Plasma torch gasification is an advanced method for disposing of hazardous waste by converting it into useful byproducts like syngas, vitrified slag, and heat. This process uses a plasma torch, which generates extremely high temperatures (up to 10,000°C) to break down waste materials at the molecular level. The intense heat decomposes organic compounds into syngas (a mixture of hydrogen and carbon monoxide) and inorganic materials into a molten slag, which solidifies into a glass-like substance. This method is highly effective for treating hazardous waste, as it destroys toxic components, reduces volume, and minimizes environmental impact. It is particularly suitable for waste streams that are difficult to treat using conventional methods.
Key Points Explained:
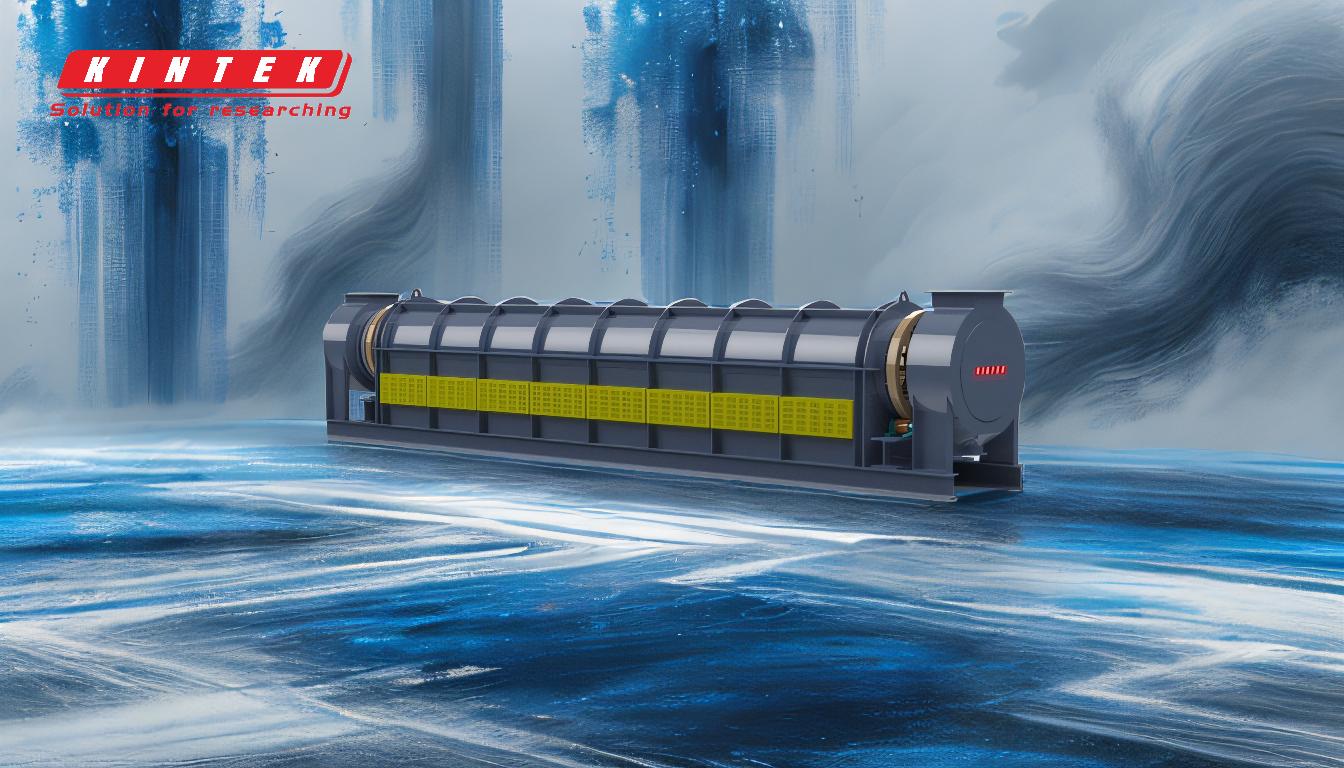
-
What is Plasma Torch Gasification?
- Plasma torch gasification is a thermal waste treatment process that uses a plasma torch to generate extremely high temperatures. This process is capable of breaking down hazardous waste into its basic molecular components, producing syngas, slag, and heat. The syngas can be used as a fuel, while the slag is inert and safe for disposal or use in construction materials.
-
How Does It Work?
- The process involves the following steps:
- Waste Preparation: Hazardous waste is fed into the gasification chamber, often after pre-treatment to ensure uniformity.
- Plasma Generation: A plasma torch ionizes gas (typically air, nitrogen, or argon) to create a high-temperature plasma arc.
- Thermal Decomposition: The plasma arc heats the waste to temperatures between 3,000°C and 10,000°C, breaking down organic materials into syngas and inorganic materials into molten slag.
- Syngas and Slag Recovery: The syngas is cleaned and can be used for energy generation, while the molten slag cools into a glassy, non-leachable material.
- The process involves the following steps:
-
Advantages of Plasma Torch Gasification:
- Destruction of Toxins: The high temperatures ensure complete destruction of hazardous organic compounds, including dioxins and furans.
- Volume Reduction: The process significantly reduces the volume of waste, with up to 95% volume reduction in some cases.
- Energy Recovery: Syngas produced can be used to generate electricity or as a chemical feedstock.
- Environmental Safety: The vitrified slag is non-toxic and can be safely used in construction or landfilled without risk of leaching.
-
Applications in Hazardous Waste Disposal:
- Plasma torch gasification is particularly effective for treating:
- Medical waste, including sharps and biohazardous materials.
- Chemical waste, such as pesticides and solvents.
- Industrial waste, including heavy metals and contaminated soils.
- Radioactive waste, where it can stabilize and reduce the volume of materials.
- Plasma torch gasification is particularly effective for treating:
-
Challenges and Considerations:
- High Initial Costs: The technology requires significant capital investment for equipment and infrastructure.
- Operational Complexity: The process demands skilled operators and precise control of temperature and gas composition.
- Energy Consumption: While it generates energy, the process itself is energy-intensive, especially for low-calorific waste.
-
Comparison with Other Waste Treatment Methods:
- Unlike incineration, plasma torch gasification operates in an oxygen-starved environment, reducing the formation of harmful byproducts like dioxins.
- Compared to landfilling, it offers a more sustainable solution by converting waste into usable resources and minimizing long-term environmental risks.
-
Future Prospects:
- Plasma torch gasification is gaining attention as a sustainable waste management solution, especially for hazardous and hard-to-treat waste. Advances in plasma technology and integration with renewable energy sources could further enhance its efficiency and environmental benefits.
In conclusion, plasma torch gasification is a cutting-edge technology for hazardous waste disposal, offering a safe, efficient, and environmentally friendly alternative to traditional methods. Its ability to convert waste into valuable resources makes it a promising solution for modern waste management challenges.
Summary Table:
Aspect | Details |
---|---|
Process | Uses a plasma torch to generate high temperatures (up to 10,000°C). |
Outputs | Syngas (fuel), vitrified slag (construction material), and heat. |
Advantages | Destroys toxins, reduces waste volume by up to 95%, and recovers energy. |
Applications | Medical, chemical, industrial, and radioactive waste disposal. |
Challenges | High initial costs, operational complexity, and energy-intensive process. |
Environmental Impact | Minimizes long-term risks, produces non-toxic slag, and reduces emissions. |
Interested in plasma torch gasification for your waste management needs? Contact us today to learn more!