Physical vapor deposition (PVD) is a group of thin film deposition techniques that involve vaporizing a solid material in a vacuum and then depositing that material onto a substrate. This process is widely used in modern industries for applications such as high-temperature coatings, conductive surfaces, and durable coatings on complex shapes. PVD offers advantages like the ability to deposit a wide range of materials, precise control over the deposition process, and improved film properties. However, PVD films are very thin and can be vulnerable to damage from abrasion, impact, or chemical staining. The process involves three key steps: vaporization, migration, and deposition, and it is known for being environmentally friendly and producing high-quality, pure coatings.
Key Points Explained:
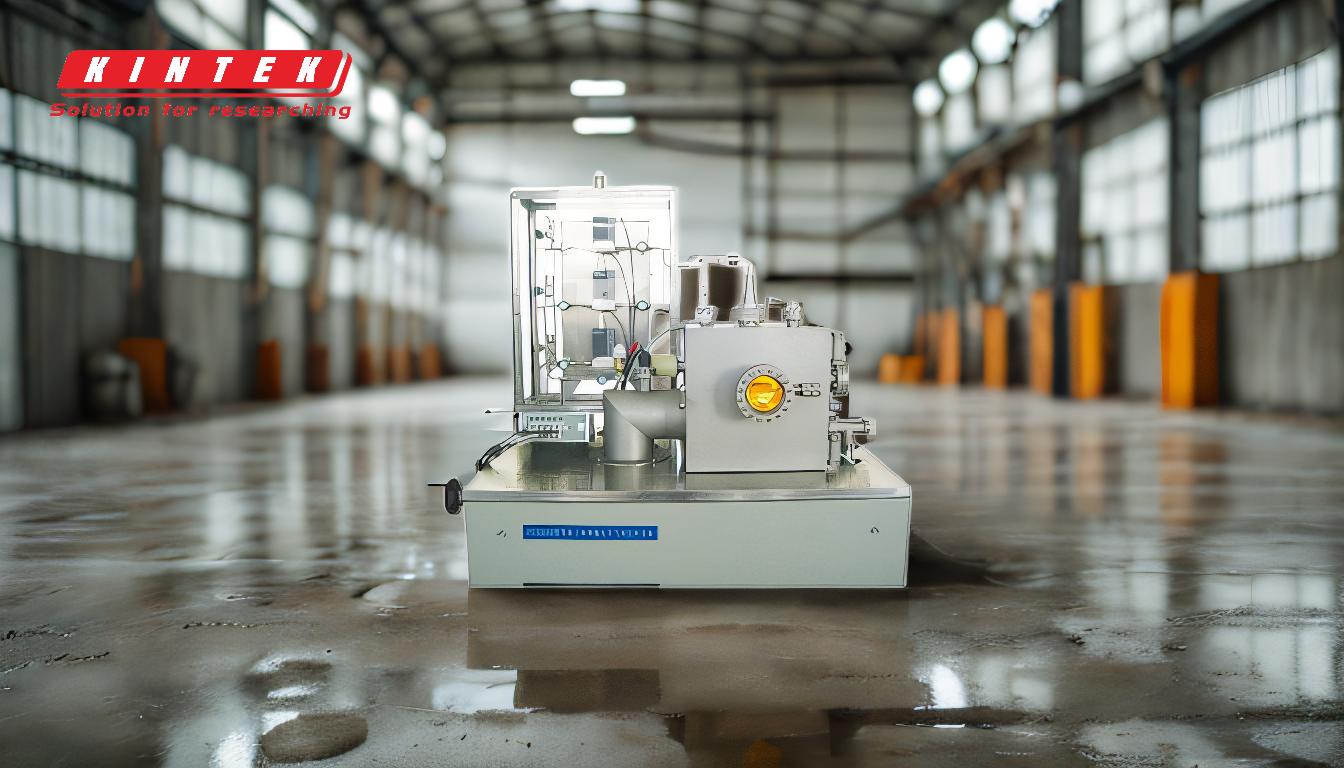
-
Definition of PVD:
- PVD stands for Physical Vapor Deposition, a group of techniques used to deposit thin films onto substrates.
- The process involves vaporizing a solid material in a vacuum and then depositing it onto a substrate.
-
Key Steps in PVD:
- Vaporization: The solid material is vaporized, transitioning from a condensed phase to a gas phase.
- Migration: The vaporized atoms or molecules travel through the vacuum chamber.
- Deposition: The vaporized material condenses onto the substrate, forming a thin film.
-
Advantages of PVD:
- Wide Range of Materials: PVD can deposit a variety of materials, including metals, alloys, and compounds.
- Control and Precision: The process allows for precise control over film thickness and properties.
- Improved Film Properties: PVD films often have better adhesion, uniformity, and durability compared to other deposition methods.
- Environmental Friendliness: PVD is a clean process that produces minimal waste and does not require harmful chemicals.
-
Applications of PVD:
- High-Temperature Coatings: Used in industries where materials need to withstand extreme temperatures.
- Conductive Surfaces: Applied in electronics and semiconductors for creating conductive layers.
- Durable Coatings: Used to enhance the durability and appearance of products, such as tools, automotive parts, and consumer electronics.
-
PVD Sputtering:
- A specific type of PVD where a target material is bombarded with high-energy ions (typically argon gas ions) to vaporize atoms from the target.
- The vaporized atoms then travel through a vacuum chamber and condense onto the substrate, forming a thin film.
-
Characteristics of PVD:
- Vacuum Chamber Processing: PVD is performed in a vacuum to ensure a clean environment and prevent contamination.
- Temperature Range: Typically processed at temperatures between 320 to 900 degrees Fahrenheit.
- Line of Sight Coating: The coating process is directional, meaning the substrate must be in the direct line of sight of the vaporized material.
- Physical Bonding: The coating forms a physical bond with the substrate, rather than a chemical one.
- Thin Films: PVD films are very thin, typically ranging from 0.00004 to 0.0002 inches in thickness.
- Material Versatility: PVD can be used with a wide range of materials, including metals, ceramics, and polymers.
- Tight Tolerances: Recommended for applications requiring precise control over film thickness and properties.
- No Heat Treatment: Unlike some other coating processes, PVD does not require post-deposition heat treatment.
- Replication of Finish: The coating replicates the surface finish of the substrate, making it ideal for decorative applications.
-
Limitations of PVD:
- Vulnerability to Damage: Due to their thin nature, PVD films can be susceptible to damage from abrasion, impact, or chemical exposure.
- Cost and Complexity: The equipment and process can be expensive and complex, requiring specialized knowledge and maintenance.
-
Materials Deposited via PVD:
- PVD can deposit a variety of materials, including:
- Titanium Nitride (TiN): Commonly used for wear-resistant coatings.
- Zirconium Nitride (ZrN): Known for its decorative gold-like appearance and durability.
- Silicon Dioxide (SiO2): Used in optical coatings and semiconductor applications.
- Tungsten Silicide (WSi2): Applied in semiconductor devices for its conductive properties.
- PVD can deposit a variety of materials, including:
-
Environmental and Surface Quality Benefits:
- Pure Coatings: PVD produces coatings with high purity, free from contaminants.
- Improved Surface Quality: The process enhances the surface properties of the substrate, such as hardness, wear resistance, and corrosion resistance.
In summary, PVD is a versatile and precise thin film deposition technique with a wide range of applications across various industries. Its ability to produce high-quality, durable coatings makes it a valuable process, despite some limitations related to the thinness of the films and the complexity of the equipment.
Summary Table:
Aspect | Details |
---|---|
Definition | Thin film deposition technique involving vaporization and deposition. |
Key Steps | Vaporization, migration, deposition. |
Advantages | Wide material range, precise control, improved film properties, eco-friendly. |
Applications | High-temperature coatings, conductive surfaces, durable coatings. |
Materials Deposited | TiN, ZrN, SiO2, WSi2. |
Limitations | Thin films vulnerable to damage; high cost and complexity. |
Discover how PVD can enhance your product's performance—contact our experts today!