Pulsed DC sputtering frequency refers to the rate at which the power supply alternates between positive and negative voltage cycles during the sputtering process. Unlike RF (Radio Frequency) sputtering, which typically uses a fixed frequency of 13.56 MHz, pulsed DC sputtering operates at much lower frequencies, often in the range of tens to hundreds of kilohertz. This frequency determines how quickly the polarity of the target material switches, which in turn affects the deposition rate, film quality, and the ability to sputter insulating materials. Pulsed DC sputtering is particularly useful for depositing thin films on insulating substrates, as it helps mitigate issues like arcing and target poisoning.
Key Points Explained:
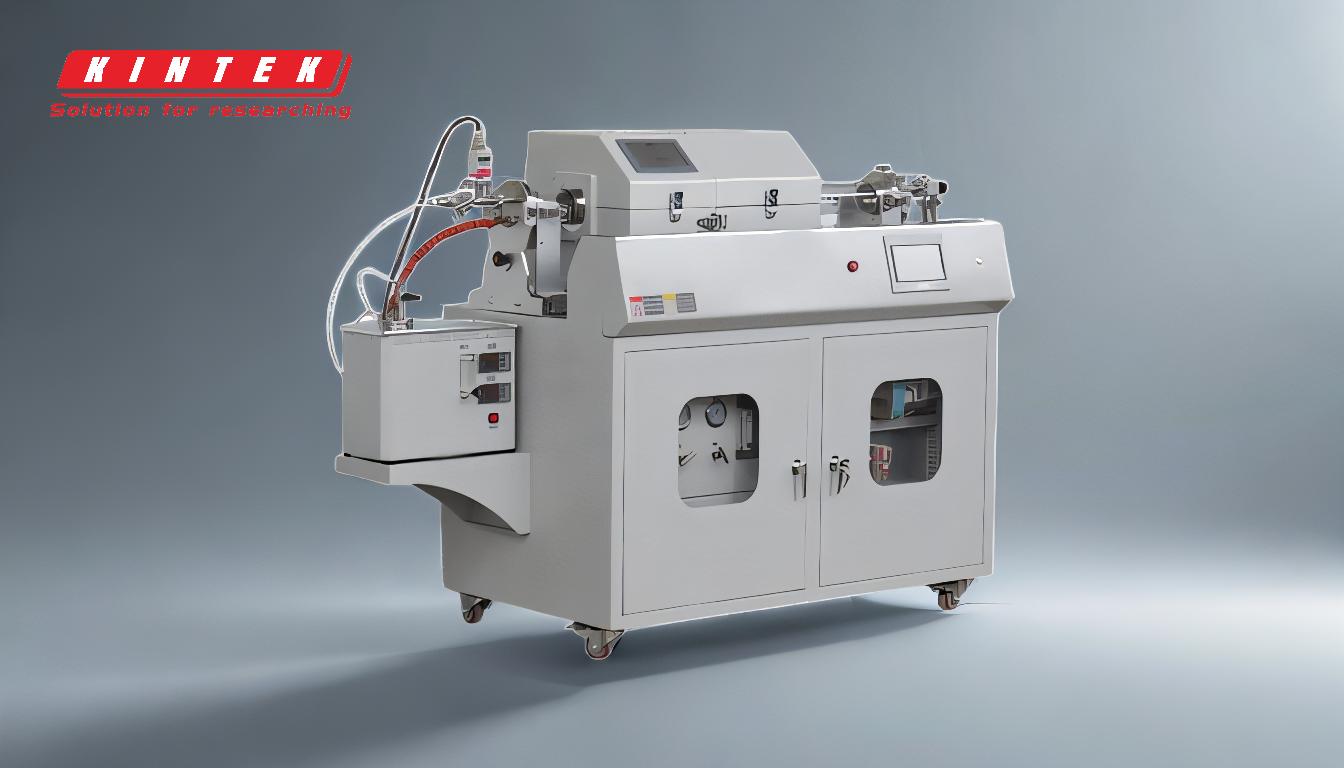
-
Definition of Pulsed DC Sputtering Frequency:
- Pulsed DC sputtering frequency is the rate at which the power supply alternates between positive and negative voltage cycles. This alternation helps in reducing issues like arcing and target poisoning, which are common in DC sputtering.
- The frequency is typically measured in kilohertz (kHz), ranging from tens to hundreds of kHz, which is significantly lower than the 13.56 MHz used in RF sputtering.
-
Comparison with RF Sputtering Frequency:
- RF sputtering uses a fixed frequency of 13.56 MHz, which is in the radio frequency range. This high frequency is effective for sputtering insulating materials but requires more complex and expensive equipment.
- Pulsed DC sputtering, on the other hand, operates at much lower frequencies, making it more cost-effective and easier to implement for certain applications, especially when dealing with conductive or semi-conductive materials.
-
Impact on Deposition Process:
- The frequency of the pulsed DC sputtering affects the deposition rate and the quality of the thin film. Higher frequencies can lead to smoother films but may also increase the risk of arcing.
- Lower frequencies are generally more stable and reduce the likelihood of arcing, but they may result in a slower deposition rate.
-
Applications and Advantages:
- Pulsed DC sputtering is particularly useful for depositing thin films on insulating substrates. The alternating polarity helps in preventing charge buildup on the target, which can lead to arcing and other issues.
- It is also advantageous for reactive sputtering processes, where the target material reacts with a gas to form a compound film. The pulsed nature of the process helps in maintaining a stable plasma and reducing target poisoning.
-
Technical Considerations:
- When selecting a pulsed DC sputtering frequency, it is important to consider the material being sputtered, the desired film properties, and the specific requirements of the application.
- The frequency should be optimized to balance deposition rate, film quality, and process stability. This often involves experimental testing and fine-tuning of the sputtering parameters.
-
Future Trends:
- Advances in power supply technology are enabling more precise control over pulsed DC sputtering frequencies, allowing for better optimization of the deposition process.
- There is also growing interest in combining pulsed DC sputtering with other techniques, such as magnetron sputtering, to further enhance film quality and deposition efficiency.
In summary, pulsed DC sputtering frequency is a critical parameter that influences the efficiency and quality of the thin film deposition process. By carefully selecting and optimizing this frequency, manufacturers can achieve better control over the sputtering process, leading to higher-quality films and more reliable production outcomes.
Summary Table:
Aspect | Pulsed DC Sputtering | RF Sputtering |
---|---|---|
Frequency Range | Tens to hundreds of kHz | Fixed at 13.56 MHz |
Cost | More cost-effective | More expensive |
Applications | Ideal for insulating substrates | Effective for insulating materials |
Deposition Rate | Slower at lower frequencies, smoother films | Faster but higher risk of arcing |
Stability | More stable, reduces arcing | Less stable, prone to arcing |
Target Poisoning | Mitigated by alternating polarity | More likely in reactive processes |
Discover how pulsed DC sputtering can enhance your thin film processes—contact our experts today for tailored solutions!