Pressureless sintering is a type of sintering process where materials are compacted and formed into a solid mass using heat without the application of external pressure. This method relies on the diffusion of atoms across particle boundaries, causing them to fuse together and reduce porosity. It is particularly useful for materials with high melting points, such as ceramics and certain metals, and is widely used in powder metallurgy and ceramic manufacturing. Unlike pressure-assisted sintering, pressureless sintering does not require additional mechanical pressure, making it simpler and more cost-effective for certain applications. The process involves heating the material to a temperature below its melting point, allowing atomic diffusion to occur and resulting in a dense, cohesive structure.
Key Points Explained:
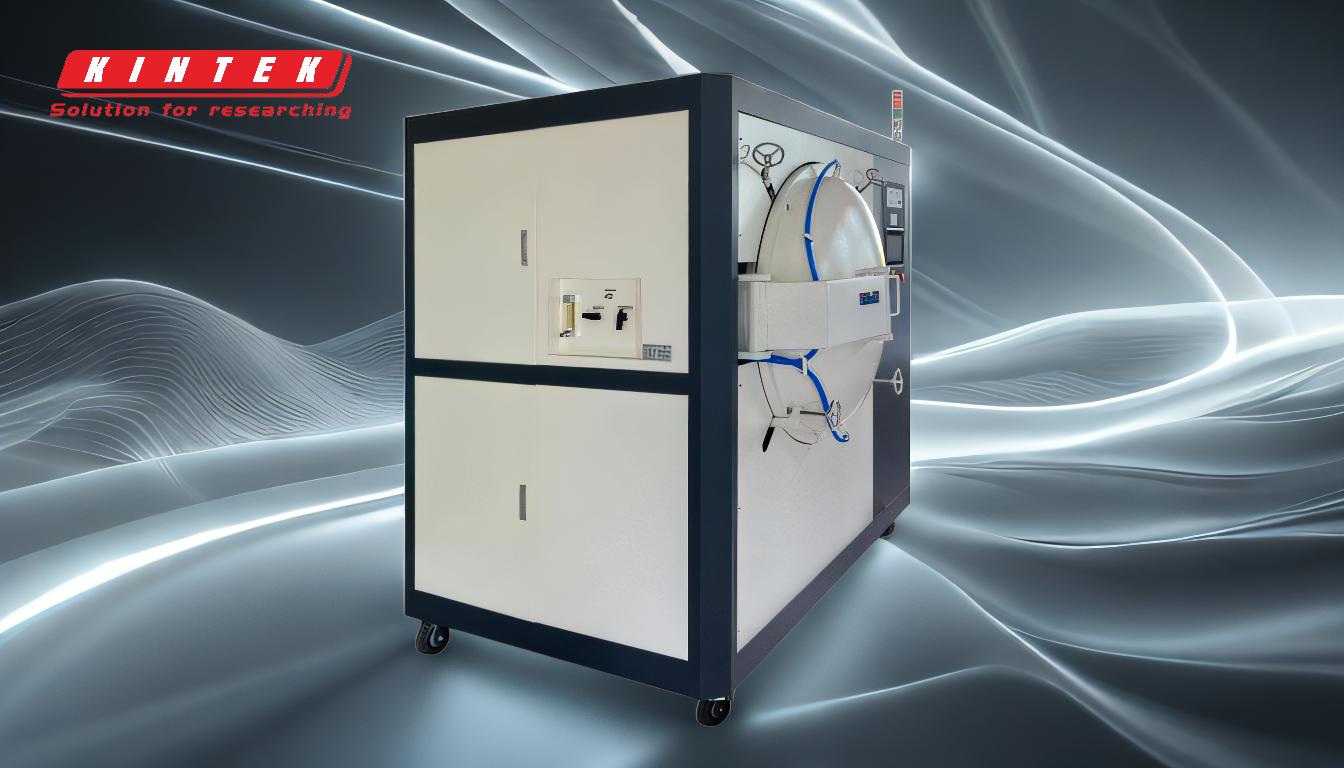
-
Definition of Pressureless Sintering:
- Pressureless sintering is a thermal process that consolidates powdered materials into a solid mass without the application of external pressure. It relies solely on heat to induce atomic diffusion and particle bonding.
- This method is commonly used for materials with high melting points, such as ceramics, tungsten, and molybdenum, where traditional melting and casting methods are impractical.
-
Mechanism of Pressureless Sintering:
- During pressureless sintering, the material is heated to a temperature below its melting point. At this temperature, atoms diffuse across particle boundaries, reducing porosity and forming a dense, solid structure.
- The process involves three main stages: initial particle bonding, densification through atomic diffusion, and final grain growth.
-
Comparison with Other Sintering Methods:
- Unlike pressure-assisted sintering, which requires external mechanical pressure to compact the material, pressureless sintering relies entirely on thermal energy.
- Compared to liquid-phase sintering, where a liquid phase aids in particle rearrangement and densification, pressureless sintering operates in a solid-state, making it suitable for materials that do not form a liquid phase at sintering temperatures.
-
Applications of Pressureless Sintering:
- Pressureless sintering is widely used in the manufacturing of ceramics, such as alumina, zirconia, and silicon carbide, due to their high melting points and the need for dense, strong structures.
- It is also employed in powder metallurgy for producing metal components, such as gears, bearings, and cutting tools, where high strength and wear resistance are required.
-
Advantages of Pressureless Sintering:
- The absence of external pressure simplifies the equipment and process, reducing costs and making it more accessible for industrial applications.
- It is suitable for producing complex shapes and large components, as the lack of pressure minimizes the risk of deformation or cracking during sintering.
-
Challenges and Limitations:
- Achieving full densification can be challenging in pressureless sintering, especially for materials with low atomic diffusion rates.
- The process may require longer sintering times or higher temperatures to achieve the desired density, which can increase energy consumption and production costs.
-
Process Parameters:
- Key parameters in pressureless sintering include sintering temperature, heating rate, and holding time. These factors influence the degree of densification, grain growth, and final material properties.
- The choice of sintering atmosphere (e.g., vacuum, inert gas, or reducing atmosphere) also plays a critical role in preventing oxidation and controlling the sintering behavior.
-
Future Developments:
- Advances in material science and sintering technology are focused on improving the efficiency and effectiveness of pressureless sintering. This includes the development of new additives and sintering aids to enhance densification and reduce sintering temperatures.
- Research is also exploring the use of advanced heating methods, such as microwave and spark plasma sintering, to achieve faster and more uniform sintering.
By understanding these key points, equipment and consumable purchasers can make informed decisions about the suitability of pressureless sintering for their specific applications, balancing cost, complexity, and performance requirements.
Summary Table:
Aspect | Details |
---|---|
Definition | Consolidates powdered materials using heat without external pressure. |
Mechanism | Relies on atomic diffusion to reduce porosity and form dense structures. |
Applications | Ceramics (alumina, zirconia), metals (tungsten, molybdenum), powder metallurgy. |
Advantages | Cost-effective, simple equipment, suitable for complex shapes. |
Challenges | Achieving full densification, longer sintering times, higher temperatures. |
Key Parameters | Sintering temperature, heating rate, holding time, sintering atmosphere. |
Discover how pressureless sintering can benefit your manufacturing process—contact our experts today!