVD.
- Temperature Range: PAPVD operates at lower temperatures, reducing the risk of thermal damage to substrates.
-
Applications of PAPVD:
- Aerospace: Used for coating turbine blades and other components to improve wear resistance and thermal stability.
- Automotive: Applied to engine parts and tools to enhance durability and reduce friction.
- Electronics: Used for depositing thin films on semiconductors and optical components.
- Medical Devices: Coating implants and surgical tools to improve biocompatibility and corrosion resistance.
-
Process Steps in PAPVD:
- Preparation: The substrate is cleaned and placed in a vacuum chamber.
- Vaporization: The solid precursor material is vaporized using sputtering, evaporation, or laser ablation.
- Plasma Activation: A plasma discharge ionizes and excites the vaporized material.
- Deposition: The ionized vapor is transported to the substrate, where it condenses and forms a thin film.
- Post-Treatment: The coated substrate may undergo additional treatments (e.g., annealing) to optimize film properties.
-
Key Equipment and Consumables:
- Vacuum Chamber: Maintains a low-pressure environment for the deposition process.
- Plasma Source: Generates the plasma discharge (e.g., pulsed-glow or high-frequency).
- Target Material: The solid precursor material to be vaporized (e.g., metals, ceramics).
- Substrate Holder: Holds the substrate in place during deposition.
- Pumping System: Reduces background gases to prevent contamination of the film.
-
Challenges and Considerations:
- Complexity: PAPVD requires precise control of plasma parameters (e.g., power, frequency) to achieve optimal results.
- Cost: The equipment and consumables for PAPVD can be expensive compared to traditional PVD.
- Scalability: Scaling up the process for large-scale production can be challenging.
-
Future Trends in PAPVD:
- Nanostructured Coatings: Development of advanced coatings with nanoscale features for improved performance.
- Hybrid Processes: Integration of PAPVD with other techniques (e.g., chemical vapor deposition) to expand its capabilities.
- Sustainability: Use of environmentally friendly materials and processes to reduce the environmental impact of PAPVD.
By combining the physical principles of PVD with the reactive capabilities of plasma, PAPVD offers a powerful and versatile solution for producing high-performance thin films. Its ability to operate at lower temperatures and produce superior coatings makes it a valuable tool in modern manufacturing and materials science.
Summary Table:
Aspect | Details |
---|---|
Definition | Hybrid coating technique combining PVD with plasma activation. |
Core Principles | Vaporization, plasma activation, and deposition. |
Advantages | Lower deposition temperatures, improved film quality, versatility, durability. |
Applications | Aerospace, automotive, electronics, medical devices. |
Process Steps | Preparation, vaporization, plasma activation, deposition, post-treatment. |
Key Equipment | Vacuum chamber, plasma source, target material, substrate holder, pumping system. |
Challenges | Complexity, cost, scalability. |
Future Trends | Nanostructured coatings, hybrid processes, sustainability. |
Ready to explore PAPVD for your high-performance coating needs? Contact us today to learn more!