PVD fabric refers to materials or surfaces that have been treated using Physical Vapor Deposition (PVD) technology. PVD is a vacuum-based coating process that deposits thin films of materials, such as metals, oxides, nitrides, and carbides, onto a substrate. This process enhances the fabric's properties, including durability, corrosion resistance, and aesthetic appeal. PVD coatings are known for their ability to create ultra-thin, high-performance layers that improve the fabric's resistance to environmental factors like humidity, UV exposure, and chemical staining. While PVD-treated fabrics offer exceptional performance benefits, they are also vulnerable to damage from abrasion or impact due to the thinness of the coating.
Key Points Explained:
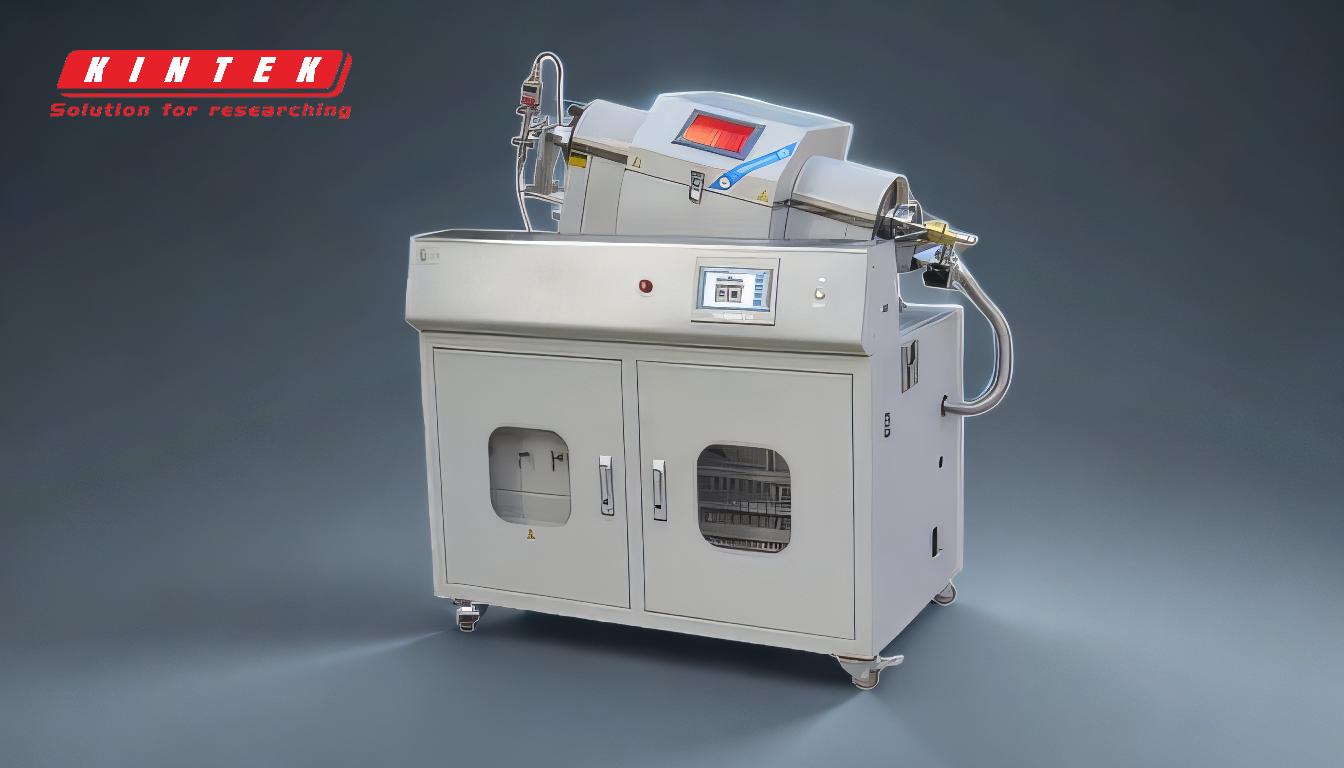
-
What is PVD Fabric?
- PVD fabric refers to textiles or surfaces coated using Physical Vapor Deposition (PVD), a vacuum-based process that deposits thin films of materials like metals, oxides, nitrides, and carbides.
- The process enhances the fabric's functional and aesthetic properties, making it suitable for applications requiring durability and resistance to environmental factors.
-
How PVD Coating Works
- PVD involves vaporizing a solid material in a vacuum and depositing it atom by atom onto the fabric surface.
- This creates ultra-thin coatings (as thin as 20 nm) that are highly uniform and reliable.
- The process operates at low temperatures (below 250 °C), preserving the fabric's core microstructure and mechanical properties.
-
Benefits of PVD Fabric
- Durability: PVD coatings are extremely hard, providing resistance to scratching, chipping, and corrosion.
- Aesthetic Appeal: The process allows for a wide range of colors and high-gloss finishes, enhancing the fabric's appearance.
- Environmental Resistance: PVD-treated fabrics resist UV exposure, humidity, and chemical staining, making them suitable for harsh environments.
- High-Temperature Tolerance: The coatings can withstand high temperatures without degrading or separating from the substrate.
- Eco-Friendly: PVD is an environmentally friendly process that produces no harmful byproducts.
-
Applications of PVD Fabric
- Decorative Products: PVD is widely used in decorative applications due to its ability to create visually appealing finishes.
- High-Humidity Environments: The exceptional corrosion resistance makes it ideal for applications in humid or marine settings.
- Functional Textiles: PVD-treated fabrics are used in industries requiring durable, high-performance materials, such as automotive, aerospace, and medical textiles.
-
Limitations of PVD Fabric
- Thin Coatings: While the thinness of PVD coatings is a benefit, it also makes the fabric vulnerable to damage from abrasion, impact, or rough handling.
- Process Maturity: Current PVD technology, while advanced, is still evolving, particularly in areas like in-situ doping and cold wall deposition.
-
Why Choose PVD Fabric?
- PVD fabric combines aesthetic and functional benefits, making it a versatile choice for industries requiring both durability and visual appeal.
- Its eco-friendly nature and ability to enhance material properties without altering core characteristics make it a preferred coating method for modern textiles.
In summary, PVD fabric represents a cutting-edge application of PVD technology, offering a unique combination of durability, aesthetic versatility, and environmental resistance. While it has some limitations, its benefits make it a valuable option for a wide range of industries and applications.
Summary Table:
Aspect | Details |
---|---|
What is PVD Fabric? | Textiles or surfaces coated using Physical Vapor Deposition (PVD) technology. |
Benefits | Durability, corrosion resistance, aesthetic appeal, eco-friendly. |
Applications | Decorative products, high-humidity environments, functional textiles. |
Limitations | Vulnerable to abrasion, impact, and evolving technology. |
Interested in PVD fabric for your industry? Contact us today to learn more!