In heat treatment, a protective atmosphere refers to a controlled environment created within a furnace to prevent unwanted chemical reactions, such as oxidation or decarburization, during the heating process. This is achieved by replacing the furnace's internal atmosphere with specific gases or gas mixtures that protect the metal parts being treated. The use of a protective atmosphere ensures that the metal retains its desired properties, such as hardness, strength, and wear resistance, while minimizing defects like surface scaling or contamination. Controlled atmospheres are essential for processes like carburization, annealing, and hardening, as they enable precise control over the material's surface chemistry and microstructure. The benefits include improved product quality, reduced material waste, and enhanced process efficiency.
Key Points Explained:
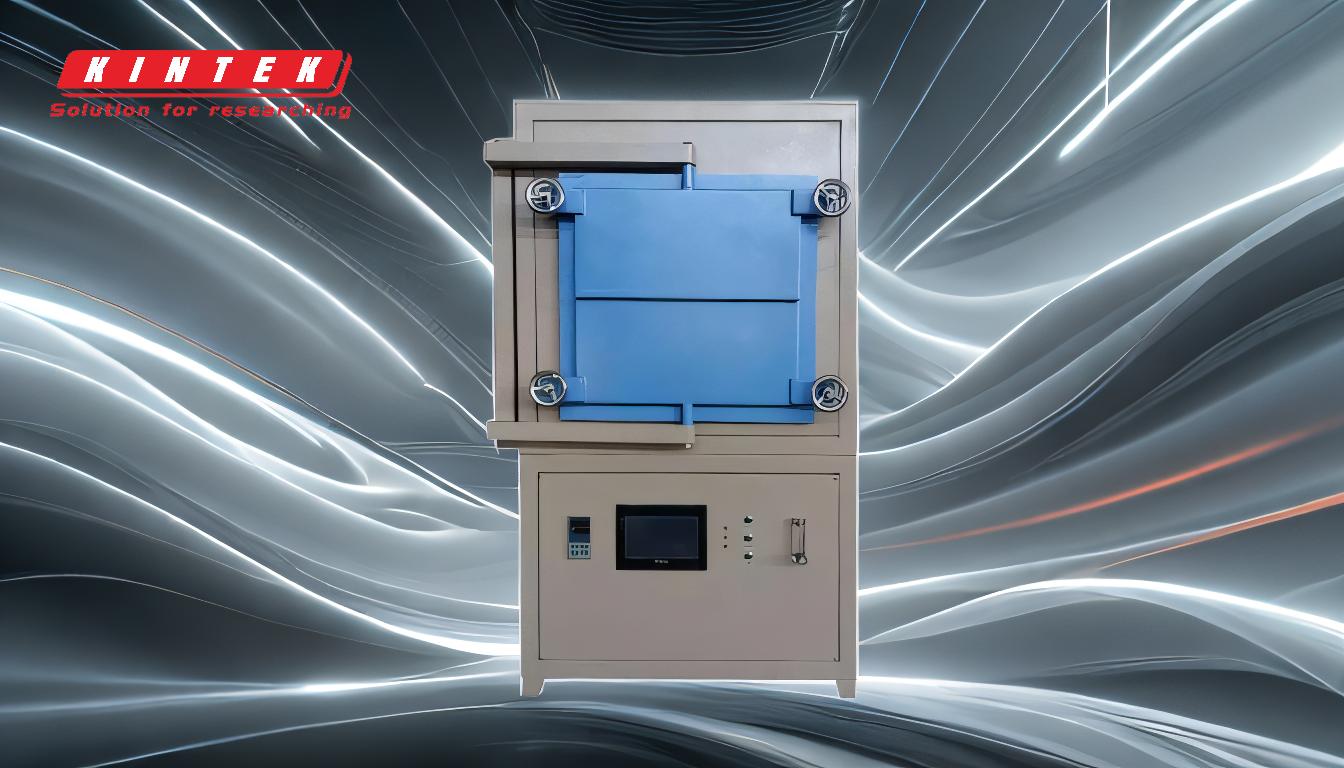
-
Purpose of a Protective Atmosphere:
- A protective atmosphere is used in heat treatment to create an environment that prevents oxidation, decarburization, or other undesirable chemical reactions. This is critical for maintaining the integrity and desired properties of the metal being treated.
- By replacing the furnace's internal atmosphere with inert or reactive gases, the process ensures that the metal surface remains free from contamination and retains its structural and mechanical properties.
-
Types of Protective Atmospheres:
- Inert Gases: Gases like nitrogen and argon are used to create an oxygen-free environment, preventing oxidation and scaling.
- Reactive Gases: Gases such as hydrogen or carbon-based mixtures (e.g., methane) are used for processes like carburization, where specific surface chemistry changes are required.
- Vacuum Atmospheres: In some cases, a vacuum is used to eliminate any gas interaction, ensuring a completely controlled environment.
-
Equipment for Creating Protective Atmospheres:
- Atmosphere Generators: These devices produce the necessary gases for heat treatment processes. They can generate protective atmospheres by breaking down natural gas or other sources into the required gas mixtures.
- Sealed Furnaces: Furnaces designed to contain and maintain the protective atmosphere, either through tight sealing or the use of retorts, ensure that the gas environment remains stable throughout the process.
-
Benefits of Using a Protective Atmosphere:
- Improved Material Properties: By preventing oxidation and decarburization, the protective atmosphere enhances the hardness, wear resistance, and strength of metal parts.
- Precision Control: It allows for precise control of surface carbon content, which is critical for processes like carburization and hardening.
- Reduced Material Waste: Minimizing surface defects and contamination reduces the need for rework or material replacement.
- Enhanced Process Efficiency: The controlled environment improves consistency and repeatability, leading to higher productivity and better working conditions.
-
Applications in Heat Treatment:
- Annealing: A protective atmosphere prevents oxidation and ensures uniform heating, resulting in improved ductility and reduced internal stresses.
- Carburization: The use of carbon-rich gases enhances surface hardness by increasing carbon content at the surface.
- Hardening and Tempering: Protective atmospheres prevent surface scaling and ensure consistent mechanical properties throughout the part.
-
Challenges and Solutions:
- Containment: Maintaining a stable protective atmosphere requires specialized equipment, such as sealed furnaces or retorts, to prevent gas leakage.
- Gas Purity: The quality of the protective atmosphere depends on the purity of the gases used, which may require additional filtration or purification systems.
- Cost: Implementing a protective atmosphere system can be expensive, but the long-term benefits in terms of product quality and reduced waste often justify the investment.
By understanding the role of a protective atmosphere in heat treatment, manufacturers can optimize their processes to achieve superior material properties, reduce defects, and improve overall efficiency.
Summary Table:
Aspect | Details |
---|---|
Purpose | Prevents oxidation, decarburization, and contamination during heat treatment. |
Types of Atmospheres | Inert gases (nitrogen, argon), reactive gases (hydrogen, methane), vacuum. |
Equipment | Atmosphere generators, sealed furnaces, retorts. |
Benefits | Improved material properties, precision control, reduced waste, efficiency. |
Applications | Annealing, carburization, hardening, and tempering. |
Challenges | Containment, gas purity, cost. |
Optimize your heat treatment process with a protective atmosphere—contact our experts today!