PVD color coating refers to the application of a thin, durable film on surfaces using the Physical Vapor Deposition (PVD) process. This technique involves vaporizing solid materials in a vacuum environment, which then condense to form a thin film on the target substrate. The resulting coatings can exhibit a range of colors, including gold, rose gold, black, and more, depending on the materials used. PVD coatings are known for their durability, resistance to corrosion, and aesthetic appeal, making them popular in industries such as jewelry, automotive, and consumer electronics.
Key Points Explained:
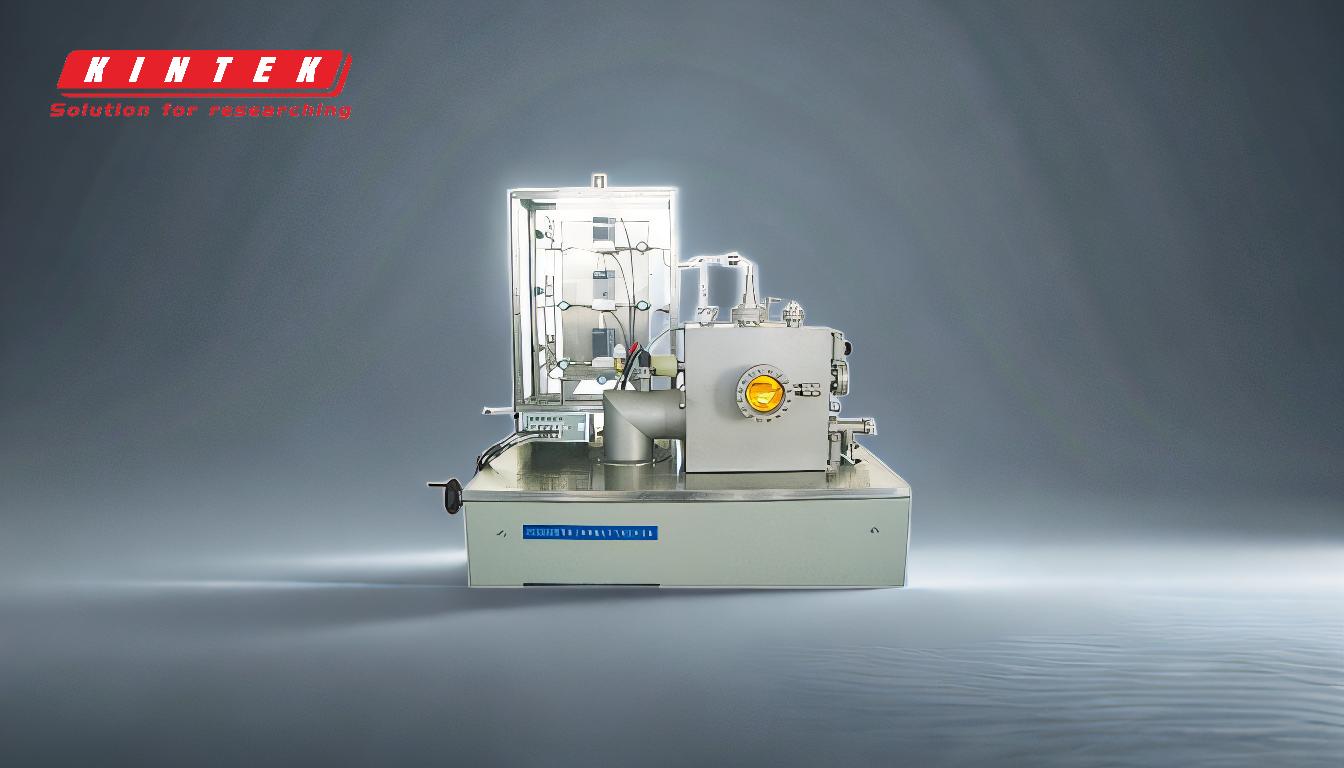
-
What is PVD Coating?
- PVD stands for Physical Vapor Deposition, a process used to apply thin films to various substrates.
- The process involves vaporizing a solid material in a vacuum and depositing it onto the target surface, creating a durable and uniform coating.
-
Materials Used in PVD Coating
- Common materials include chromium, titanium nitride, and specially treated alloys.
- These materials are chosen for their ability to produce specific colors and enhance the durability of the coating.
-
Colors Produced by PVD Coating
- PVD coatings can produce a wide range of colors, including but not limited to gold, rose gold, black, and bronze.
- The color is determined by the type of material used and the specific conditions of the PVD process.
-
Applications of PVD Color Coating
- Jewelry: PVD coatings are used to create durable and attractive finishes on rings, watches, and other accessories.
- Automotive: The process is used to coat car parts, providing both aesthetic appeal and protection against wear and corrosion.
- Consumer Electronics: PVD coatings are applied to smartphones, laptops, and other devices to enhance their appearance and durability.
-
Advantages of PVD Coating
- Durability: PVD coatings are highly resistant to wear, corrosion, and tarnishing.
- Aesthetic Appeal: The process allows for a wide range of colors and finishes, making it ideal for decorative applications.
- Environmental Friendliness: PVD is a clean process that produces minimal waste and does not involve harmful chemicals.
-
Process of PVD Coating
- Preparation: The substrate is cleaned and prepared to ensure proper adhesion of the coating.
- Vaporization: The coating material is vaporized in a vacuum chamber.
- Deposition: The vaporized material condenses on the substrate, forming a thin, uniform film.
- Finishing: The coated product may undergo additional treatments to enhance its properties or appearance.
-
Comparison with Other Coating Methods
- Electroplating: PVD coatings are generally more durable and environmentally friendly compared to electroplating.
- Anodizing: While anodizing is effective for aluminum, PVD offers more versatility in terms of materials and colors.
In summary, PVD color coating is a versatile and durable method for applying thin, decorative, and protective films to various materials. Its ability to produce a wide range of colors and finishes makes it a popular choice in multiple industries. The process is not only effective but also environmentally friendly, contributing to its growing adoption in modern manufacturing and design.
Summary Table:
Aspect | Details |
---|---|
What is PVD Coating? | A process to apply thin, durable films using Physical Vapor Deposition. |
Materials Used | Chromium, titanium nitride, and treated alloys for specific colors. |
Common Colors | Gold, rose gold, black, bronze, and more. |
Applications | Jewelry, automotive parts, consumer electronics. |
Advantages | Durable, corrosion-resistant, eco-friendly, and aesthetically versatile. |
Process | Preparation, vaporization, deposition, and finishing. |
Interested in enhancing your products with PVD coatings? Contact us today to learn more!